An electric Deere. Part two
An electric Deere, second chapter. Philippe Contault, JDPS Marketing Communication Manager, explained to us and to all of you, what ‘alternative’ really means for John Deere Power Systems. Are the advantages of electrification of power transmission only constructive (e.g. freedom in the positioning of components, ease of power transmission between non-neighbouring components) or are there […]
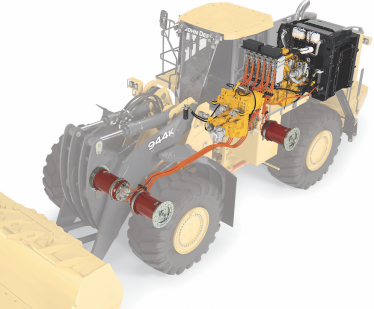
An electric Deere, second chapter. Philippe Contault, JDPS Marketing Communication Manager, explained to us and to all of you, what ‘alternative’ really means for John Deere Power Systems.
Are the advantages of electrification of power transmission only constructive (e.g. freedom in the positioning of components, ease of power transmission between non-neighbouring components) or are there advantages also in the flexibility and mode of power and torque transmission?
There are certainly additional advantages when integrating electric drive components.
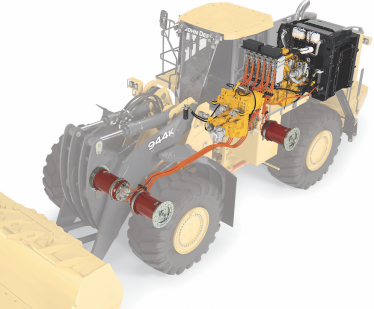
An electric Deere. An expandable and scalable architecture
The power electronics designed and developed by John Deere Electronic Solutions make it possible for expandable and scalable electrification architectures, allowing engineers to manage power in innovative ways. For example, traction power can be distributed across multiple motors while controlling them independently. Or, for power generation, systems aren’t limited to a single e-machine motor generator or size. Power electronics make it possible to run a series of smaller e-machine motor generators in parallel and then combine power to one electrical BUS for downstream use. Another benefit of is the additional flexibility y of implementing electrification within existing vehicle designs. Rather than a one-size-fits-all solution, John Deere components can be configured specifically for various OEM applications. Our engineers have identified key electric drivetrain components that will integrate into an existing space claim where conventional mechanical drivetrain components exist to minimize changes to the vehicle chassis. The John Deere 644K Hybrid Wheel Loader uses 6.8L engines rather than the 9.0L engine used in comparable applications, increasing packaging flexibility. Operation is made easier and quieter with electric drive components, offering 3dBa sound reduction, and the ability to run at maximum efficiency.
The diesel electric solution in this application delivers all the benefits expected of electrification — improved fuel efficiency, reduced noise, lower operating costs, and reliable power — but with the added durability that’s expected from John Deere.
Let’s talk about the Electric Motor Drive – EMD-100-1. Currently, JD offers only 100kW power version. Are other powers expected in the future?
As far as additional powers, we are continually working with OEMs to understand their development requirements. John Deere evaluates opportunities to provide customers with the appropriate components and power solutions to meet application needs.
One of the advantages of the electric is being able to release (within certain limits) speed and torque output. How has the constant torque section been defined?
Our electric drivetrain components have been designed to take full advantage of the high torque available at low speeds while also balancing power at high speed conditions.