Battery Technology Center (BTC) officially opened at the Mercedes-Benz plant in Mannheim
Andreas Gorbach, Member of the Board of Management of Daimler Truck and responsible for Truck Technology: “The opening of our Battery Technology Center is an important step in terms of electrifying our product portfolio. We have decided to take care of the assembly of the future battery generation ourselves and thus keep important added value in-house.”
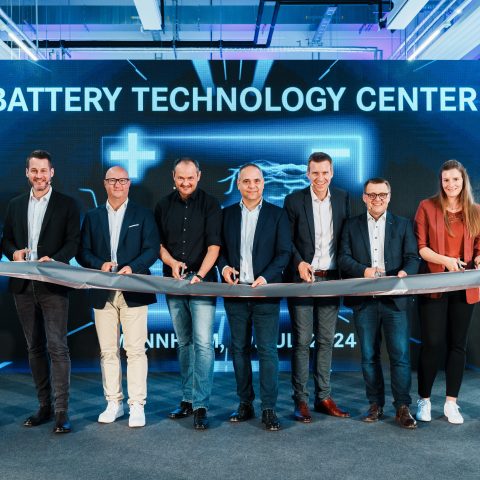
Around a year after the topping-out ceremony, Daimler Truck officially opened the Battery Technology Center (BTC) at the Mercedes-Benz plant in Mannheim on July 19.
Daimler Truck’s product and process development for battery electric commercial vehicles is carried out on an area of over 10,000 square meters: the BTC combines development with production. Experts build up knowledge about batteries and their production processes here. To this end, two production areas will be created in the BTC, which was still called InnoLab Battery at the topping-out ceremony. On the one hand, cells will be produced here on a pilot basis in order to build up process knowledge. Secondly, battery packs will be manufactured as prototypes for test benches and test vehicles. With the pilot line for battery packs, the Mannheim site is preparing for future series production, which is planned for the second half of the decade as part of the introduction of the next generation of lithium-ion batteries at the plant.
Andreas Gorbach, Member of the Board of Management of Daimler Truck and responsible for Truck Technology: “The opening of our Battery Technology Center is an important step in terms of electrifying our product portfolio – and yet another milestone in the history of innovation at the Mannheim plant. We have decided to take care of the assembly of the future battery generation ourselves and thus keep important added value in-house. In and for Europe, we will do this at the Mercedes-Benz plant in Mannheim and thereby further strengthen the future of the location.”
The Mercedes-Benz BTC in detail
The existing building with the number 18, which dates back to 1952, is located at the heart of the plant and covers an area of 7,500 square meters. In recent months, it has been extensively renovated and extended by a 3,000 square meter annex.
Over 60 new machines and systems are being installed in the BTC, where the relevant processes for the prototypical production of battery cells and systems can be mapped: coating technologies, welding processes, assembly and adhesive processes.
The BTC is divided into two areas. In the cell area, product and process knowledge regarding the manufacturing of battery cells is gained. The equipment provides the prerequisites for gaining extensive knowledge of cell chemistry. For example, it offers the opportunity to experiment with different recipes in the production of battery paste, also known as “slurry”.
This slurry is then used to produce prototype battery cells, the smallest unit of a battery. Each cell passes through both clean and dry room areas, as it is very important to protect the sensitive materials from dust particles and humidity during production. Both pouch and prismatic cells, two different types of battery cell, can be produced in the cell area. The cell area is used to build up expertise in the manufacturing process and unit scaling.
Experience in battery pack assembly is gained on the pilot line for battery pack production: battery modules, the next larger unit within a battery, are manufactured from cells before battery packs are subsequently produced from these modules. In a few years’ time, the findings from this line should go into series production at the Mannheim site.
A total of around 100 employees work at the BTC. In order to give employees more space for creativity, productivity and efficiency, a modern office concept with different work zones was chosen.