Focus on the new e-axle. Our interview with Jan Hjelmgren (Volvo Trucks)
At the beginning of 2024, Volvo introduced the Aero range. Right before the last IAA in Hannover, the Swedish manufacturer announced big changes in electric truck development, with the new e-axle coming next year, revolutionizing powertrains and enabling higher efficiency range. We talked about all this with Jan Hjelmgren, SVP Product Management and Quality at Volvo Trucks.
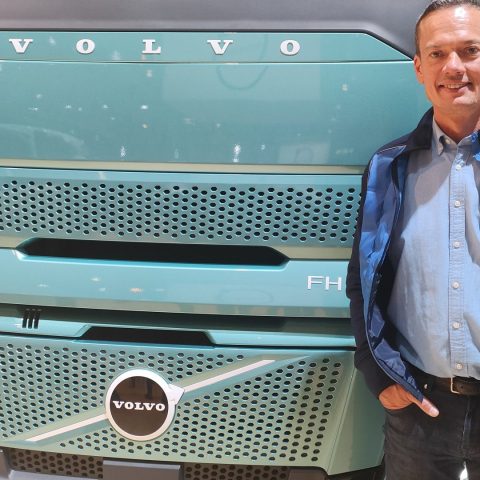
At the beginning of 2024, Volvo introduced the Aero range, and right before the last IAA in Hannover the Swedish manufacturer announced big changes in electric truck development, with the new e-axle coming next year, revolutionizing powertrains and enabling higher efficiency range. In the background lay crucial partnerships in view of hydrogen-powered trucks. We talked about all this with Jan Hjelmgren, SVP Product Management and Quality at Volvo Trucks.
How’s the Volvo Trucks proposition changing?
It’s a lot about the new Aero introduction, at the beginning of this year. It’s also important to say that our strategy focuses on both ICE and electric vehicles. In particular, the FH Aero manages to improve efficiency by 5% or even more, according to some customers who are indeed using the trucks.
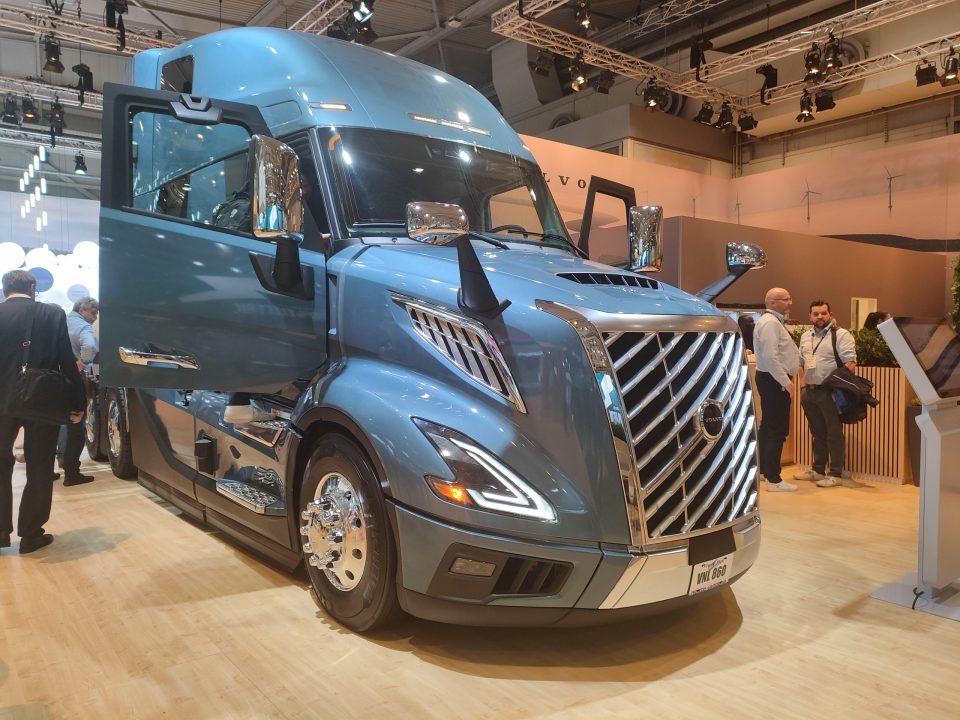
We’re also updating the iconic FH16. The reason is that our customers want it and need it for heavy-duty transport, of course. It is a product of the future, as well. We also took the opportunity, at the last IAA, to bring in an American product, such as the all-new VNL truck introduced earlier this year. With this new version, we’re improving fuel economy by 10%.
Of course, battery-electric trucks are key in our proposition. We’re starting the sales of the long-range FH Electric next year, with a range of about 600 km.
Jan Hjelmgren (Volvo): here’s how the e-axle was developed
The introduction of the e-axle for the new generation of Volvo e-trucks is a true enabler to have more performing vehicles. How’s the Volvo e-axle made?
Our in-house developed e-axle is a fundamental piece in our long-range products. About the e-axle development history, I have a lot of things to say, as I was the Head of Powertrain development at that time. It all started with a few people having an idea, and I’m talking about our team in Lyon. We decided to develop the product ourselves because we thought we could make it better than others.
Since we have a lot of industrial capacity in the Volvo group, we decided to go on. We learned a lot along the way and now we can proudly say we can launch the product next year. The e-axle that is coming to the market is only the first type of the e-axle family we’re developing, as we’re using a modular strategy to expand to different types of vehicles. So, different power levels, different installations. The e-axle could be a product for the European market, or even for the North American market.
Is the e-axle the key to have electric trucks with longer range? Is it the key to make e-trucks suitable for covering long-haul applications?
Yes, it’s one of the key ingredients. What the e-axle does is improve efficiency, ensuring less losses in the driveline, which is a very good thing. We will get more space for batteries, which is also good. Another key aspect, of course, is having good battery technology in order to have high-performance electric trucks. It’s a combination of these issues.
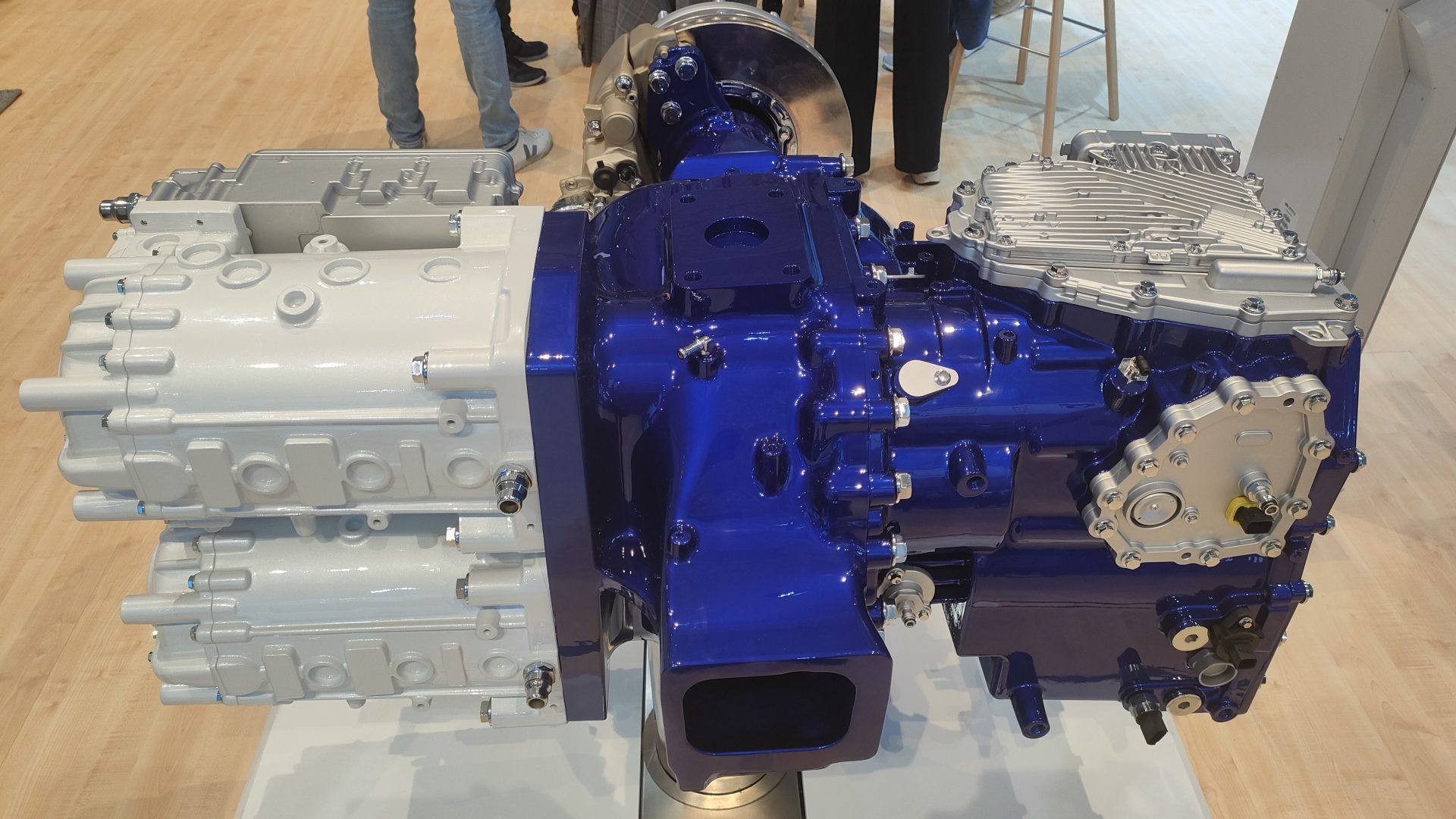
Is it true that electrical axles can make the truck heavier? How did you cope with such thing?
E-axles are less heavy than the components they replace. The current technology allows us to have lighter products.
The battery production process
How’s Volvo working in the development of its batteries? Are you considering the possibility of developing them in-house, from the cells to the final assembly?
We are on a journey. When we started to sell e-trucks in 2019 we bought the complete battery packs from suppliers. Now we are building modules in our assembly sites. It’s possible that in the future we may start from the cells. When we get higher volumes, the possibility to manage the whole cycle will be more and more important for us. It is a consequence of the volumes.
Why is it so important to manage the battery production process in-house?
There are basically two ways. Relying on a partner and working with them, or building the whole production chain in-house. Let’s take the conventional engine as an example. If we consider these components as technologically crucial it’s worth investing a lot of money in their production. It’s not the same for other products, which can be considered as commodities. It’s a very strategic reasoning you must do, always thinking of what’s best for the customer’s experience.
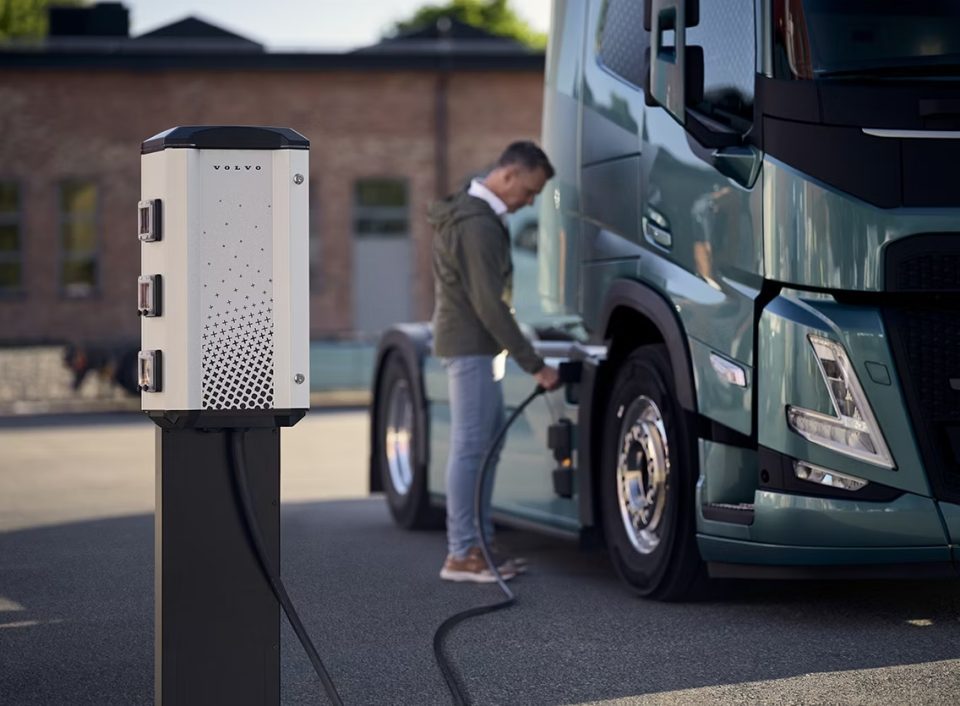
As the leading European brand in terms of e-truck sales, how do you consider the current slowdown in electric vehicles growth figures? Is the market rejecting such technology (not only in the truck sector) or do we need to wait longer to see higher figures?
I think the current scenario is of course a bit worrying. From the customer’s perspective, you need to have a product that does the work. You need to have a suitable infrastructure to charge the vehicles, and, in some regions, you also need to have some subsidies to make the shift even more attractive. Our electric trucks on the road are showing the products are there and can do the work. I think it’s a matter of infrastructure availability, and a matter of cost of the vehicles. In such a big transformation, even a political push could be important to boost e-truck sales, at least in Europe.
“Society needs hydrogen to meet decarbonization targets”
Does Volvo believe in hydrogen ICE?
We don’t believe there’s a single solution in decarbonizing transportation. Hydrogen will be an option. Maybe not everywhere, but society needs hydrogen to meet decarbonization targets. We are in a joint venture with Daimler, called cellcentric, to develop fuel cells. We have a new joint venture called Cespira with Westport Fuel Systems, with the aim of reaching a wider adoption of the patented HPDI technology used today in gas vehicles. This is a first step to make the technology ready for hydrogen-powered vehicles.
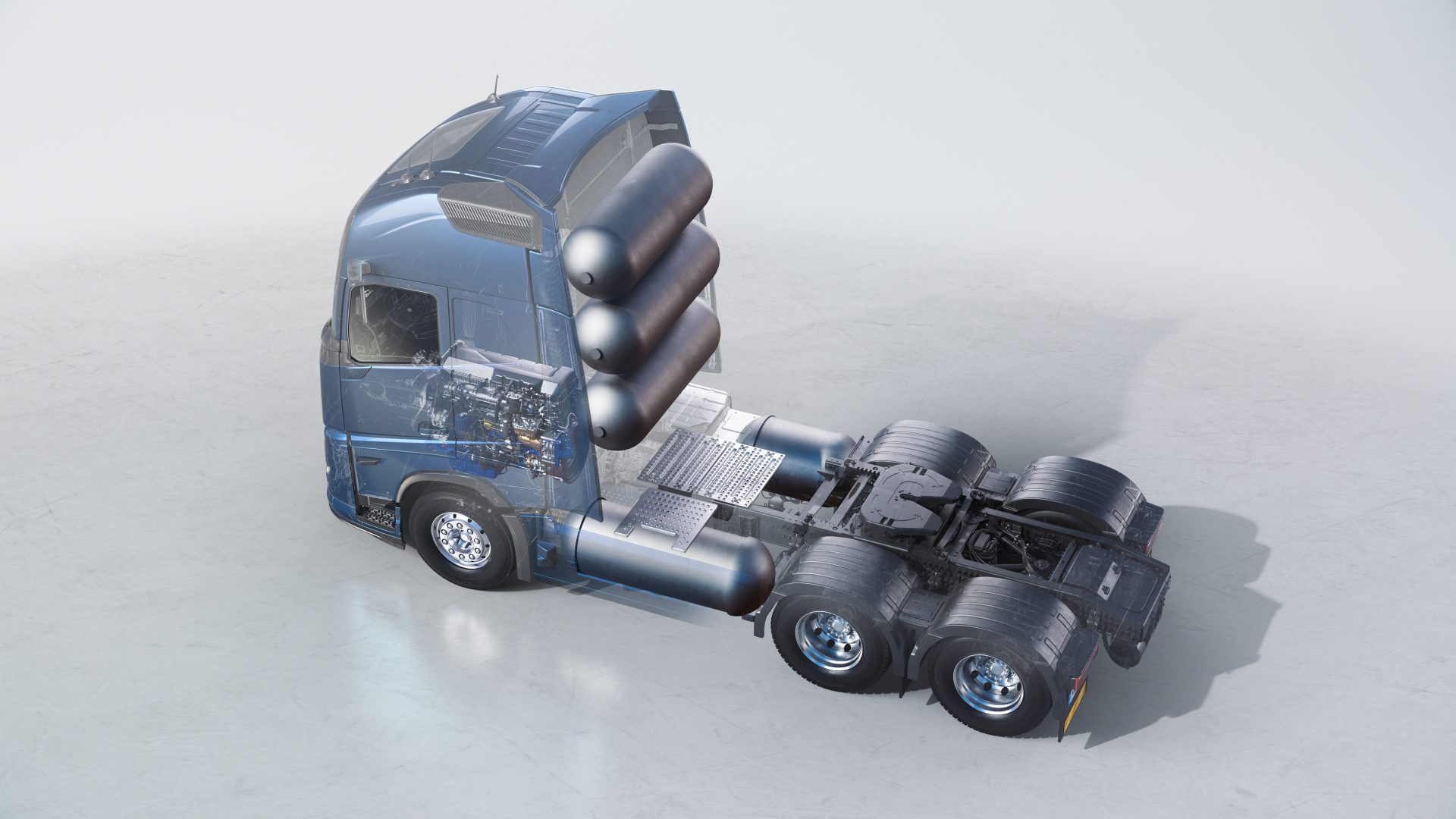
One of Volvo’s latest communications was about the increased use of fossil-free steel in truck production. What are your targets in this regard? Is the process somehow certified?
The overall target is to make sure that the complete truck is carbon neutral by 2040 not only when it’s used, but also when it’s produced. Up to 2040, we need new materials, and one of these is low-emission steel. We’re very happy we can now take this big step, which is only one of the many big and small steps in view of more environmentally friendly solutions.