FPT Industrial: let’s go, XC13
The XC13 surely sounds agnostic in FPT Industrial’s unofficial nomenclature; it comes, indeed, with a tripartite certification: Euro 6E (winking an eye at the upcoming Euro 7), methane gas and also biofuel, with a link to hydrogen. Andrea Abbà, FPT’s product marketing manager, told us about dialoguing with Iveco upon conceiving the XC13 for the Model Year 2024. Read the full article in the March issue of Powertrain International.
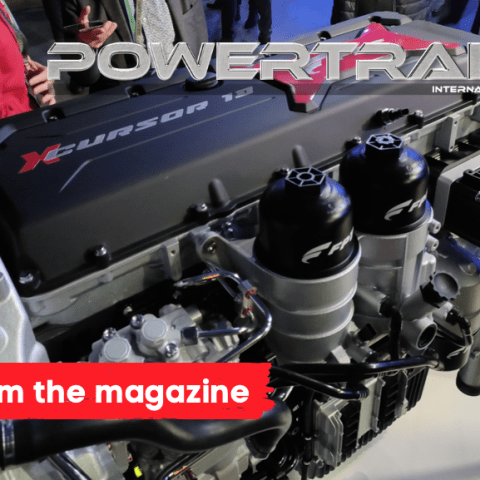
The XC13 is the quintessential expression of FPT Industrial ’s soul: common rail and thermodynamic parameters that are Diesel cycle-optimized, with the HVO option; a significant upgrade of the natural gas unit, historically rooted back to Turin; a hydrogen version that looks forward to the (not-so-distant) future. It turns its gaze to the on-road with this version, that is, however, naturally inclined towards mobile industrial applications.
After all – as Andrea Abbà will tell us – field tests are being carried out on a Prinoth snow groomer, right in a hydrogen incarnation. Introduced in Barcelona, where Iveco said it would be investing a billion into renewing their entire range, the XC13 reaffirms internal combustion engines’ prominence in the heavy range. At the headquarters in Turin they firmly believe BEVs are not an option for long-haulage.
Speaking of which Luca Sra, heading Iveco Group’s Truck Business unit – was absolutely unequivocal. “Let’s think of a carrier working on international routes: it simply can’t work without the fuel autonomy it needs to ensure its business stays productive. It comes just naturally, then, to think that we need time, we need the transition to be guided. Ours is neither a critical nor an opportunistic stance, but rather the affirmation of a strong sense of practicality.”
Andrea Abbà, FPT’s product marketing manager, told us about dialoguing with Iveco upon conceiving the XC13 for the Model Year 2024.
Could you tell us about Iveco’s demands? In other words, about the genesis of the XC13?
“Reducing fuel consumption was our North Star. To stick to this input, we revolutionized the engine starting from the very engine block, whose material changed from cast iron to compacted graphite iron. Displacement per cylinder was our cornerstone, given that bore and stroke had remained unchanged, compared to the Cursor 13. We also implemented a new valve actuation system to maximize braking power, which allows vehicle engineers to avoid fitting a retarder on many applications. That’s an expedient that enables end customers to get a pretty considerable saving. This project enabled us to shed over 100 kg. I know we’re talking about a 44-ton truck, but this means the carrier will have a 100kg of extra payload. We resized the crankshaft and used connecting rod journals and crankpin journals of a smaller diameter; plus, we added an electronically controlled dual flow ball bearing turbo, which optimizes air flow and thus also fuel consumption. We modified the common rail: pressure gets from 2,200 to 2,500 bar. We also made variations to the Peak Cylinder Pressure, raising it to 250 bar. We were asked to provide a base engine that could work with a variety of fuels – diesel, natural gas, bio, and also hydrogen, in the future.
Another key demand was about fuel consumption, that has a direct impact on CO2 emissions. We have to comply with the goals set for 2025 for truck drivers. XC13 will be one of the primary contributors to the Iveco Group mission. The engine consumes 7% less diesel compared to Model Year 2022 and as much as 9% less compared to the Model Year 2019, which is the baseline against which the impact set for 2025 is measured. The natural gas/biomethane version uses 8% less fuel compared to Model Year 2022 and 10% less compared to MY 2019. We were clearly asked to align with competitors’ performance. So in particular, we worked to close the torque gap at low revs, so hard we can now say we’re the best in class, both in terms of max torque and of downspeed, hence at low revs.”
Could you expand a little on performance, ending with a note on MEP?
“In terms of performance, we equalled the top of the range. The max engine capability is 600 hp/2850 Nm, but to date we have certified the 580 hp/2800 Nm version. If we compare the 500 hp XC13 with the 480 C11 and the 490 C13, thanks to downspeeding, in addition to achieving a remarkable increase in max torque up to 2600 Nm (versus 2300-2400) max torque is reached already at 840 rpm, versus the 930/970 rpm of the previous versions. The mean effective pressure gives us an idea of the amount of useful work achieved with the same displacement. The MEP went from 24.4 to 27.8 bar, meaning a 14% increase.”
114 kg lighter than the Cursor 13. Is this only explained with the use of compacted graphite iron?
“That’s certainly one of the key improvements, as we changed the engine’s core – that is, the cylinder head and the block. In addition, we downsized a few components, namely the crankshaft, the conrods and the piston, to reduce both size and friction. We halved the number of counterweights – we went from 8 to 4. That laid the groundwork for the 114-kilogram weight reduction.”
When discussing with Iveco, what inputs were you given as to performance, considering that internal combustion engines are steadily under the spotlight? Specific curve increase or fuel reduction?
“No doubt reducing consumption. To achieve which, downspeeding is a key step. And this brings us back to what we were able to reap: 300Nm more and 150 rpm less, as I mentioned earlier.”
Will these same parameters be applicable to the hydrogen version, too?
“Hydrogen is less efficient, after all is the Otto cycle we’re talking about, so we can draw a comparison with natural gas technology. We have to think of efficiency and performance similar to those in the gas and biomethane versions. The NG version’s max capability is 500 hp at 2200 Nm. Torque and power curves meet the needs of this segment’s core – long-haul applications. As you know, we launched a prototype jointly with Prinoth, fitted on a snow groomer, tested last winter. We’re setting ourselves the target of achieving start-up production of the hydrogen-fuelled XC13 by the end of the decade. This is not a very short-term project, but we do have a few engines being field-tested so that’s a realistic option. We have changed all components on the NG version, too, in addition to introducing the new valve actuation system to maximize braking power, the same applied to diesel, with the differences in performance that are inherent to the individual technologies. The main changes, compared to the diesel version, are the turbocharger, an electronically controlled wastegate – no longer a VGT – and the addition of EGR. Recirculation suits more powerful engines in that it enhances performance: natural gas entails temperatures that are much higher than with diesel engines, which the EGR can lower, thus improving efficiency.”
Are the axles by FPT, too?
“In Turin we’ve been producing axles and transmissions since the Seventies, we manufacture about 260,000 a year for commercial medium and heavy vehicles. To the MY24 we provide the front and rear axles. On the rear axle, the rear axle ratio was sped up to 2:06 to optimize downspeeding.”
What about friction reduction?
“It helps mitigating CO2 emissions as well as fuel consumption. To achieve it, we used smart auxiliaries, such as variable water and oil pumps, and also donwnsized the components.”
One of the take-home messages from Barcelona is that Iveco was brave enough to state that for the time being electric vehicles are no solution for long haulage. How did you come to this conclusion?
“Being very practical. Currently, legal requirements are clear, and so are thresholds, and the penalties applied in case the goals are not met. Everything else is still a chapter left unfinished: for example, where’s the fuelling infrastructure for hydrogen, a carrier that holds promise for long haul transportation? And what’s the rationale, considering that the circulating fleet in Italy is more than 10 years old?”
Vehicle registration data for 2023 have just been issued and the percentage share of diesel vehicles is growing. FPT Industrial too expects ICEs to remain the benchmark for a long time.
Click here to read the full article or download the pdf.