Bauma 2025, alternative drives to decarbonize the construction site
Environmentally friendly drives: as the leading international trade fair for construction machinery, building material and mining machines, Bauma has been following this trend since its beginnings.
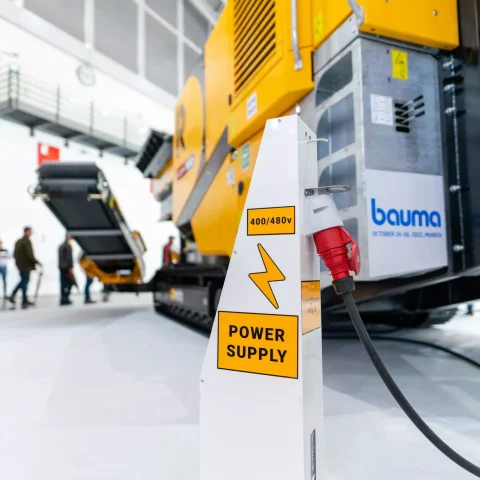
Bauma 2025 is getting closer: the next edition will take place in Munich from April 7 to 13, 2025. Construction machinery worldwide emits several hundred million tons of carbon dioxide every year, while more and more countries, municipalities and companies are aiming for a climate-neutral future. In light of this, the industry is increasingly switching from traditional diesel engines to more environmentally friendly drives. As the leading international trade fair for construction machinery, building material and mining machines, as well as construction vehicles and equipment, Bauma has been following this trend since its beginnings. Alternative drives will also be one of the main topics at the next edition from April 7 to 13, 2025.
Numerous manufacturers and users of construction machinery have already committed to decarbonization. The Volvo Group, for example, announced that from 2040 it will only supply vehicles that are powered entirely without fossil fuels. In the same year, Strabag SE, one of Europe’s largest construction companies, aims to achieve climate neutrality along its entire value chain, which of course includes the operation of its construction machinery.
Electric motors can now be classified as a permanent fixture as a climate-friendly drive for construction vehicles and machines. Whether it was excavators, wheel loaders, rollers, dumpers, or vibratory plates, many exhibitors already presented new solutions from their ever-growing e-portfolio at the last editions of Bauma. And this trend looks set to continue: According to a forecast by the analysis and consulting firm IDTechEx, the global market for electric construction machinery will be worth 105 billion dollars by 2042.
“Battery electric systems are still primarily suitable for compact machines. Their daily energy and power requirements can be covered by an electric motor and a moderately sized lithium-ion battery in conjunction with a well-defined charging strategy,” says Timo Feuerbach, technical expert for construction machinery and building material machines at the German Mechanical Engineering Industry Association (VDMA). The Bobcat RogueX2 concept loader belongs in this category as a current and pioneering example. The all-electric machine not only operates with zero local emissions, but is also fully autonomous, according to the manufacturer’s specifications. This year, it received the prestigious Red Dot Design Award in the “Design Concept” category.
“For larger and heavier construction machinery, however, electric drives currently often still reach their technological and, due to the additional costs for electrification, also economic limits,” says Feuerbach. Added to that are challenges relating to the power supply and the charging infrastructure. For example, the available grid capacity may not be sufficient for the high energy requirements of the e-machines, especially at construction sites in rural or remote areas. Long charging phases in turn limit the operating times. “The industry is currently looking for practicable and affordable solutions to this, for example, by using mobile charging units and fast charging stations, or implementing intelligent energy management systems,” as the VDMA expert explains.
It is clear that openness to technology is required for drives that are as climate-neutral as possible across the entire spectrum of the construction industry. For example, a life cycle analysis commissioned by the Liebherr Group came to the conclusion that operating mobile cranes with hydrogenated vegetable oil (HVO) promises the greatest potential for reducing greenhouse gases. Other fuel alternatives that can contribute to decarbonizing construction sites are biodiesel, biogas and e-fuels.
Companies and research institutes are also focusing on developing and testing hydrogen powered construction machinery. The Liebherr Components product segment presented prototypes of two hydrogen combustion engines at Bauma 2022, and series production was announced for 2025. The industry is also exploring potential applications for fuel cells. For example, General Motors and the construction machinery manufacturer Komatsu are working together on a hydrogen fuel cell module for an electric dump truck. Komatsu has also developed a medium-sized hydraulic excavator with a hydrogen fuel cell system as a concept machine.
“Before alternative fuels can be used on a large scale, however, issues regarding their production and distribution need to be clarified,” emphasizes Timo Feuerbach. According to him, to really benefit the environment, vegetable oils should, for example, ideally only be produced from plant and food waste, and be widely available. He says that the situation is similar for hydrogen or e-fuels, adding that, alongside producing sufficient quantities from carbon-neutral sources, another prerequisite is also setting up an extensive distribution network.