Parker and the electric spirit at bauma
Two fractions of Parker's electric soul at bauma are GVM motors and GVI Gen 2 inverters
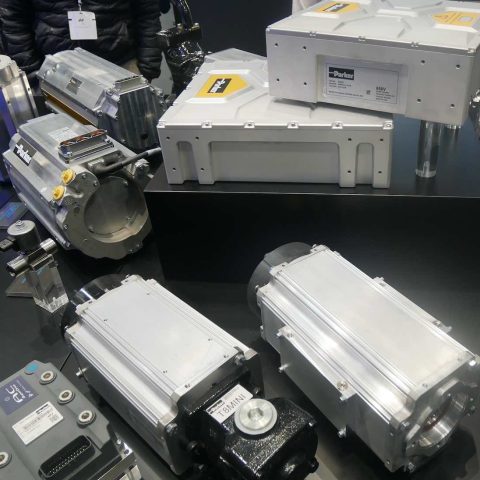
We wrote about Parker Hannifin’s participation at bauma in reference to hydrogen. Here we tell you about the electrical part. In fact, to be perfectly comprehensive, let’s switch to electrification and digitalization, that are strictly interconnected.
Parker ‘s electric soul rhymes with GVM
Among Parker ’s most recent electric developments is the launch of the Global Vehicle Motor (GVM), designed in combination with a gearbox. One of the key differentiators of this motor is its integrated thermal management system, which is essential in electric drivetrains operating under demanding duty cycles. Efficient cooling enables the motor to withstand peak torque loads without compromising performance or reliability. When combined with an electric PTO (ePTO), the solution enables full removal of the combustion engine while maintaining the ability to drive hydraulic systems. The complete package includes an inverter, drive, and electric motor, which can be tailored to match the required pump configuration. Electrification also enables greater versatility in pump design. A concrete example is the new T8MINI pump, an evolution of the T7 series based on Parker’s proven Denison vane technology. Engineered for electric powertrains, the T8MINI delivers low noise, high efficiency, and a compact footprint, making it particularly well-suited to space-constrained applications. The silent vane pump technology ensures quiet operation even at high speeds, reducing environmental noise—especially in urban applications—and improving operator wellbeing. Thanks to its small displacement range, the T8MINI requires only modest torque, allowing for the use of downsized electric motors and further improving packaging efficiency. Digitalization further amplifies these benefits. Parker has invested in model-based software development, simulation tools, and digital twins, all aimed at reducing time-to-market. Customers can leverage configurable simulation models to accelerate prototyping, optimize their system architecture, and evaluate multiple scenarios without the need for physical testing.
And with GVI
The new second-generation Global Vehicle Inverter (GVI) GEN 2 delivers enhanced motor control for both traction and auxiliary functions, improved safety features and greater design flexibility needed across multiple industries, including construction, mining, material handling, agriculture, and transportation. Parker offers the GVI GEN 2 in two power configurations, 75kW and 250kW, with a 125kW coming soon. The GVI GEN 2 is tuned to provide a perfect match for the Parker Global Vehicle Motor (GVM) range of permanent magnet AC (PMAC) motors to deliver high power density and energy efficiency. The features include Safe Torque Off (STO), High Voltage Interlock Loop (HVIL), active and passive discharge, and high-speed overvoltage protection. To maximize energy efficiency and longevity, the GVI GEN 2 incorporates advanced liquid cooling to reduce thermal stress for optimum performance under harsh operating conditions. The inverter series has a wide operating voltage, from 200 to 750 VDC, further enhancing its versatility, allowing OEMs to adapt to various vehicle platforms with ease. Additionally, its rugged design and IP67/IP6K9K rating ensure reliable operation in extreme environments.
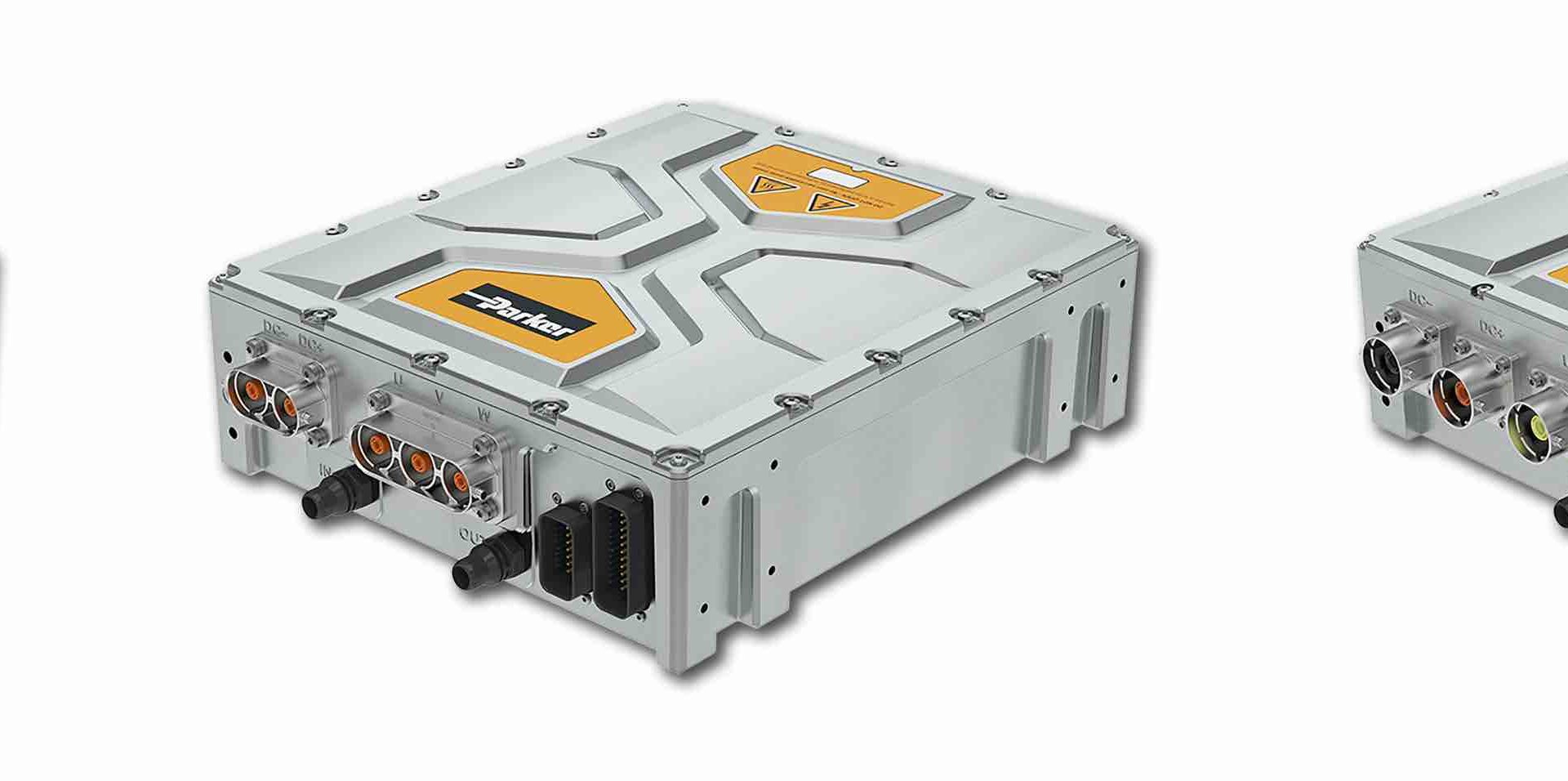