Bosch: new injection technology for hydrogen engines
At Agritechnica 2023, Bosch premiered a technical innovation: an injector for direct hydrogen injection that requires no additional lubrication.
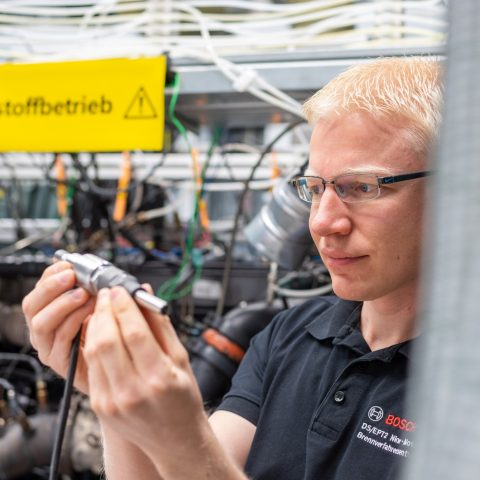
As different as the tasks of agricultural machinery are, all these vehicles have one thing in common: a diesel engine. Yet its use in the agricultural sector alone accounts for some 5 percent of Germany’s diesel consumption. Clearly, agricultural machinery needs to become more climate friendly. Bosch sees hydrogen, which can also be used to power heavy vehicles, as essential for achieving climate neutrality. With its solutions for the hydrogen engine, which can also serve as a suitable drive for specific applications in agriculture, the company wants to move further toward the establishment of a hydrogen economy. At Agritechnica 2023, it presented for the first time a technical innovation: an injector for direct hydrogen injection that requires no additional lubrication.
“Technologically, the new hydrogen injector for direct injection is a great leap forward,” says Jan-Oliver Röhrl, the executive vice president responsible for commercial vehicle powertrains in the Bosch Powertrain Solutions division.
In the course of a vehicle’s service life, the injector opens and closes roughly one billion times. To ensure that this always works reliably, the engineers developing the hydrogen engine had to overcome two challenges: one, the lubrication provided by the fuel in the diesel engine is absent; and two, the hydrogen may react with materials it comes into contact with. The engineers’ solution is a sophisticated design that keeps the media separate inside the injector, and uses various coating technologies. The systems for low-pressure direct and port injection have been developed for engines that can also be operated with heavy loads and in difficult environmental conditions. As a systems supplier, Bosch also offers electronic control units, products for storing and supplying hydrogen, and other powertrain components.
Besides fuel-cell applications and battery-electric powertrains, the hydrogen engine is another option in the powertrain mix of the future. Its concept is based on established diesel and natural-gas engines. This means that the fundamental structure of the engine, as well as the fuel, air-supply, and exhaust systems, can be transferred from existing powertrain solutions, along with a large number of other familiar system components. “More than 90 percent of the development and manufacturing technologies needed for the hydrogen engine already exist,” Röhrl says. “This allows us to maintain large parts of our value chain – and applies to the aftermarket as well.” In addition, the hydrogen engine consists primarily of steel and aluminum, which reduces dependencies on critical raw materials and their supply chains.
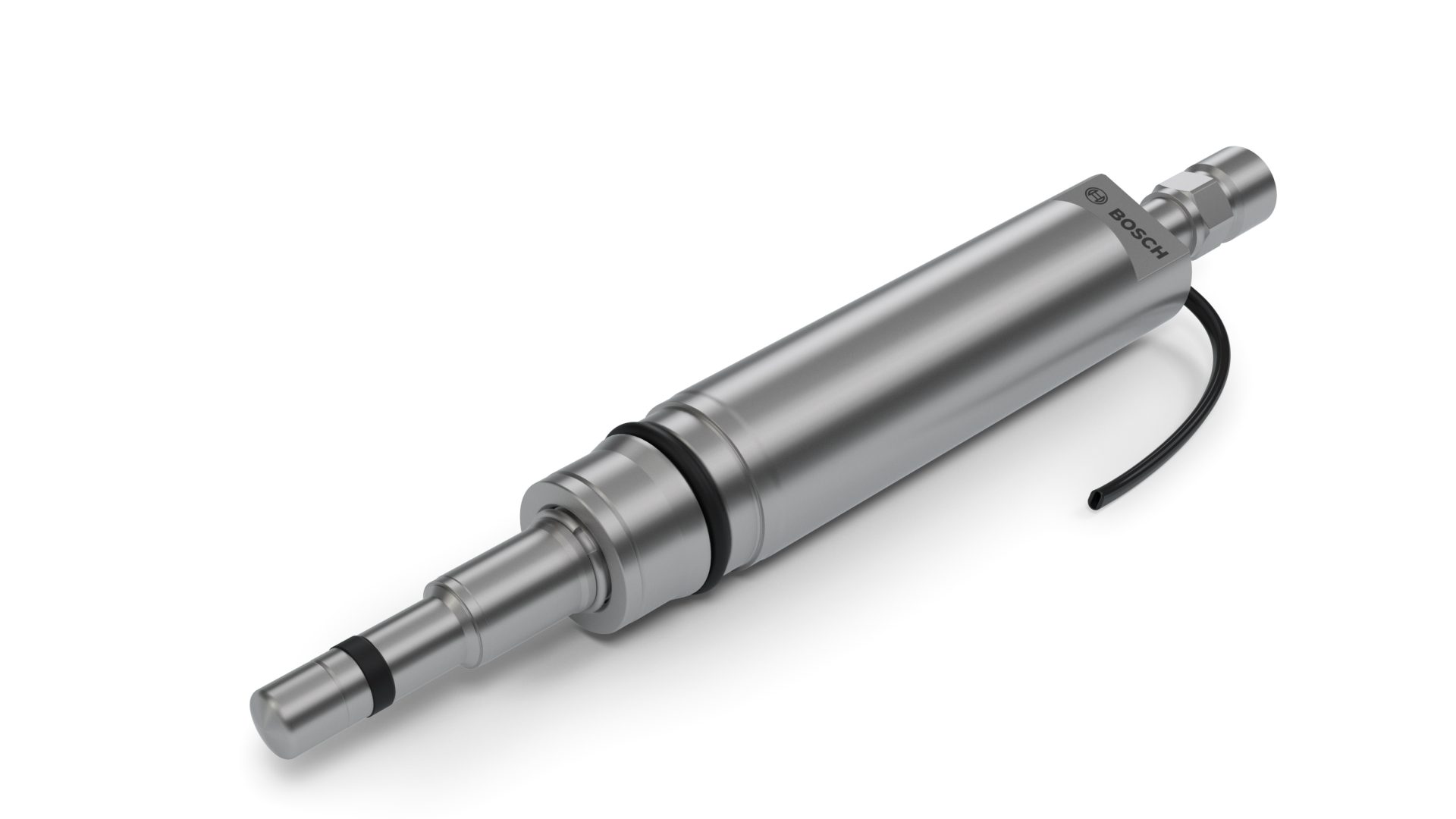
Making conventional systems fit for the future
At the same time, Bosch is continuing to improve its conventional diesel-injection and exhaust-gas treatment systems for commercial vehicles and the off-highway sector. “We want our solutions to help automakers worldwide further reduce CO2 and other emissions,” Röhrl says. For example, the modular CRSN common-rail system for commercial vehicles and off-highway applications exhibited at Agritechnica 2023 ensures efficient fuel supply and injection in diesel engines. It is scalable for pressure levels between 1,800 bar and 2,500 bar, and can be configured for engine sizes of up to eight cylinders. In addition, Bosch diesel technology can already run on renewable synthetic fuels. Such fuels can complement electromobility or hydrogen-based powertrains where these solutions face economic or physical challenges.
Read also this: Bosch Rexroth at Agritechnica 2023