Cat and its futuristic solutions. Grade with 3D and Remote Services
Grade with 3D for D3K2, D4K2 and D5K2 The new Cat Grade with 3D system for D3K2, D4K2 and D5K2 track-type tractors is an automated grade control system that uses GNSS (Global Navigation Satellite System) technology to give a nice precise touch to the position of the machine’s blade, without operator input, from first rough cut […]
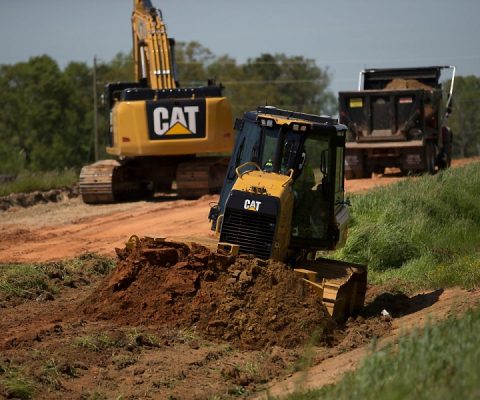
Grade with 3D for D3K2, D4K2 and D5K2
The new Cat Grade with 3D system for D3K2, D4K2 and D5K2 track-type tractors is an automated grade control system that uses GNSS (Global Navigation Satellite System) technology to give a nice precise touch to the position of the machine’s blade, without operator input, from first rough cut to finish grade.
But there is more. Grade with 3D incorporates the Cat AccuGrade Ready Option, which allows use of universal-total-station and laser references for automated control. The new system is there to allow the achievemnt of specified grades faster and more accurately, compared with conventional methods.
Cat Grade with 3D is an optional system, the idea behind it is to fit the design of the machine ‘like a glove’. The GNSS antennas are securely mounted on top of the cab. GNSS receivers and a data radio are also neatly housed in the roof structure. Three inertial measurement units monitor machine orientation. In the meanwhile, position-sensing hydraulic cylinders monitor blade position. The integrated installation eliminates the need to remove components at the end of the day. The system can automatically position the blade via an integrated, electro-hydraulic valve module.
Grade with 3D automatically controls the movement of the machine’s blade, both lift and tilt, to conform to digital jobsite plans. The only input required of the operator is to steer the machine. The new system is also able to work with other Caterpillar dozing features, such as AutoCarry, which focuses on assisting the operator in attaining optimum blade loads in varying ground conditions, while reducing track slip.
CATERPILLAR AND THE ULTRA-CLASS TRUCKS: 796 and 798 AC
There is also a less expensive ‘initial package’
As an alternative to the factory-installed Grade with 3D system, machines can be ordered with only the AccuGrade Ready Option (which includes the Cat Slope Assist system, sensors, processor, and wiring harnesses). The Cat dealer can then scale up this technology by installing the required Grade with 3D components, including antennas, receivers, data radio, display, and Software Enabled Attachment key. This approach allows, of course, the possibility to start with a more ‘budget solution’ and then upgrade from there as needed.
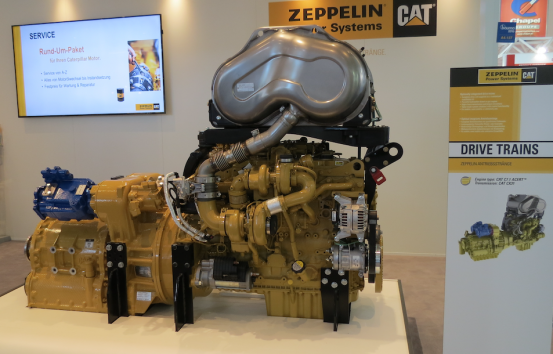
Let’s talk about the remote services for diagnostics
Caterpillar introduced a new suite of Cat Connect technology that offers remote equipment diagnostics and software updates to reduce machine and engine downtime. New Cat Remote Services include two offerings: Remote Troubleshoot and Remote Flash.
Herwig Peschl, Caterpillar global marketing manager, on the matter, said: «A machine or engine not at work isn’t making money for the customer, which cuts into the company’s profitability for the job. Remote Services provide a solution to more effectively and efficiently maintain equipment. Customers can continue to use their assets while the dealer reviews and diagnoses a fault code from the office».
Remote Troubleshoot
Remote Troubleshoot analyzes real-time asset data, so the dealer can run diagnostics testing on the connected product and pinpoint potential issues. This eliminates equipment downtime during diagnosis. The machine or engine continues to do its job throughout the process.
Once the cause of the fault code or alarm has been identified, the dealer can possibly resolve the issue remotely. If a repair is necessary, technicians can get to the jobsite already having the correct information, parts, tools and instructions to make the repair.
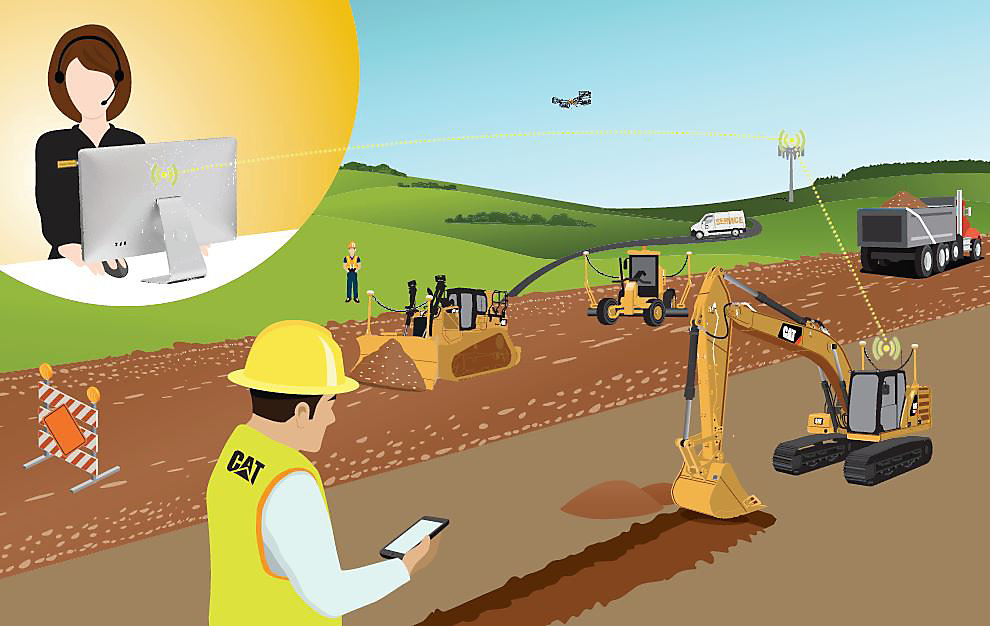
Remote Flash
Remote Flash is there to ensure that the equipment can deliver the right performance. This Cat service enables remote updates to the software of a connected machine or engine, without the need for a service technician to visit the jobsite. With Remote Flash, Cat customers receive notification from their Cat dealer, or directly from Caterpillar, when a new software update is available for a piece of equipment.
Once a customer receives the flash-file push notification for a targeted product, the authorized user simply confirms the machine or engine is ready to begin the flash, initiates the process and confirms the post-flash performance.
Currently, Remote Troubleshoot is available on Next Gen excavators, and Remote Flash is available on Next Gen and 336F XE hydraulic excavators, M3 Series motor graders, L and M Series medium wheel loaders from the 950M to the 972 XE models, and 10 models of Oil and Gas engines. Remote Troubleshoot and Remote Flash work for Cat machines or engines with an on-board PLE641 or PLE742 card and telematics 2017B software or newer. Cat says that more equipment will be eligible for the Remote Services offerings with future updates.
TALKING ABOUT REMOTE MANAGEMENT: CONTINENTAL PRESENTED CONTICONNECT