Liebherr EMS (Electronics Manufacturing Services)
Liebherr-Elektronik has made the EMS service, that already exists for its sister companies, also available to external customers. Here an interview with managing director, Jan Uhlig.
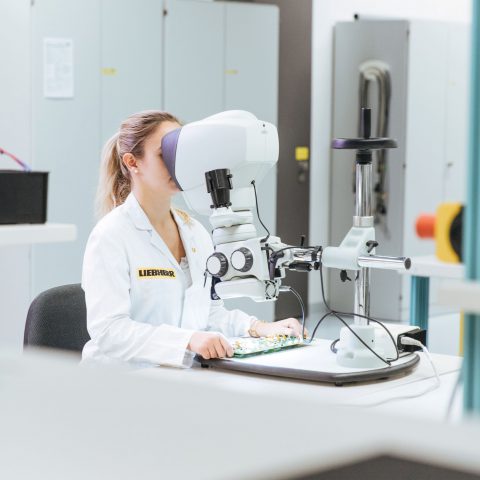
Liebherr EMS (acronym of Electronics Manufacturing Services) responds to a need that has become disruptive: the supervision of on-board electronics. “Learning and growing are constant processes, and this applies to our Electronics Manufacturing Services (EMS)” they say. “Liebherr-Elektronik GmbH has made the EMS service, that already exists for its sister companies, also available to our external customers.” Liebherr released an interview with managing director, Jan Uhlig, from Lindau facility.
Mr Uhlig, what makes, in your view, an efficient Liebherr EMS service provider?
Electronics Manufacturing Services (EMS) encompass the entire contract manufacturing of electronic assemblies, devices and systems up to component assembly, soldering, final assembly, testing and inspection. Today, many customers no longer ask exclusively for contract manufacturing. The need for development and repair services, as well as the demand for logistics and obsolescence management are also part of this. So, a modern, efficient EMS service provider should be able to offer everything from a single source and deliver high product quality on short notice.
In your opinion, what makes Liebherr-Elektronik GmbH particularly attractive in the EMS sector?
Liebherr-Elektronik GmbH is the competence centre for electronics within the Liebherr-Components Division. We have extensive expertise and experience in the design, development, production and series support of electronic products, for example for the medical and agricultural technology sectors. Our certification according to the quality standards of the aviation industry and our focus on quality enable us to manufacture products that meet the highest demands of the aviation industry. We are also listed with the Federal Motor Transport Authority. We fulfil all requirements as a manufacturer of approval-relevant electronic vehicle parts. Last but not least, we manufacture in accordance with IPC Class 3. At our Lindau site, we work with modern and efficient production lines. It enables us to optimise costs, while maintaining a high degree of diversity and flexibility – from single items to five-digit annual quantities. We manufacture innovatively and supportively in accordance with the customer requirements.
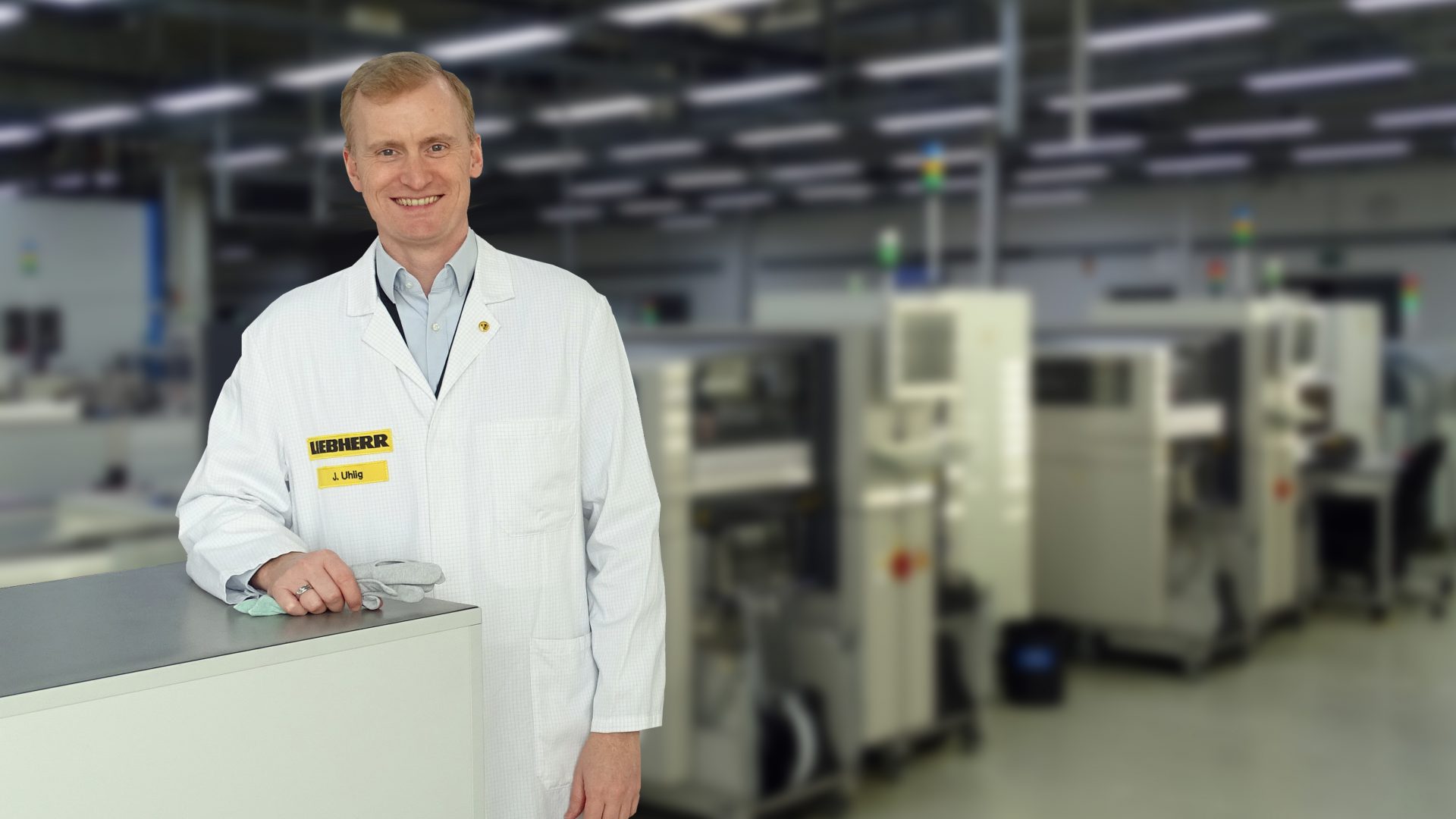
Mr Uhlig, how big is the EMS team at Liebherr-Elektronik GmbH, and what specific services are they responsible for?
The EMS team in Lindau consists of experienced employees from different areas. Since everything starts with product development, highly-qualified development and production engineers reliably support our team. They deal with layout and industrialisation services, for example, or optimise the product based on customer requirements. At the same time, this enables us to minimise product-manufacturing costs.
Furthermore, we also take care of material procurement from international suppliers, including supplier management, auditing and ensuring delivery capability. And that is not all. Obsolescence management is also part of our service. Moreover, we offer long-term storage and stockpiling, complete traceability and customised logistics concepts.
Do you assemble the products in-house?
Yes, in addition to SMD and THT assembly, as well as surface treatment of PCBs, we offer device assembly and end-of-line testing. Well-organised production islands enable highly flexible, fast and qualitatively optimal assembly of the products.
Quality is immensely important. How does Liebherr-Elektronik GmbH ensure a high-quality standard?
We have an integrated quality management system and can also support our customers with the development of complex test concepts. A special feature is certainly our test centre at Lindau with testing and measuring technology at the highest level.
Mr Uhlig, what do you think your customers particularly appreciate about Liebherr?
We are a reliable and competent partner for our customers. Our team has versatile expertise and many years of experience in electronics development and production. This said, we work closely with our customers to find the best possible solutions for their products and diverse requirements.