Poppe + Potthoff supplies a material specially developed for hydrogen applications
Poppe + Potthoff has developed PPH2, a material specially designed for hydrogen applications. PPH2 was designed to be particularly suitable for welding processes (for example, for the production of common rails) and to be easy to process. It can therefore be used in familiar manufacturing processes, such as those used in the production of components for diesel engines.
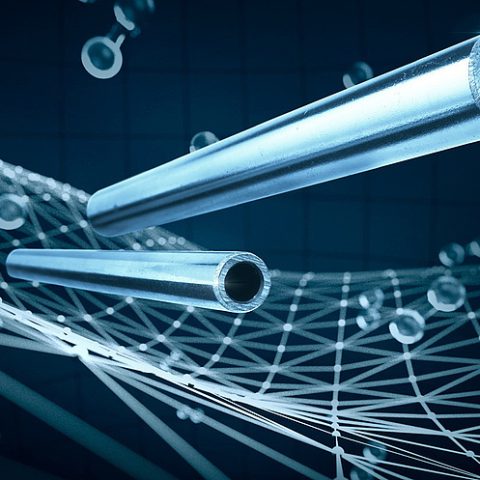
Poppe + Potthoff has developed PPH2, a material specially designed for hydrogen applications. PPH2 was designed to be particularly suitable for welding processes (for example, for the production of common rails) and to be easy to process. It can therefore be used in familiar manufacturing processes, such as those used in the production of components for diesel engines.
Alternative drives have long since ceased to be dreams of the future. Fuel cell and hydrogen technology offers a clean alternative to conventional types of drive – in both mobile and stationary applications. To ensure safe storage and efficient transport of the highly volatile gas within the drive system, the components that are in direct contact with the hydrogen must have special resistance.
In conventional systems, these components have so far been made primarily of austenitic stainless steels. However, this has some disadvantages: austenitic stainless steel is very expensive due to its high nickel content, among other things. Since the material has relatively low strengths, the components must be designed with greater wall thicknesses for higher pressure resistance. This increases the weight and the higher material input in turn leads to higher component costs.
Poppe + Potthoff PPH2, suitable for the production of common rails
To counter these problems, Poppe + Potthoff has developed PPH2, a material specially designed for hydrogen applications. The alloyed carbon steel has high mechanical properties. These are further enhanced by the PPSH annealing treatment developed by Poppe + Potthoff. As a result, components manufactured with PPH2 can be designed with thinner walls than those made of stainless steel, which, in addition to lower weight, also leads to a reduction in material costs and thus represents another clear advantage for customers. Effective protection against corrosion is ensured by a zinc-nickel coating.
PPH2 was designed by Poppe + Potthoff to be particularly suitable for welding processes (for example, for the production of common rails) and to be easy to process. It can therefore be used in familiar manufacturing processes, such as those used in the production of components for diesel engines. In this way, additional costs can be saved, especially since machines and systems do not have to be converted if carbon steel has already been processed before.The material is particularly suitable for the production of components for H2 distribution systems (including pipes, rails and valves) and can be used in both mobile and industrial applications. As a competent development partner, Poppe + Potthoff already manufactures components made of PPH2 in various dimensions – always according to the specific requirements of the customers.