SIKO for the German robot that collects apple crates
Siko's sensors contribute to the AurORa project: a robot dedicated to picking and placing apple boxes
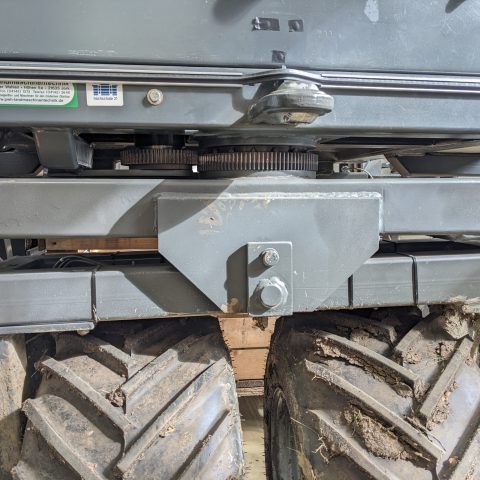
SIKO put in the sensors, the Altes Land, south-west of Hamburg, the orchards, AurOra (‘Autonomer Obstplantagenhelfer Altes Land’, the original German name for the Autonomous Orchard Aid for the Altes Land region) the automation for harvesting apples.
SIKO sensors
Let’s go into the details of the ‘AurOrA’ project. We are talking about a robot (speaking of robots, but for demolition…), i.e. a small, self-propelled vehicle designed to locate and pick up crates full of fruit and bring them to a defined unloading point. For the harvesting personnel, the robot will mean an easing of tasks and the possibility of devoting themselves to more demanding tasks. The initial inspiration for the project came from practical experience: fruit grower Johann Schröder from Jork, in the Altes Land south-west of Hamburg, approached Hochschule 21 in Buxtehude asking for support in the development of an autonomous vehicle. The project started in February 2020 in cooperation with PWH, a company in Jork that manufactures agricultural machinery. The actual aim of the project is to build a working prototype by January 2023 to demonstrate its technical feasibility. The project is financed by the ZIM support programme of the German Ministry of Economic Affairs and is currently in the third planning phase after reaching the second milestone: the robot can already move around the orchard with a high degree of autonomy. Work is now being done on collision avoidance and terrain recognition, such as muddy terrain, to prevent the wheels from spinning and the vehicle from getting stuck or being diverted into a ditch. The third milestone will be the actual picking up and subsequent transport of the crate of fruit. This type of development project always conceals particular challenges, ranging from the coordination of the interests of the various fruit farms, which often have very different harvesting procedures, to infrastructural problems such as a stable mobile phone standard that allows the robot to receive GPS data and communicate with the operator, to the practical difficulties inherent in daily outdoor activities (bad weather, snow, rain, sunlight, terrain characteristics).
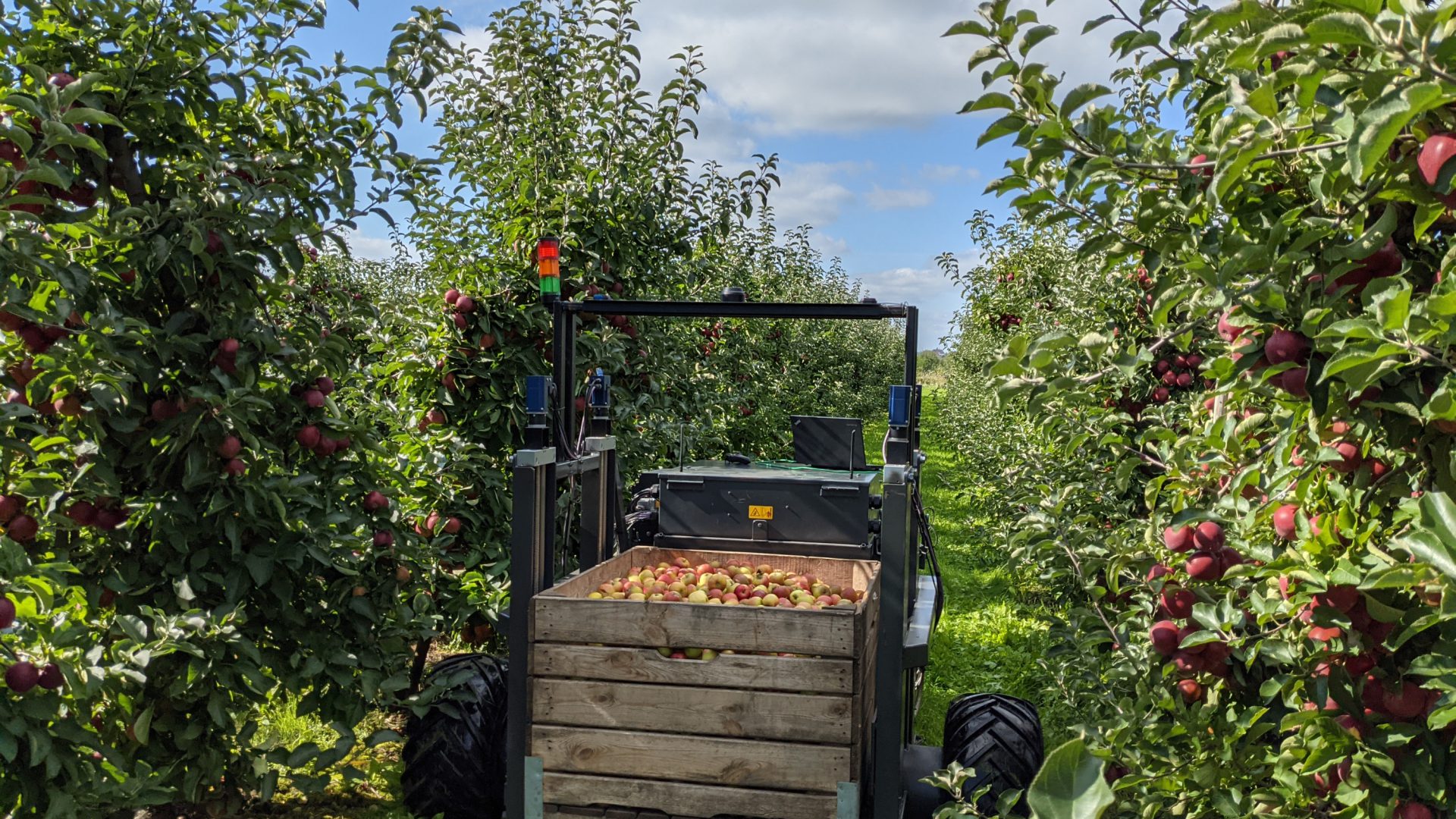
What, how and why
Possible sensors must first of all be very robust and insensitive to harsh outdoor environmental conditions (mud, dust, rain, strong sunlight, uneven terrain). The components of Siko’s Pure.Mobile modular sensor system are particularly suitable for use in mobile machines operating under adverse environmental conditions. A double wheel is installed at the rear of the vehicle, which can turn and thus generates the steering. The steering angle is detected by the WV5800M magnetic encoder and then processed and sent to the control system. The encoder in question is a multi-turn encoder capable of absolutely detecting multiple rotations. Should the voltage be interrupted, e.g. due to low batteries, the previously set steering angle would not be lost. Without an absolute encoder, the steering angle would be incorrectly defined as zero degrees when the vehicle is restarted. The magnetic measuring system meets the requirements for robustness and insensitivity. The project team also appreciated the high precision and reliability of the encoder, thanks to which the vehicle always adjusts the steering angle in such a way that it can travel the defined path without any anomalies and without excessive tolerances. In order to achieve an even higher level of safety when interacting with people working in orchards, and to reliably rule out faults, the safety variant of the WV58MR encoder with redundant position detection will be used in future vehicles. In the development phase, the focus was primarily on technical feasibility and therefore the encoder without safety standard was sufficient. The advantage of the SIKO models: the two encoders have an identical construction and therefore do not require any mechanical changes to the application in the event of replacement. In addition, a CANopen interface was adopted for steering angle detection, allowing as many standardised electronic components as possible to be used, which can be quickly replaced and integrated into the bus system.
Call it flipper
The second SIKO AH25S encoder is a single-turn encoder that controls the position of the crate magazines, the so-called pinballs. The crate full of fruit is lifted by being gripped at four points by four pinballs. When the robot passes over the crate, the crate touches the spring-loaded pinball machines, which swing sideways and then automatically fold back into place under the four corners of the crate to be picked. In order to transport the crates safely, it is necessary to meet the position of the individual pinball machines: have they actually moved backwards, or are they perhaps stuck? Are all four pinball machines underneath the crate to ensure that they can be lifted? The very limited installation space required a miniaturised encoder that could be used directly on site without the need for a special mount. In this case, an analogue encoder is sufficient as the data information is less critical than that of the steering angle sensor. In a development project of this kind, it is necessary for many small gears to fit into each other in order to transform a vague idea into a technically flawless product that can be used in numerous orchards with a balanced cost-benefit ratio in the future. In order to be able to offer farms real added value, the use of ‘AurOra’ for additional tasks such as mulching and mowing or as a support for tree replanting is also being investigated. This would allow its efficient use almost all year round and not limited to the harvest season.
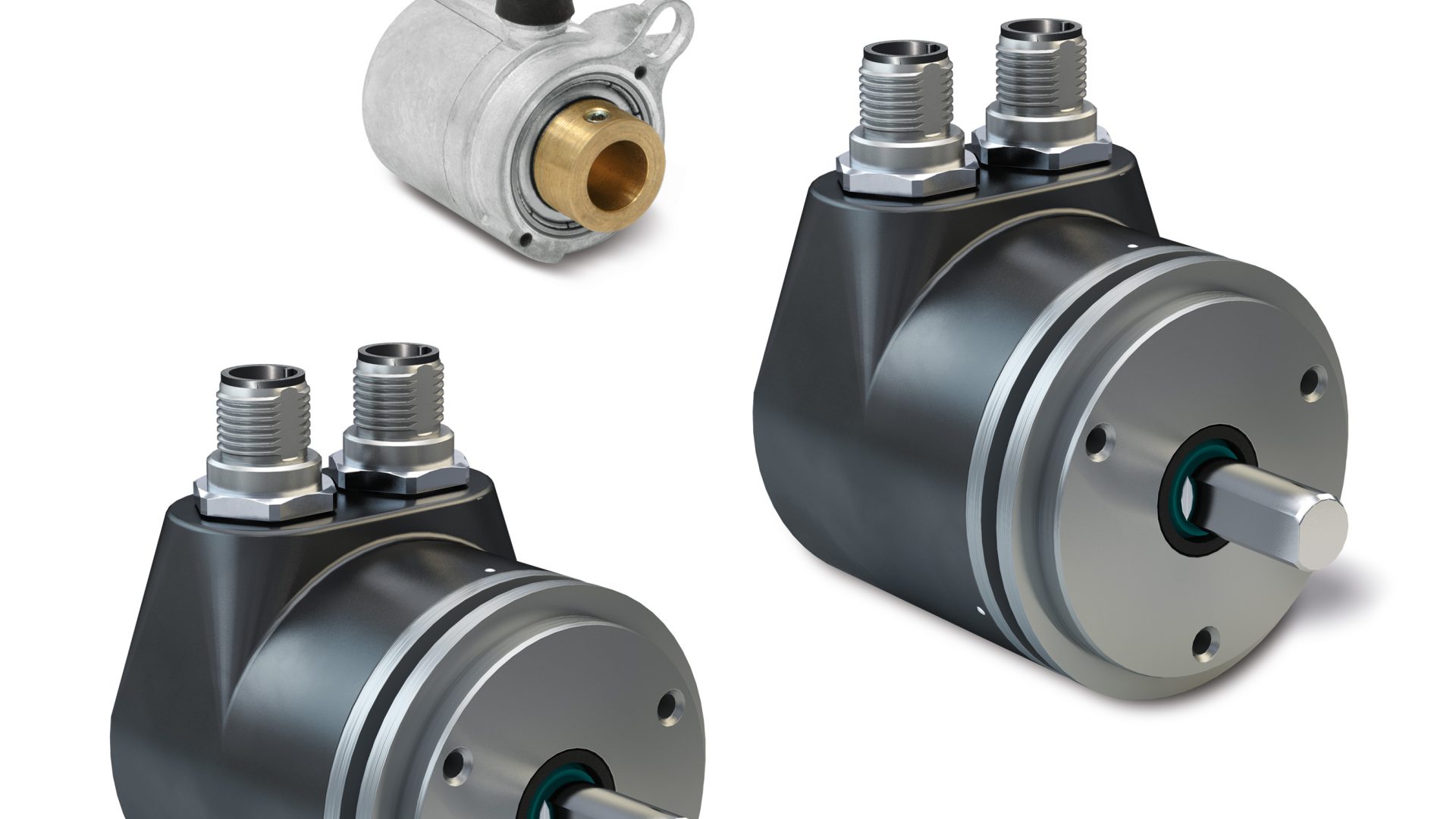