Diesel of the Year 2025: dawn of the Hyundai DX05 & DX08
The Korean star is also reflected in the Diesel of the Year. South Korea is in the empire of industrial powers, cinema in the author anthology, K-pop in the playlist of teenagers. The 2025 edition is about Hyundai Infracore DX, 4- and 6-cylinder modular (BxS 110x132 mm), which have what it takes to stand out. Read the full story in the November issue of Powertrain International.
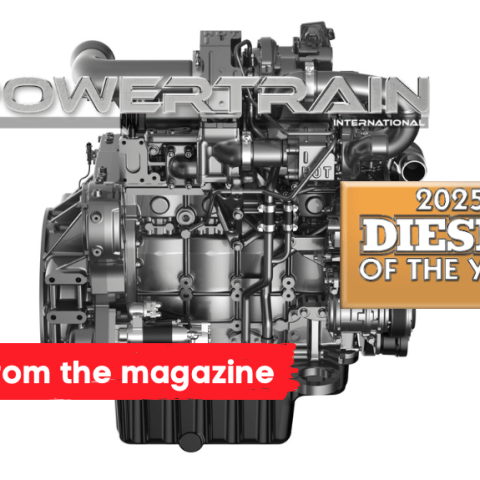
This story is rooted in time, some ten years ago, between the 2008 subprime crisis and the pandemic in 2020, when Doosan Infracore launched the G2 range. A triad of 1.8-, 2.4- and 3.4-litre compact engines initially intended for captive application (such as forklifts, skid steer loaders and mini excavators, and for Bobcat requirements). However, they were aiming at the free market, as the supply of 8,000 units to Goldoni Keestrack proves. An architecture in step with the times and designed around the key requirements of compactness and power density.
The consecration comes with the extension of this approach to a 4- and 6-cylinder modular duet with 1.25-litre barrel (BxS 110 x 132). Named DX05 and DX08, they are expected to make their way among maxi excavators and a plethora of other off-highway applications and extend the application coverage of what has since become Hyundai.
We got a preview of a miniaturized model under a display case at the HD Hyundai Infracore stand at Conexpo in Las Vegas. In early March 2023, we were told that: “We started completely from scratch with a new electronic engine which has 5-litre and 7.5-litre displacement. Our target is both Stage V and China V. We see two different strategies to approach this kind of long journey. Reasoning from a future perspective, the market will reward a multitasking approach, and there will not be a winning solution. Maybe things will change in 2040 or 2050; until then, we have to support our engine business and that is why we are developing two different strategies for the internal combustion engine and the factory of the future”.
So, let’s summarise the last two sentences: the internal combustion engine of the future is the present and is called DX, which is officially Diesel of the Year 2025. A monopoly of the western industry until the arrival of the Rising Sun on the motoring scene, the Diesel of the Year stopped for the first and only time in the East in 2019. Five years ago, the award ceremony involved Kubota’s management and engineering staff. Now, let’s cross the Strait of Korea, because it is in South Korea that the award that has recognised the gradient of innovation of the diesel-cycle combustion engine since 2006 will move. Already set up in G-Drive format, for the needs of power generation, we are willing to bet on a forthcoming conversion to the marine sector.
Multidisciplinarity is one of the privileged parameters in the pedigree of the Diesel of the Year. Korean engineering has perfected the twin-stage to calibrate the supercharger with torque entry at low revs and rapid filling of the entire curve up to the apex point, approximately from 900 to 1,400 rpm. The 5-litre and 7.5-litre respectively reach up to 171 kW and 955 Nm and 254 kW and 1,460 Nm. Compared to the Korean engine maker’s previous models, there is an estimated 6% jump in power and torque for the 5-litre engine. Moving on to the DX08, it is estimated at 19% and 15%. The refined software and ECU, which were developed in-house, allow significant margins for customisation according to transients and work cycles. Speaking of elasticity, the DX05 and DX08 are also available with a single turbocharger with a wastegate valve. A prospect that fits with both partial electrification and possible conversion to hydrogen. Two options that Hyundai has firmly in its sights.
Back to Conexpo, “The software that controls the hybrid system is an in-house development by Hyundai. We can provide the full system, the engine and the electrified components. Hyundai also engineered the battery pack. We have the engine technology and the electrified system as well. So, we are able to provide to our customers a technological combination with the battery pack. We are talking about I-on lithium battery, 48 Volt for the smaller applications up till a 360 Volt offer for the bigger machinery. Anyway, the most demanding applications need a huge amount of energy, and they need an excessive battery pack volume. The requested energy is too much operating in a long time. For these reasons, we adapted our internal combustion engine to hydrogen fuel. We displayed an 11-liter displacement, the base engine is a diesel and gas engine that we converted into hydrogen. It delivers 300 kW and 1700 Nm and can be adapted to commercial vehicles, trucks and buses. It can be used also for excavators (about 30 and 34 tons) and construction equipment. It also fits gensets”.
This is what you call a thorough roadmap, a projection of Hyundai’s propulsion skills, which in Korea find virtuous synergies for electrification and digitisation.
We end with the presentation coming straight from Incheon.
“Developed for a wide range of applications, from construction equipment to heavy-duty trucks and generators, DX05 and DX08 engines are set to redefine the standards of versatility and reliability. DX05 and DX08 engines, belonging to 5L and 7.5L class respectively, have been developed with the latest technologies to ensure eco-friendly and cost-effective operations. These engines are scheduled to begin mass production in the fourth quarter of 2024. In developing the new DX engines, a key focus was on durability and performance. We have employed high-strength materials for major structural components, including cylinder block and cylinder head. For moving parts such as tappet, piston, and piston ring, wear-resistant materials were chosen to enhance durability. Furthermore, the use of two-stage turbocharger in the intake and exhaust systems not only delivers 21% increase in power output compared to previous engines, but also improves low-end torque.
Our years of research and development in combustion technology have culminated in these engines. We have achieved emission reductions and fuel efficiency improvement of up to 8% compared to previous engine models through advanced combustion technologies, optimized fuel injection systems, and enhanced air management.
Moreover, we focused on crafting a customer-centric product by enhancing serviceability and convenience. We’ve extended the maintenance intervals for fuel filter and oil filter from 500 to 1,000 hours, and implemented features like super impactor, auto tensioner, and HLA (Hydraulic Lash Adjuster) to ensure maintenance-free operation.”
To read the full article, click here or download the pdf.