F28 Diesel of the year 2020 Hybrid
Fpt F28 Diesel of the year 2020 Hybrid. We had a (video) catch-up together with Luca Giovenzana, Innovation Hybrid Chief Engineer for FPT Industrial. What can you tell us about the engineering approach the size of the F28 Diesel of the year 2020 Hybrid? Space management is one of the main and challenging aspects for the […]
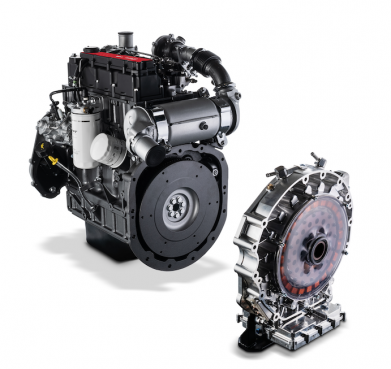
Fpt F28 Diesel of the year 2020 Hybrid. We had a (video) catch-up together with Luca Giovenzana, Innovation Hybrid Chief Engineer for FPT Industrial.
What can you tell us about the engineering approach the size of the F28 Diesel of the year 2020 Hybrid?
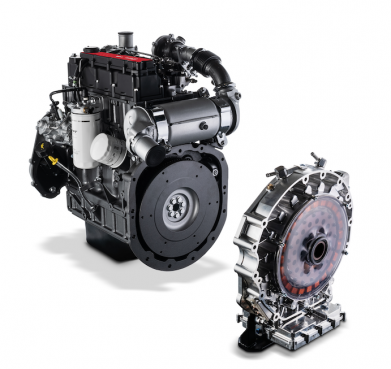
Space management is one of the main and challenging aspects for the success of the project. The F28 is designed for small to medium sized AG and CE applications. Hybridization allows engine downsizing while maintaining the performance today guaranteed by the F34 engine for this kind of machine. In fact, the compactness of the F28 engine facilitates the integration of electric machine and inverter, with the aim of maintain the footprint of the current power unit.
What approach in the design and bench testing phase?
The applications are many, with different installation layouts. The design of the hybrid system must be conceived as modular and compact in order to minimize the modifications necessary for integration in the engine compartment. The same modularity approach is also guaranteed by a common control strategy developed to optimize the benefits of the diesel and electric combination.
The reference hybrid architecture is Low Voltage (48V) and scalable in High Voltage. The maximum power for a Low Voltage system is between 20 kW and 30 kW. The 48V systems allow a greater simplification in terms of safety and maintenance than the High Voltage counterparts, which remain adopted for the heaviest uses. A choice to make with the customer depending on the application.
Details of electric motor and battery pack?
Off-road hybridization allows the electric machine to be used to improve the productivity and efficiency of the ICE, especially in load transients, thanks to the effect of electric torque assist. The batteries are the power reserve of the system. In the design, we analyze the typical missions of the vehicle application that guide the dimensioning of the system and in particular the capacity of the battery. In the selection we look for an optimization between required performance and overall dimensions and respect. We adopt lithium-ion batteries with state of the art technology.
What happens during the preparatory phase?
In the design phase, the analysis of the reference mission is fundamental. At the dynamic test bench, missions are replicated and detailed calibration of the relevant parameters, e.g. cooling system specifications, is carried out. Always according to the modular approach, a control strategy integrated with proprietary software is developed, which will optimize the distribution or torque distribution between thermal and electric motor to achieve maximum efficiency and plate performance.
What are the benefits of a hybrid vehicle compared to conventional diesel and gas versions?
The electric motor allows the introduction of new operating modes. Thanks to electric torque assist it is possible to increase productivity and improve dynamic operations. Traditionally operated attachments can be electrified mechanically-hydraulically, with the advantage of lower power consumption. In this way the thermal engine works in a more efficient operating area, combined with lower fuel consumption.
DO YOU LIKE GAS? CNG AND BIOMETHANE TOO