Flash Battery made a big step forward
With over six million invested, Flash Battery completed a crucial step with the automated module assembly line with laser welding
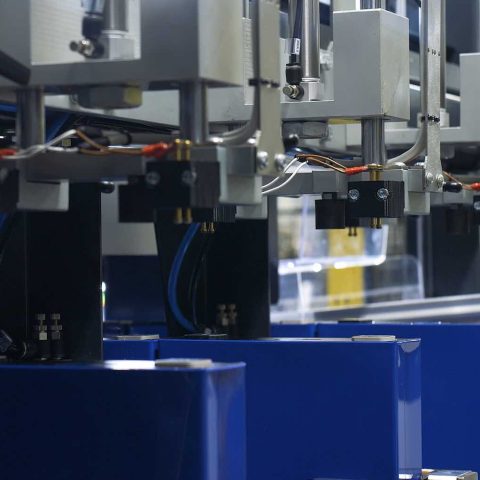
Flash Battery sped up the domestic footprint of the energy transition. What does this mean? The new automated module assembly line with laser welding is operational at the Italian headquarters in Sant’Ilario d’Enza, between Parma and Reggio Emilia. Regarding the reasons for Flash Battery’s brilliant performance, founder and CEO, Marco Righi, told us (you will find confirmation in the March-April issue of POWERTRAIN International): “We do everything in-house which makes it easier to keep constantly up-to-date.” And so, it seems, will be increasingly that way.
Assembling modules with prismatic cells
More than six million euros have been invested in this breakthrough in production capacity, which is spread over an area of 2,200 square metres. It is a department designed to accommodate the entire welding and mechanical integration process in a controlled environment. Annual capacity reaches 90,000 modules, making this line not only the most advanced but also the most productive in Italy for the assembly of prismatic cell modules.
Flash Battery: Independent, integrated, European
In the words of Marco Righi, Flash Battery has chosen to keep the key competences of the process within the perimeter of its headquarters: from the proprietary battery management system to mechanical and electrical design, through to process validation and predictive maintenance. With the integration of the new module assembly line, the company completes its internal production consolidation process, bringing under its direct control also the soldering and assembly activities, hitherto entrusted to external suppliers.
The new assembly line is designed for rapid changes between configurations, handling 13 module variants with changeover times of under ten minutes. This enables Flash Battery to respond quickly to even the most specific requirements, supporting customers in building optimized electrical systems with no compromise on timing or quality. Production’s ability to adapt thus becomes a real competitive advantage. Laser welding is also a strategic technological choice, ensuring stronger mechanical and electrical joints, greater resistance to vibration and lower energy dispersion. It’s a key step towards achieving stable, reliable performance – especially in industrial applications subject to high stress. The line is divided into four key stages: Automated loading and inspection of cells using optical scanning and precision sensors. Module formation with robotic stacking and positioning of components into a containment structure for subsequent welding. Laser welding of frames and busbars, which connect the cells together to ensure efficient, long-lasting electrical connections. Final conformity testing, including for safety, insulation and mechanical strength Only modules that pass these tests are labelled and cleared for use in Flash Battery’s battery pack assembly lines.
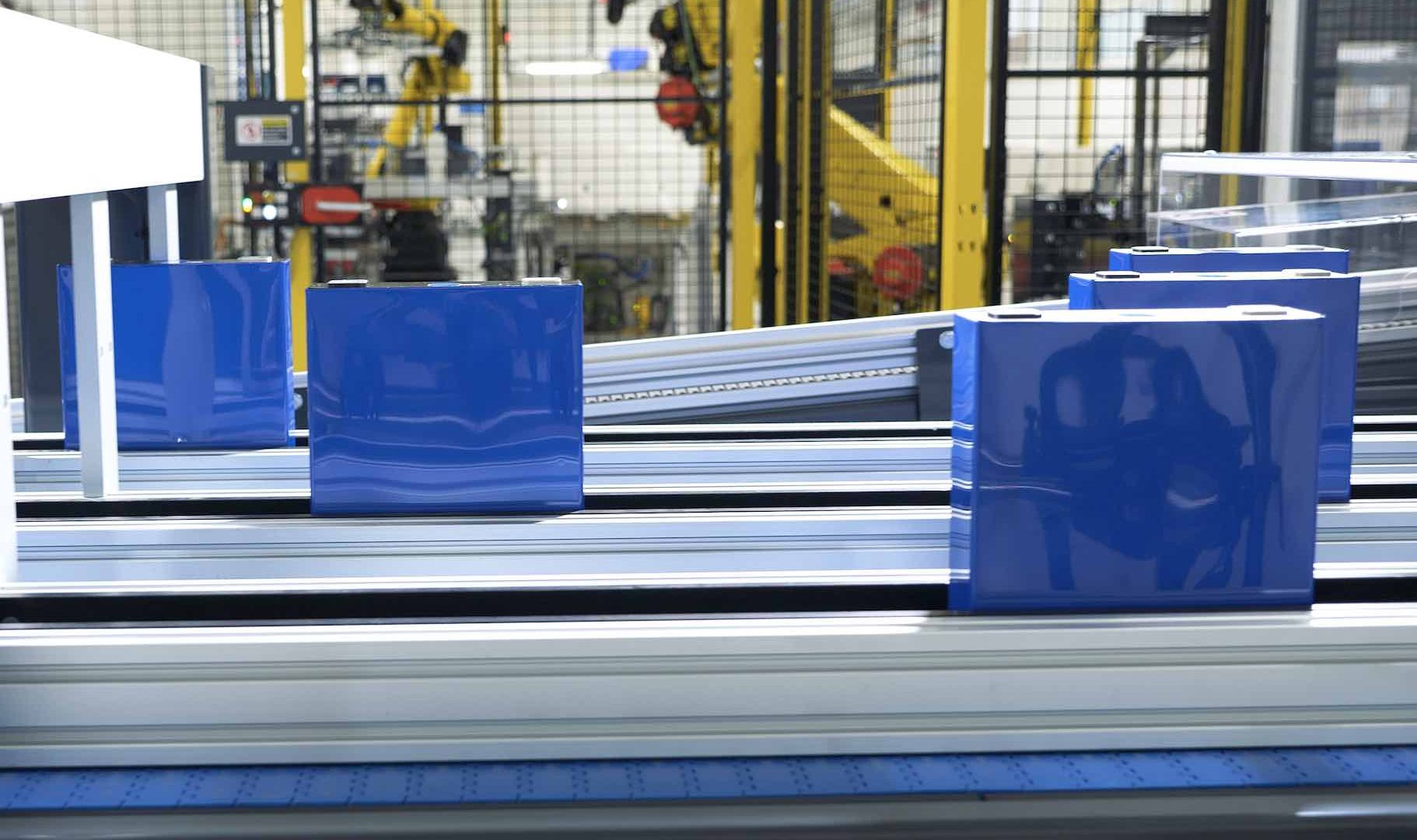
For a Made in EU supply chain
In concluding, the words of Marco Righi, again: “With this new line, we’re taking a decisive step towards a more autonomous, effective and reliable production model. Integrating production capabilities enables us to respond promptly to customer needs and deliver tailormade solutions at the highest levels of quality and performance. It’s a crucial competitive edge, especially in a constantly evolving market. Thanks to this production autonomy, and the upcoming launch of European gigafactories for LFP cells,
we’ll soon be able to offer our customers a fully European supply chain”.