Bonfiglioli electrification: primary and all-round
The interview with CEO Fausto Carboni, published in the January-February issue of Powertrain, helps us understand the challenges that Bonfiglioli will face during the year.
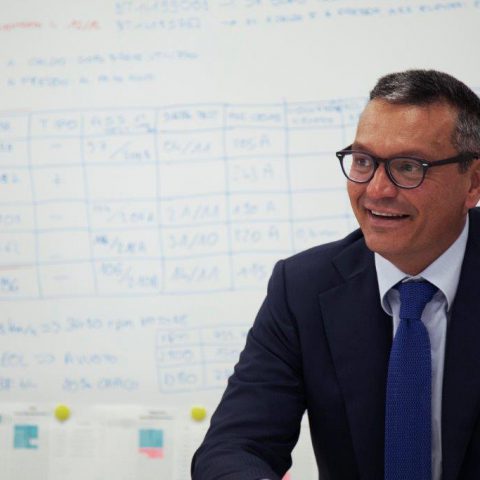
“Bonfiglioli wants to put itself forward as a partner supporting customers in the transition towards the electrification of work equipment,” says Bonfiglioli Group’s CEO Fausto Carboni at the outset.
“Let’s start with the reducers actuated by hydraulic motors, which in turn are driven by an ICE. In this case, hydraulic motors can be replaced by electric ones. We have built competences from our experience with industrial automation, which is expressed in our permanent magnet motors, high power density and compact size. Bonfiglioli offers the market a midway solution under the name of “all-in-one”. It comprises an electric motor for machinery in a medium power range, an inverter and a PCU – power control unit. The entry-level PCU version coming from automotive applications only features the accelerator pedal signal (open/closed) and is thus unsuitable for work machinery characterized by more complex working cycles as well as multichannel controllers. In most cases, full electrification has to be seen as the ultimate goal, not the starting point. This is why we offer primary-level electrification and all-round electrification. We combine the experience gained with working equipment – subject to energy efficiency requirements – with that gained in industrial automation -a field that’s very stimulating, complex and demanding.
Ecomondo Key Energy hosted a preview of the “all in one” coming in two versions: the first made for work equipment fitted with single-stage final drives that slows down the electric motor to align it with combustion engine speed. There is a gear reduction ratio needed to bring the axle to the speed required by the machine’s transmission. The other version includes a steel gear reducer with differential that can be used on any vehicle needing one output shaft for two half-shafts.”
Green economy also means reconciling the productivity, emission reduction and equipment manoeuvrability requirements. What’s Bonfiglioli’s value added?
In all of these respects, it all boils down to software programming. There is nothing a machine cannot do, once that the logics of motion control from industrial automation are applied. The technology is there, but the sector specific application is still to be invented.
Currently, the market still lacks widespread competences in this field. That’s why we think we’re offering equipment professionals a strategic opportunity with our primary-level electrification mode. It took our customers years to gain an in-depth knowledge of hydraulics – it actually marks the difference between a machine and another – and become skilled system engineers. When switching to electric, said knowledge tends to get back to square one. You need to be familiar with electronic controls and the system providers themselves can fill this gap.
Bonfiglioli set up a spin-off from their mobile division, which will provide skilled resources from this ad-hoc department. The professionals tackling these needs that we may term “disruptive”, have the required flexibility to tackle the mission we have entrusted on them.
How is Bonfiglioli Group doing through the hardships of semi-finished material/component supply problems and booming energy and logistics costs?
I feel I can say Bonfiglioli is in a position to withstand these stress factors. We never resorted to massive delocalization. The plants of China, India, Brasil, USA, Vietnam, have been working for some 10 years now based on the local-for-local principle. You produce for your reference market so you avoid shipping containers, differently than those who delocalized production to import from low-cost production sites to western markets. What worries me most is the shortage of raw materials.