Battery-hybrid collaboration between Solstad Offshore and SEAM
Norwegian offshore supply and services company Solstad Offshore ASA has one of the largest fleets in the industry, with 83 vessels serving customers globally of which 10 have been converted to hybrid. SEAM is one of the key partners.
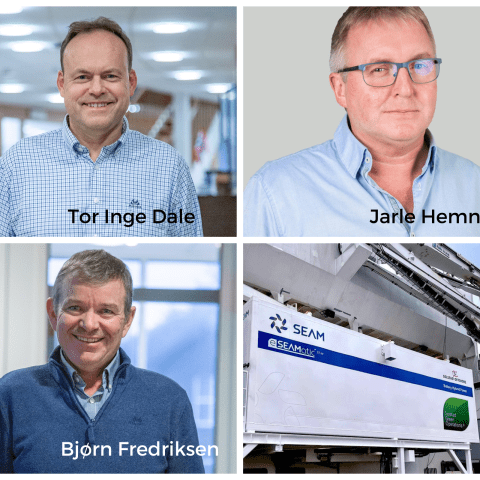
Hybridization has emerged as one of the key strategies to address the environmental challenges facing the shipping industry. What can we learn from shipowners who invested heavily as first movers in this propulsion revolution, at a time when its viability was still up for debate? What results can they show, and where do they stand competitively today?
Most industry experts now agree that hybrid solutions are the best approach to optimizing energy use on board while ensuring compliance with emissions regulations. In simple terms, hybrid propulsion describes the use of two or more energy sources to power a vessel. The main aim is to reduce fuel burn and emissions while maintaining required power and performance. In most cases, this involves combining a conventional combustion engine with an electric motor or other clean energy source.
Hybrid propulsion incorporating energy storage technology, such as batteries that can be used to provide additional green power as needed, has become increasingly popular. The ferry sector was first out, but hybrid solutions are becoming steadily more common in other shipping segments as well, including offshore.
Solstad Offshore: extensive retrofit program
Norwegian offshore service and supply company Solstad Offshore ASA has one of the sector’s largest fleets, with 83 vessels serving clients globally. It has been in the vanguard of sustainability efforts, retrofitting 10 existing vessels to hybrid propulsion between 2019 and March 2023. The first to undergo the process was the 5,300-dwt PSV Normand Server (built 2011), and there are more in the pipeline.
“Hybrid technology is right now the only commercialized green technology that can be implemented on offshore vessels today. Having these 10 retrofitted vessels makes us one of the largest users of battery technology in the offshore business worldwide. It’s not cheap, but the Capex outlay is compensated by Opex savings over 10 years’ time, mainly on client fuel savings but also on reduced engine maintenance cost,” says Chief Sustainability Officer at Solstad, Tor Inge Dale.
The journey started back in 2009, when Solstad launched its “Solstad Green Operations” campaign designed to incrementally phase in measures to reduce and track fuel consumption and emissions.
The campaign has evolved with the introduction of innovative methods to optimize energy efficiency. Alongside hybrid propulsion, these include Green DP (an advanced dynamic positioning solution that significantly reduces fuel burn through predictive control), reducing power offtake by onboard actuators and the use of shore power when in port. Solstad also plans to implement new technologies on the retrofitted ships as they become available.
Ambitious targets
He emphasizes that close collaboration with key partners is crucial in developing functional, energy-efficient solutions for the fleet.
SEAM is one of those key partners, supporting Solstad in the development and integration of not only hybrid systems but also energy management solutions, drives, shore connections, batteries and implementing class society DNV’s battery (power) notation.
“Having a counterpart who we can rely on is very important. SEAM is one of the few suppliers that we’ve chosen to forge a very close relationship with. They’re very quick at coming up with good solutions that we know will work, and not least they deliver within the timelines.”
SEAM has worked on developing and optimizing hybrid technology since 2016 and firmly believes that hybrid-electric is the key to unlocking even better energy efficiency in the future.
“Hybrid energy systems are an optimal choice for preparing offshore vessels for future zero-emission technology and regulatory demands. They generate immediate emissions reductions, increased energy efficiency and reduced costs, as well as allowing for newer, more efficient fuels and technologies down the road – thus reducing the cost of investing in brand-new systems and costly retrofits or newbuilding projects later,” says SEAM Project Manager Jarle Hemnes.
“The proof is in the pudding”
So far, Solstad has saved over one million tonnes of CO2 through its Solstad Green Operations campaign. Each of the 10 retrofitted vessels themselves save an average of 21% of fuel during typical operations. In some cases, such as the latest diesel-electric retrofit, the 6,000-dwt CSV Normand Ocean (built 2014), results are as much as 25% fuel savings in field and mobilization/demobilization operations, and 20% in DP2 mode.
Solstad Technical Manager Bjørn Fredriksen has witnessed first-hand the increase in both operational and economic efficiency on board, as well as the accompanying social benefits. “We’re saving a lot of maintenance hours on the engine when we’re running on batteries. Instead of two engines we use just one, and when connected to shore power we shut all engines down and just run on the battery. The experience for both the crew on board and local residents near the quay has improved dramatically as there is much less noise pollution.”
Keeping clients on side
Solstad is constantly on the lookout for more efficiency technology to install on its vessels over time. “Battery technology alone will not take us to our 2030 goal, so new green innovation and alternative fuels such as hydrogen, ammonia or methanol – which aren’t currently available in the market – will need to be deployed in the coming years,” says Dale.
Exploring new-to-market solutions requires close cooperation with clients who believe in and are willing to invest in future potential, Dale says. “Our strategy is to deploy the best technologies on our vessels as they become market ready. We will need to implement green fuels just like we’ve done with hybrid technology. Together with key partners like SEAM we can conceptualize ideas and get our clients on board,” he says.
This makes Solstad something of a test bed for new technology, but to realize their ambitions they depend on trusted suppliers like SEAM to make it happen. “We can then go to our clients and say, ‘do you want to join us in installing and testing this equipment so we can get emissions right down?’. This kind of collaboration on both the supplier and client front is the only way we’ll get to net zero,” concludes Dale.