Siemens’ virtual prototyping. The advanced design of electric motors for use at sea
Siemens held a webinar focused on the advanced design of electric motors for use at sea, explaining the features and benefits of virtual prototyping as an integrated and innovative approach. In fact, today the tools available to designers are manifold and recall some of the hottest trends in the sector. Virtual prototyping and digital twin […]
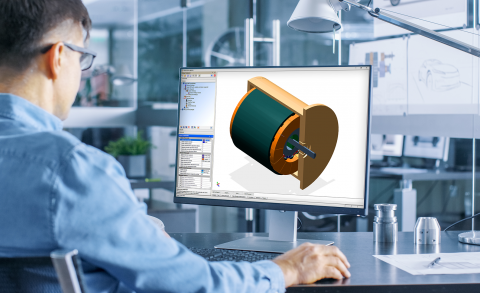
Siemens held a webinar focused on the advanced design of electric motors for use at sea, explaining the features and benefits of virtual prototyping as an integrated and innovative approach.
In fact, today the tools available to designers are manifold and recall some of the hottest trends in the sector. Virtual prototyping and digital twin are concepts that go in the direction of greater design freedom, without jeopardizing the time it takes to create a product or rather risking wasting precious resources in a preliminary stage.
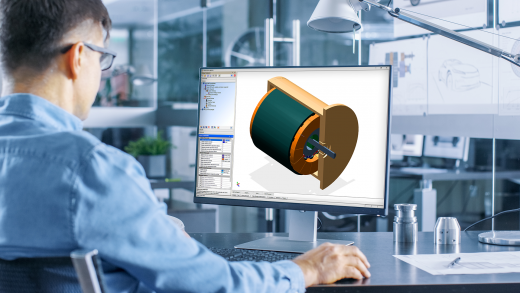
The importance of being compliant to IMO regulations
All this meets a need that is getting quite urgent nowadays, especially when we think of the yachting sector or light commercial applications. We are talking about the compliance to IMO regulations on emissions reduction. All this is closely related to the concepts of hybridization or, in the longer term, electrification of propulsion systems. It should not be forgotten, however, that electric motors for vessels must necessarily guarantee a high level of performance (and reliability…) in potentially complex environmental conditions.
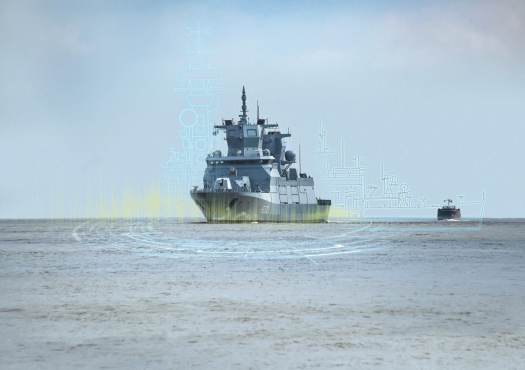
Siemens: how to increase performance and reliability even before prototyping
«Our goal is to create alternative propulsion designs; we want to be able to validate and verify cycles even before prototyping», explained Darren Nunes, Simcenter Solutions Consultant, Siemens Digital Industries Software. «We also want to be able, through an improved design, to increase performance and reliability without having to compromise in terms of costs. To do this, it’s necessary to rethink the vessel development process by creating a so-called digital twin».
System simulation is the expression chosen by Siemens’ experts during the webinar. «It is an ecosystem in which we have all these multi-physics and multi-dynamics capabilities linking together in one platform. It has several libraries: control logics, electric, hydraulic and mechanic, all of them performing together. At this stage, the typical design issues are: is the motor powerful enough? What is the time response of the system? Is there any risk of vibrations? How to optimize the control system design?».
The design tools provided by Siemens
The practical answer to all these questions was provided by Adrien Perregaux, Solutions Consultant, Siemens Digital Industries Software, and can be summarized into the Simcenter Motorsolve software, a design software that «gives the opportunity to rely on a series of tools (Heeds or Amesim are two examples) with the aim of generating the digital twin».
Adrien Perregaux also talked about the Motorsolve software in details through some practical examples. It is indeed a two-step process. «The first step is to define the operating conditions. Starting with the general settings, we see voltage, current and speed, number of poles or slots; then we need to get more details, being able to define the geometries and the nature of configuration for our rotor layout. Then, we have to go for the geometry of the stator. The last reference in this process deals with the winding layout. Once you set up your motor, we need to actually start to review and do some experiments. There’s a series of experiments based on a 2D FEA (Finite Element Analysis, ed). Then, some thermal experiments are possible. Once our design is complete, we can address the exports by using some dedicated programmes».
According to the experts from Siemens, these tools allow users to minimize both Opex and Capex, then operational expense and capital expense, respectively. In particular, it would be possible to reduce Capex up to 41 percent as well as Opex up to 32 percent.