Volvo Penta and CMB.Tech: how hydrogen dual fuel engines can help reduce emissions
Volvo Penta’s hydrogen dual fuel engine, based on the EU Stage V D8 platform, incorporates CMB.Tech’s hydrogen technology. This allows applications to run on a mix of hydrogen and traditional fuel; and in the event hydrogen is temporarily unavailable, they can operate on diesel or even HVO.
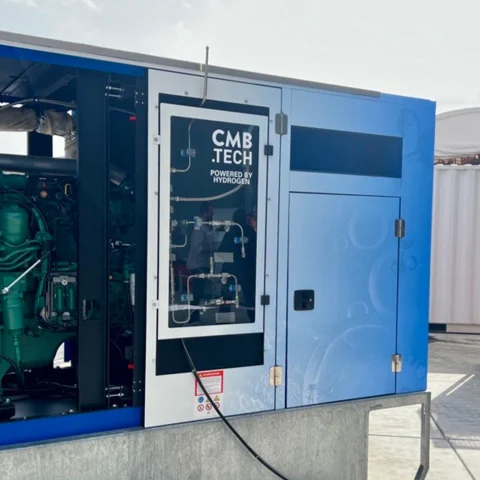
Volvo Penta has partnered with maritime group CMB.Tech to bring forth a production of hydrogen dual fuel engines to aid a selection of customers through the energy transition. Collaboration is key in realizing the solutions – Volvo Penta, its customers, and CMB.Tech are working together in various dual fuel field tests for different off-highway and power generation applications.
Three low-to-zero-emissions pathways are in focus – electrification (BEVs), combustion engines that run on (or partly) renewable fuels and fuel cells. Dual fuel engines are a bridging technology to reduce emissions. Combustion engines that run partly on hydrogen can leverage existing technologies and provide a lower-emissions option for specific use cases to meet increasing decarbonization needs from customers while hydrogen infrastructure is still being rolled out.
What is a hydrogen dual fuel engine?
This dual fuel setup is a combustion engine enhanced with a hydrogen injection system, allowing it to operate on a blend of hydrogen and diesel (or HVO). Early hydrogen dual fuel engine trial data has revealed a reduction of up to 80% in CO₂ emissions. This solution capitalizes on existing combustion engine platforms while providing a scalable way of reducing greenhouse gas emissions.
How does a hydrogen-diesel dual fuel engine work?
The Volvo Penta Stage V D8 engine is equipped with CMB.Tech’s dual fuel hydrogen technology. Hydrogen is released from storage tanks and brought to low pressure, then injected into the engine’s air intake. Aspiration of the hydrogen reduces the amount of diesel required to produce the same amount of energy from combustion. CMB.Tech’s injection system is designed to communicate with Volvo Penta’s engine controller to switch between dual fuel mode and diesel-only mode seamlessly. As such, hydrogen mix lowers diesel use, potentially contributing to lower CO₂ emissions. When hydrogen is injected into the cylinder, the hydrogen-air mixture is compressed, and a small amount of diesel is injected. The diesel auto-ignites and the hydrogen co-combusts, driving the piston down. The cylinder then empties during the exhaust stroke. If the hydrogen supply runs low, the engine can operate entirely on diesel or HVO, maintaining uptime and performance.
In what kind of applications could the dual fuel engine be used?
The hydrogen dual fuel engine, built on Volvo Penta’s D8 EU Stage V platform can be applied in a variety of settings. It is ideal for off-highway segments like port handling, in applications like straddle carriers and RoRo-tractors, where uptime is crucial during regular duty cycles. This segment is rapidly advancing, with hydrogen refuelling infrastructure emerging in key markets to complement electrification initiatives.
Additionally, it is a viable option for power generation in stationary applications, such as gensets, where it delivers efficient and reliable energy using a mix of conventional and hydrogen fuel. Stationary applications are subject to other regulations compared to off-highway ones, which may allow for flexibility in the adoption of alternative energy solutions, including lower-emission options.
To ensure the long-term feasibility of hydrogen dual fuel combustion technology in real-world settings, rigorous field tests are conducted in collaboration with OEMs and customers. Below are two examples: one in an off-highway application and another in stationary genset applications.
Does having hydrogen in the fuel mix affect engine performance?
The torque and power curve of a hydrogen-diesel dual fuel engine is comparable to a regular diesel engine and with lower CO₂ emissions. The nitrogen oxide (NOx) and particulate matter emissions are not affected by the system. Lastly, hydrogen may improve the process by positively affecting the after-treatment system, including the SCR (Selective Catalytic Reduction), especially on low loads. Similar to the diesel sibling, this dual fuel solution is designed to meet the most stringent off-highway emission legislations, EU Stage V.
How large of a hydrogen fuel tank will I need?
It depends on how often you have the opportunity to refuel. Compressed hydrogen at 350 bar takes up significantly more space than diesel, approximately 10 times the volume. So you will likely need to reassess your refuelling habits and expect to refuel more frequently than you do today, should one wish to run on dual fuel continuously.
Key considerations when adopting hydrogen solutions
Navigating the energy transition comes with several challenges and opportunities. Many factors can be at play, from energy strategies and ways of working, to cost and governmental initiatives that may motivate changes. However, two key considerations framing your decision to adopt the hydrogen dual fuel solutions would be:
• The energy transition: What does your decarbonization strategy look like? What are your cost considerations, timelines, and need to maintain uptime as you transition? The hydrogen dual fuel engine can be used as a stepping stone to reduce tailpipe CO₂ emissions especially if there is more immediate access to green hydrogen.
• Access to hydrogen: Do you have a refueling station nearby? Is there a plan for securing a supply of green hydrogen? Is there access to mobile hydrogen refueling? Then, dual fuel may be a good solution to start decarbonizing.
Is hydrogen fuel safe?
Hydrogen is an abundant, non-toxic, colorless, odorless tasteless gas, and potentially clean and efficient energy source. It is 14 times lighter than air. If released, it rises and dissipates quickly. However, hydrogen requires safe handling in the same way as natural gas and petrol does. The design of the Volvo Penta/CMB.Tech hydrogen dual fuel setup focuses on safety and reliability. The engine operates with a low-pressure system, keeping hydrogen below 10 bars. In the event of a safety concern, it automatically shuts down, seals all hydrogen tanks, and switches to diesel, aimed at ensuring that your equipment continues to run without interruption.