Alexei Ustinov and Cummins’ strategy for the near future
Cummins is currently developing very different aspects of its business with different strategies concerning Stage V and alternative solutions like gas, electric and hybrid. We wanted to discover more so we went to talk directly to Alexei Ustinov, Vice President Off-Highway Engine Business at Cummins, and this is what he shared with us. Connection with […]
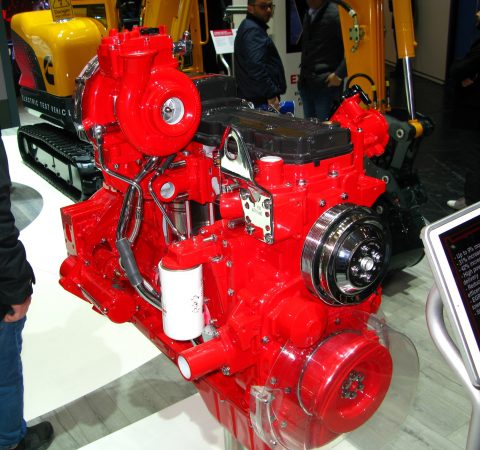
Cummins is currently developing very different aspects of its business with different strategies concerning Stage V and alternative solutions like gas, electric and hybrid. We wanted to discover more so we went to talk directly to Alexei Ustinov, Vice President Off-Highway Engine Business at Cummins, and this is what he shared with us.
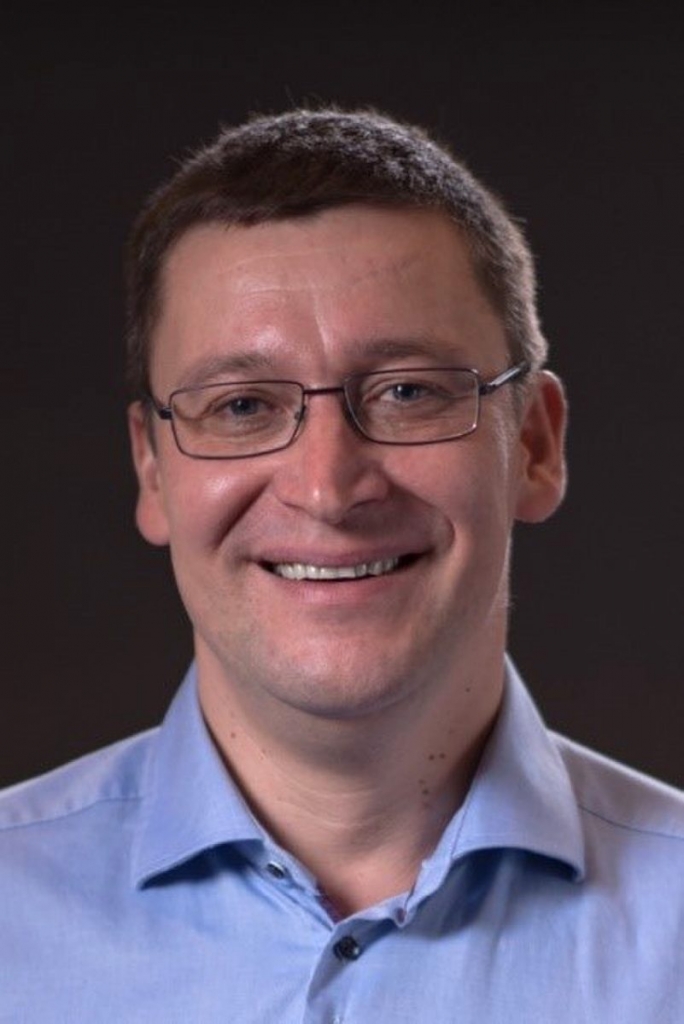
Connection with Westport. Why CNG and LNG couldn’t become the real, immediate, solution for the next decade?
We are a global company and we believe it is very important to offer a wide portfolio of options which include electrification, natural gas and diesel engines. We are developing solutions in all of these areas.
If you talk about Europe, the ultra-low emission zones in major cities are more likely to drive electric power, particularly in the bus segment. The cities are less likely to take an intermediate step, such as gas, if they can go straight to electric. We do have the product available should our customers need it.
Green, bio, sustainable. It’s a benchmark for marketing. Is it really the ‘truth’ concerning full electric?
If you talk about electrical drives the systems are stable, but the storage of the electric is more challenging. I think it will take some time for the market to move forward on this due to the economics – cost and capability. The industry is at an intermediate step until the next disruptive technology for energy storage comes in. This will change, and we must be ready, which is why Cummins have invested in battery technology companies.
CUMMINS WORDS ON THE HSK78G SERIES AT MEE DUBAI 2019
And the next step couldn’t be hydrogen?
It could be, we are also exploring opportunities in this segment as well. Here, at Cummins, we try different options to be sure that we’ll able to offer different solutions to the customer for emissions compliance. We are a 20 billion Euro company and we have economies of scale that other companies don’t have, to invest in different options, try them and bring them to market in a dependable way.
Electric is an option available in particular for city buses and pick-up trucks as well?
We are concentrating mostly on buses, as these are moving first due to the strong focus on public transport. We don’t expect so much focus on pick-ups. We are also studying off-highway equipment, as we expect a lot of cities to include construction equipment in their zero emissions legislation. In this case we need to have an electric option, and is why we exhibited the electric excavator at Bauma.
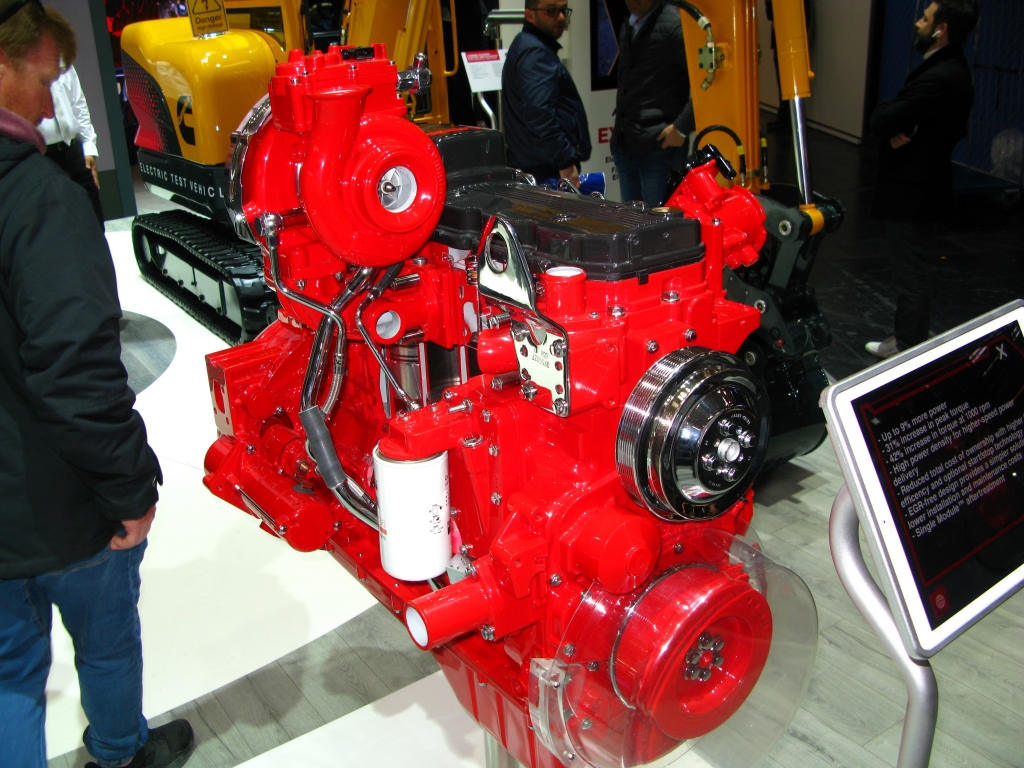
Can you choose the right applications for the hybrid and the electric applications?
Obviously if you have zero emissions requirements you need to go electric, based on a good business case of course. With hybrid it’s important to consider the load the equipment needs. A balance between diesel and electric could be more efficient for higher load equipment or those that operate for long hours. To date hybrids have been popular in buses because they recover the energy from braking in traffic which can be stored and used to improve efficiency.
For off-highway I expect smaller excavators up to 7 tons will go electric in the next 5 years, with the bigger excavators continuing to use diesel power. Some of the bigger excavators can go hybrid, because there a number of opportunities for energy recovery in the way they operate, which some of our OEM partners are currently testing.
The interesting fact about excavators, relating to hybrids, is almost all of these are diesel hydraulic. They have hydrostatic systems to drive all the components of the machine. So, if you have energy recovery you can make the whole machine much more economical.
What off-road applications are the best target for Cummins in terms of cycle life, loads and stress?
If you talk about off-highway applications, we hold a quite significant market share in engines for hydraulic excavators. The second segment which we produce in large volumes for is front-end loaders. Both are demanding application in terms of the duty cycle and load factors, which is supported by the durability and reliability of Cummins products.
There are so many players in these segments in the construction industry. Being a global supplier like Cummins means we can support them wherever they manufacture or sell; North America, South America, Europe, Russia, India and China.
QSK 60 and 95. Are they perfectly suitable and shaped for smart grid? And what about data centre?
They are very well suited, it’s a good option for the customer in particular in terms of power density, where you can reduce the footprint. This is particularly important for the data centres.
Is removing EGR a definitive solution for your ICE lineup?
EGR is one technology to reduce NOx and help meet emissions requirements. There are two reasons why we decided to eliminate EGR in the development of Stage V engines. One is to reduce engine installation costs. EGR is more complex and requires a larger cooling package. The second reason is for our engines to be applicable around the world. It is challenging to operate EGR systems in the areas where fuel is low quality or the sulphur in fuel is too high. So, using Cummins latest SCR and DPF technology, we can avoid EGR and the installation is more cost effective, more reliable and more global.
Can you explain the recipe to upgrade the performances of Stage V engines, in particular 3.8 litres, the best in class of its displacement range?
We recognized that one of the key trends in diesel engine manufacturing was to increase power density, doing more with less. For Stage V we didn’t just adopt the usual solutions of turbocharging and injection systems. We used different materials to enable higher combustion temperatures. Normally, to reduce NOx you need to reduce the temperature of your combustion process. In this case your efficiency and your power density are reduced. For us, we increased the combustion temperature to improve the power density, and managed the NOx emissions through our latest SCR technology.