CMD Eco20X. The second part of our interview with Maurizio La Villetta
CMD ECO20x micro-CHP system delivers up to 20 electric kilowatts and 40 thermal kilowatts generated by the product of gasification of residual wooden scraps. In this post, we published the first part of the interview with Maurizio La Villetta, R&D Manager at CMD. Here is the second and last part. Let’s start again from CMD […]
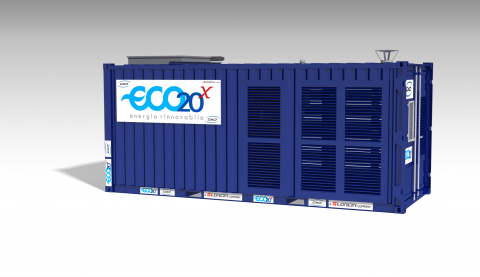
CMD ECO20x micro-CHP system delivers up to 20 electric kilowatts and 40 thermal kilowatts generated by the product of gasification of residual wooden scraps. In this post, we published the first part of the interview with Maurizio La Villetta, R&D Manager at CMD. Here is the second and last part.
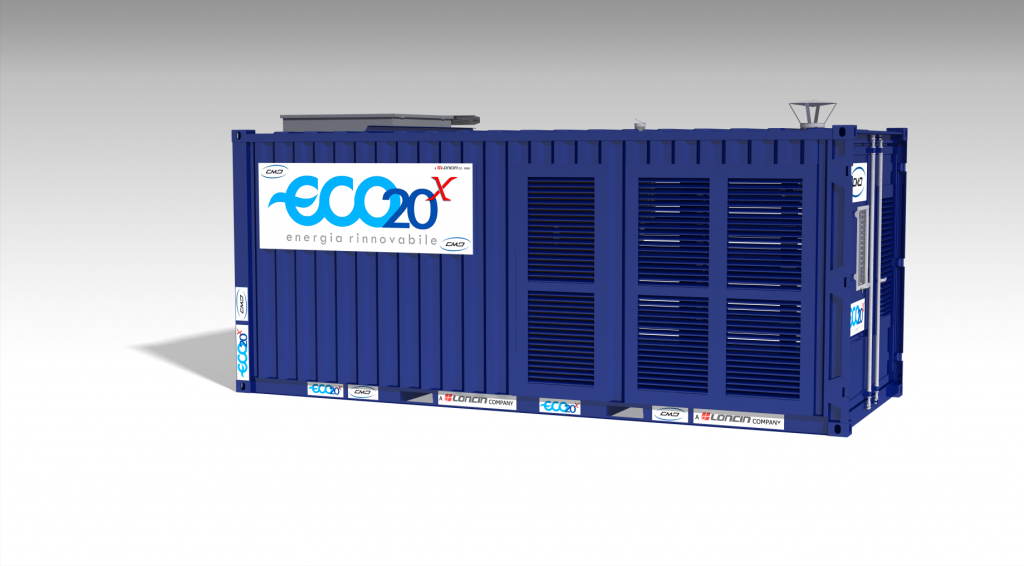
Let’s start again from CMD ECO20x.
The machine has an average consumption of 25 kg/hour for a total operation up to 7,500 hours/year, using class A1 wooden scraps. For biomass/residual materials other than wooden scraps class A1, average consumption, annual operation and overall plant efficiency, must be evaluated from time to time, both on the basis of chemical-physical investigations carried out on the raw material that the customer intends to use, and on related experimental tests of functionality, carried out on our plants at the R&D Energy Department in Caserta. Thanks to intensive research, conducted in synergy with excellence in this field, such as universities and research centers link the CNR in Naples, today we are able to define the operation of the plant already on the basis of laboratory investigations, conducted on the material to be used in feed to the micro-CHP and, consequently, define any pre-treatment and process logic set by PLC, as each type of material may need a specific protocol.
What can we say about the plant functionality?
Although the ECO20x features a capacity of 20 ekW and 40 thermal kW, from a technical point of view it could be used in clusters (several plants arranged in parallel). In this sense, we should be making a premise: in thermo-technical systems and in the management of electrical and thermal loads of a structure, often the load curves are not fixed-point, except for those industrial processes that need well-defined electrical and thermal requirements during daily operation.
For specific applications, the load curves can be extremely varied and, if the adjustment is entrusted to a single plant, the partialisation could produce efficiency reduction and the consequent increase in consumption connected to the plant management.
For these circumstances, it is always preferable to work in clusters so to switch the systems on and off according to demand. Such a concept can be declined with the CMD plant, in fact the management of a cluster of ECO20x systems makes it possible, on the one hand, to follow the load curves and, on the other hand, to use a specific maintenance program, an aspect particularly felt for biomass plants.
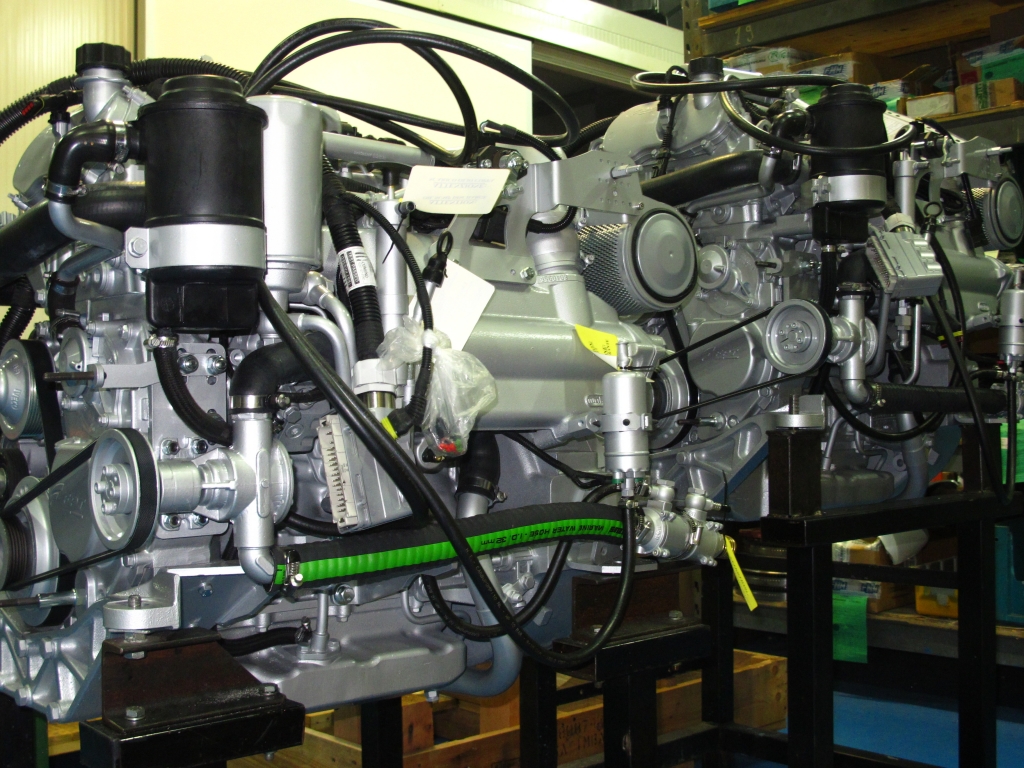
What about maintenance, then?
One of the main features of the ECO20x is to have a specific maintenance plan, calibrated according to the hours of operation. In fact, it is possible to closely correlate the type of maintenance intervention to the operating hours of the machine. The hours of operation can be read by the plant operator through the PLC. In this sense, the ECO20x architecture facilitates the operator during the assembly and disassembly phases of the components to be subjected to ordinary and/or extraordinary maintenance.
The plant operator, chosen by the customer, is properly trained at our headquarters and, at the end of the training course, receives a certificate on the operation and maintenance of the micro-CHP. The operator is then accompanied to the plant management, also after the installation at the customer’s premises, thanks to remote control and assistance service and, in case of particular difficulties, a team of our technicians is ready to intervene on site.