Cummins and Darlington, ‘a significant upgrade’
We went to Darlington, UK, at Cummins' European headquarters, to see for ourselves the new Powertrain Test Facility
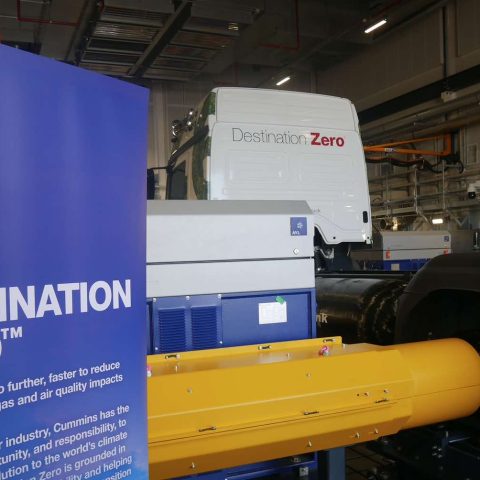
A “significant upgrade” is the message that came loud and clear from the opening of the new Powertrain Test Facility at the Cummins Darlington Campus, in UK. These are words from Felipe Rocha, General manager Europe On-Highway for Cummins.
Cummins’ new Powertrain Test Facility in Darlington
Among the challenges imposed by the explosion of vehicle power sources and the technologies serving them is the evolution of testing procedures. Cummins has equipped itself to meet these needs of OEMs. Following an investment of more than £13 million, the 738 sq. m. two storey facility significantly increases Cummins’ testing capacity in Darlington with fully robotic driving with manual or automatic transmission, road grade and load simulation, wheel-slip simulation, and engine duty cycle recreation.
THE NEW PILOT FACILITY IN GERMANY
New energy? Hydrogen, certainly, which involves upgrading safety systems. The test center building provides three levels of safety, relating to inhalation, detection and blast. Jonathon White, Vice President, Engine Business Engineering, said: “The new centre enables Cummins to develop and test a wider range of vehicles and machinery powered by hydrogen, renewable natural gas, advanced diesel, or battery electric. It is a key part of our Destination ZeroTM strategy to reduce the greenhouse gas and air quality impacts of our products – helping our customers in their energy transition, whatever solution they chose.”
Real world emissions…
As Felipe Rocha pointed out: “Real-world emissions are currently receiving a lot of emphasis. We are able to accomplish that and conduct tests with far greater precision thanks to this facility. Additionally, we observe that this facility has a great deal to offer us in terms of our ability to collaborate with OEMs and customers. There are many things they are prepared to accomplish on their own as they consider developing diesel or battery electricity, but we might be able to work with them in our test center.”
…and Virtual Engineer Robotic Assistance
Vehicles are tested under robotic guidance, not by humans, to ensure maximum safety for operators and assets. This guidance has a name, VERA, that stands for Virtual Engineer Robotic Assistance. Cummins engineers are expanding their capabilities using highly advanced dynamometers to test chassis-installed powertrains. Previously focused predominantly on engine testing, they can now develop full drivelines for on-road use, from compact SUV size to 44-ton trucks and double-deck buses, plus off-road use in construction and agricultural machines. These can be two or four-wheel- drive.
WE WERE IN POLAND TO SEE THE NEW REBUILDING CENTER
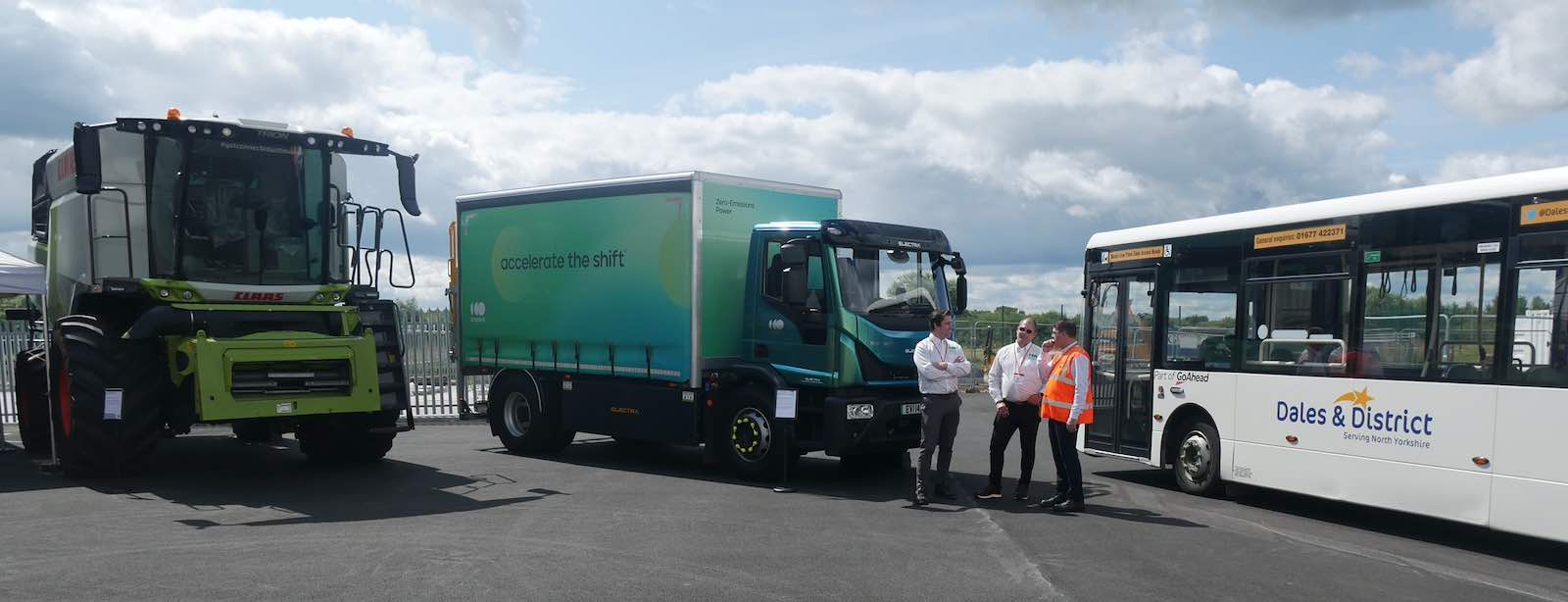