E-Polyhedron. How many faces has got the electric motor?
E-Polyhedron: How many faces has got the electric motor? It’s really difficult to say but we have a certainty: the spread of electrification has revitalised the powertrain and multiplied its players and features (do you want to know more about BATTERY PACKS?). E-Polyhedron: Lotus Engineering Part of this E-Polyhedron is “Lotus Engineering, who is launching a […]
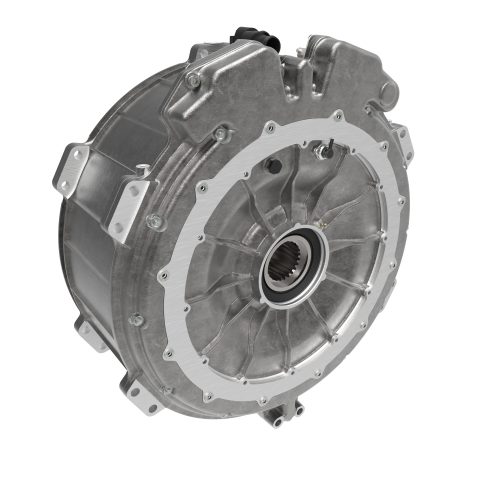
E-Polyhedron: How many faces has got the electric motor? It’s really difficult to say but we have a certainty: the spread of electrification has revitalised the powertrain and multiplied its players and features (do you want to know more about BATTERY PACKS?).
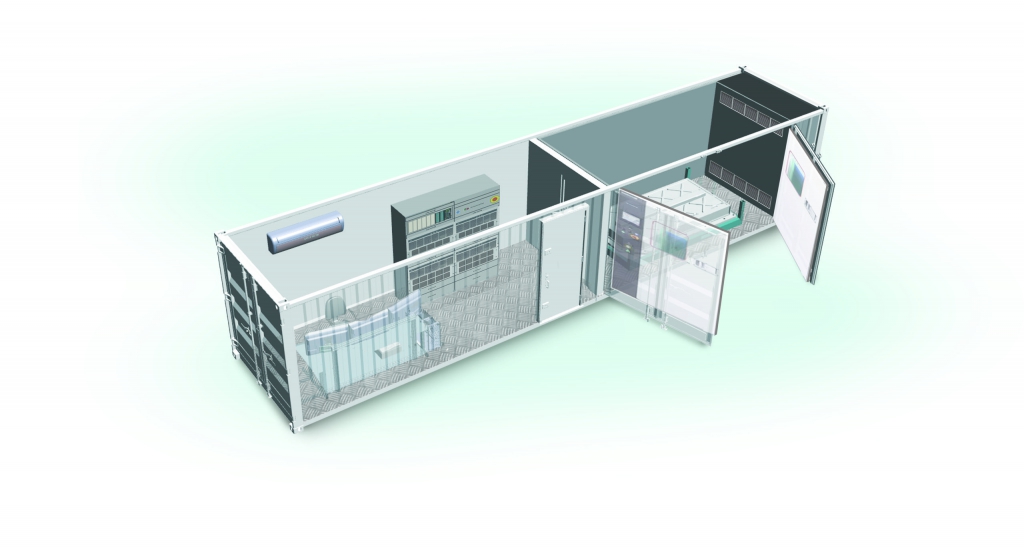
E-Polyhedron: Lotus Engineering
Part of this E-Polyhedron is “Lotus Engineering, who is launching a pilot containerised battery testing facility. The project has been named BattCon, an abbreviation of Battery Containerised Test Facility. The ‘containers’ are individual walk-in laboratories and will be in operation at Lotus HQ in Hethel, Norfolk, as well as the new Lotus Advanced Technology Centre in Wellesbourne, West Midlands. Each is the size of a standard 40ft shipping container and so can easily be packed up and transported as a mobile testing unit, available to Lotus Engineering customers wherever they are. Lotus has three operational units as part of the pilot scheme. Lotus Engineering has a wealth of experience in the design and engineering of EVs and other alternative propulsion powertrains dating back two decades. While many of the programmes remain confidential, the consultancy’s work on the Tesla Roadster (2008-12) is the best-known example. Services available include capacity determination, resistance mapping, current and power mapping, open circuit voltage determination and heat capacity. Lifetime testing is comprised of low-voltage cycling, high-voltage cycling, self-discharge determination, storage ageing, cycle ageing, drive cycle ageing and orientation. One of the three Lotus containers features an ambient chamber, the temperature of which can be raised or lowered to replicate climatic extremes around the world. The pilot project will conclude in spring 2021 and is co-funded by the Automotive Transformation Fund (ATF), part of the Advanced Propulsion Centre (APC); Innovate UK, part of UK Research and Innovation; the UK Government’s Department for Business, Energy and Industrial Strategy (BEIS) and the Department for International Trade (DIT).”
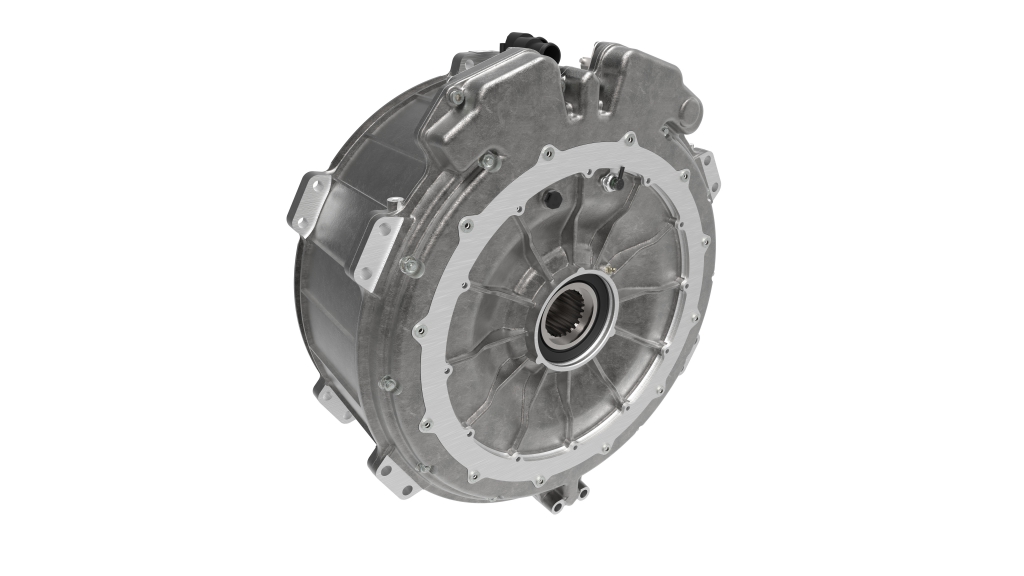
The Equipmake contribute to commercial vehicle’s electric drivetrain
E-Polyhedron remains in UK, the place is still Norfolk, where Equipmake is based and has launched an all-new high torque electric motor designed specifically for use in heavy duty commercial vehicles. “Called the HTM 3500, the new motor combines high torque with low motor speeds, fitting directly onto the propshaft of a large electric vehicle, negating the need for a separate gearbox. Capable of producing maximum torque of 3,500Nm at just 1,000rpm, it has been designed for multiple heavy duty vehicle applications, from electric buses to HGVs and mining trucks, where high torque and start/stop duty cycles are required. The company has developed its own retrofit electric bus chassis – known as EBus – which allows any bus coachbuilder to become a full electric bus manufacturer almost overnight. Equipmake’s new HTM 3500 motor is an integral part of the very latest iteration of the state-of-the-art EBus platform, with in-service trials of this technology beginning next Spring by Brazilian commercial vehicle manufacturer, Agrale, who will launch an electric bus first in Buenos Aires, Argentina in 2021.”
ABB for mining
We’re going to end with a figurative fireworks. ABB, the name is enough to guess the specific weight in electrification processes. In this case focused ‘underground’. “Devised by LKAB, the Sustainable Underground Mining (SUM) project has the goal of setting a new world standard for sustainable mining at great depths in partnership with ABB, Combitech, Epiroc and Sandvik. The framework outlines ambitions for zero carbon dioxide emissions, completely safe mines for humans, productivity increases of 50 per cent and deeper mining. ABB will continue to contribute its deep knowledge in electrification, automation and workplaces together with other suppliers to the mining industry. The collaboration aims to find new methods and smarter solutions for mining operations in the future. Test work in LKAB’s Kiruna mine, northern Sweden, as well as a virtual test mine will study the best way to build a carbon dioxide free and autonomous production system. Within the mine, the Konsuln orebody is used to demonstrate future workplaces in a decentralized environment with efficient use of an autonomous electrical mobile transport system in a mixed environment. Real time process information is available to all organizations involved. When combined with the wider efforts of the SUM partnership, this shows a way of bringing completely new technology solutions to market for safer, more sustainable and more efficient mining production processes.”