Improving the fuel efficiency of an internal combustion engine (Part II)
It’s pretty sure that fuel efficiency is one of the main factors that trigger the competitiveness of internal combustion engine also in the next years and decades. Hybridization and electrification are major challenges indeed for more traditional engines. Last week we started the publication of a technical article written by Serguei Tikhonenkov, MSc. Here we […]
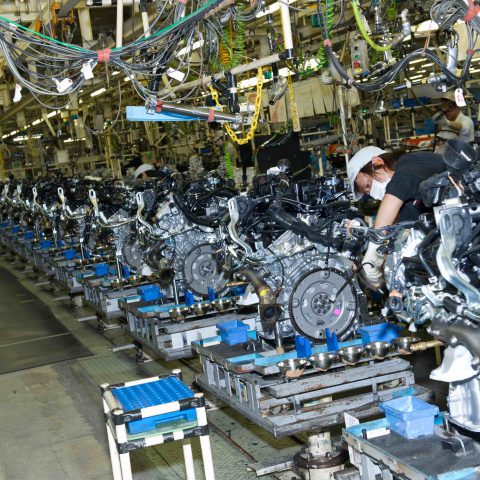
It’s pretty sure that fuel efficiency is one of the main factors that trigger the competitiveness of internal combustion engine also in the next years and decades. Hybridization and electrification are major challenges indeed for more traditional engines. Last week we started the publication of a technical article written by Serguei Tikhonenkov, MSc. Here we publish the second part of the article.
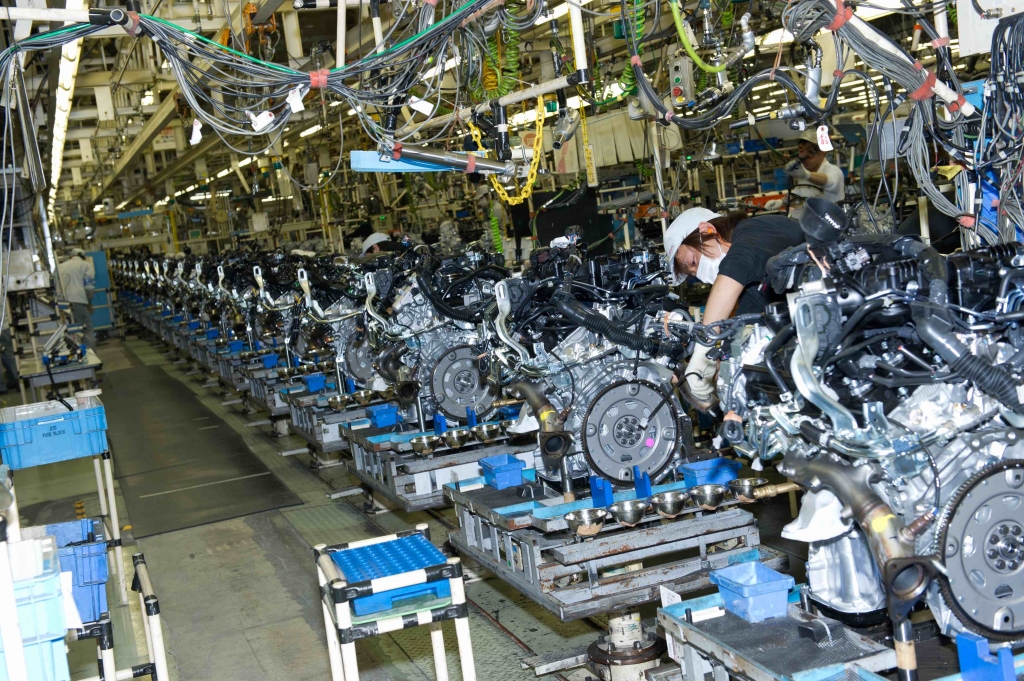
Fuel efficiency: the matter of unburned fuel
An internal combustion engine uses, at best, 75% of the fuel, while 25% of the unburned fuel escapes through the exhaust pipe, the catalytic converter and the muffler into the atmosphere. The unburned fuel is burned up in the catalytic converter. A catalytic converter is a fairly expensive device. Its dense honeycomb takes away a part of the engine power. Several reasons for incomplete combustion of fuel are noted, and one of them is the very short time of the fuel-air mixture combustion process. The average time of combustion of the fuel-air mixture in the cylinder is 0.003-0.005 seconds. This means that the length of the piston’s travel determines how completely the mixture burns up, and the length of the piston’s travel is determined and limited by the size of the crankshaft.
ALL-PLASTIC FUEL VAPOR PUMP IMPROVES ENGINE EFFICIENCY
The shortness of the burned mixture’s exhaust time has a significant effect on fuel efficiency as it leads to the mixing of a fresh portion of the fuel-air mixture with unburned residues. This factor reduces engine power.
The compressed mixture is ignited when the piston is at TDC. It is known that high temperature and high pressure are necessary for the complete and effective combustion of the air-fuel mixture. This condition is violated in traditional engines. After passing the TDC, the piston goes down. The space above the piston increases, and the pressure and temperature decrease, and the fuel-air mixture does not burn up completely.
Two videos show the new engine:
In the next post, we’ll show the difference between a traditional engine and the version without crankshaft.
(To be continued…)
srgtikhonenkov@gmail.com