Miretti: all about explosion proof
Miretti is approaching half a century of life (the company was founded in 1973), an important name in the anti-emission device market. In particular, Miretti is associated above all with explosion-proof systems. One application, in particular, is the main one at the Limbiate site, about twenty kilometers from Milan, in northern Italy: handling. The protagonists […]
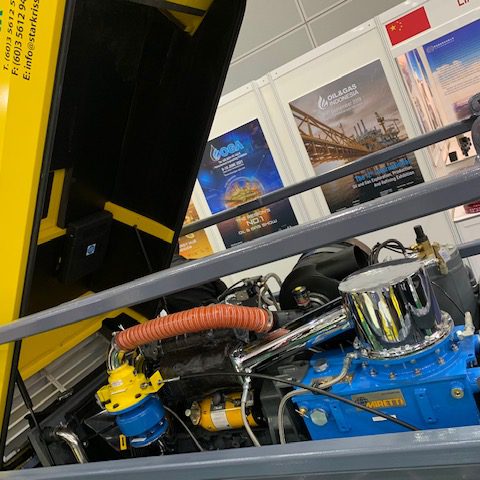
Miretti is approaching half a century of life (the company was founded in 1973), an important name in the anti-emission device market. In particular, Miretti is associated above all with explosion-proof systems. One application, in particular, is the main one at the Limbiate site, about twenty kilometers from Milan, in northern Italy: handling. The protagonists are, in particular, the front lifts, the lift trucks, the earth-moving machines and stationary systems. Miretti concentrates on any machinery in potentially explosive environments (mines, tunnels, oil rigs, etc.). So endothermic engines, even more so if Tier IV Final and Stage V, are very familiar with Miretti’s solutions. ATEX standards, and more. What are we talking about, specifically? We asked Matteo Stefanini, Global sales and marketing Director.
Stefanini explained to us: «The classic ATEX application refers to the storage and/or handling of dangerous raw materials or finished products that become dangerous during and after processing. In surface industries, the typical example of an explosion-proof machine is the lift truck, which can be classified based on flow rate, work cycle and power supply (diesel, petrol/LPG or hybrid). We are currently seeing an upward trend in heavy duty electric trucks».
What kind of approach do you take based on the different types of emissions?
The SCR is also a source of heat, such as exhaust gases and regeneration. Suffice it to say that certain powders (and gases) ignite at just 200 °C…
Any mechanism that can cause a fire must be protected, based on the various reference directives (ATEX, IECEx, CNEx, NEC). Each country has its own rules to follow. Among our interventions, we proceed to the insulation of hot surfaces, to the cooling of exhaust gases, to the encapsulation of components such as alternator and starter motors, to the antistatic treatment of alternator or fan belts – because the rubbing can trigger an electrostatic charge – and the adaptation of the intake valves to avoid over-speed.
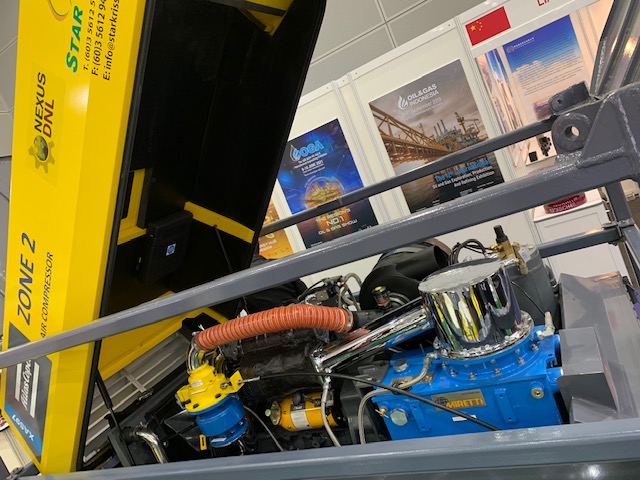
Some special applications?
In the United States (note: Miretti has a manufacturing plant in New Jersey, in addition to Limbiate, Shanghai and Singapore) we found an opportunity in the tank barges, which pump and transport gas from the Gulf of Mexico to the mainland.
Do you have any usage, architecture or injection restrictions?
Absolutely not. We have recently transformed Fpt and Cummins units and operate with any engine. Some examples: Caterpillar, Atlas Copco, Volvo, Deutz, Perkins, MTU, John Deere, JCB, etc… We are independent and this is what makes us unique. Although we have pre-assembled packages, we offer 100 percent customized solutions. We work on behalf of the client in compliance with the directives required by current legislation and the instructions of the customer.
What are the operational constraints?
In some cases the ATEX transformation is not practicable or is not advisable. Diesel, for example, cannot operate at a temperature below T4 (135 ° C), to avoid penalizing performance. Space is another issue: if you think about an open skid there is room for maneuver, if the engine is instead allocated in a small container, the problems increase.
For example, the DNV institution sets some structural limits such as the provision of four anchor points for lifting the skid, forcing us to respect the original shape and thus preventing us from positioning the exchanger, muffler or other. We always request the final approval of the project by the customer, with whom we establish a continuous exchange of information for a constructive collaboration.
ATEX standards. What transformations do you bring to the engine?
We can talk about the interventions on the entry line and the discharge line. The diesel cycle generates high temperatures on the exhaust and turbo manifold, which make the mechanical parts incandescent.
For marine engines, the transformation is simplified due to the water cooling of the exhaust manifolds and the turbine. On the exhaust line the gases are cooled by the exchanger, respecting the parameters set by the customer (usually it is T3 – 200 °C). The exchanger is the Miretti FilterEx: a patented and certified system that contains in a single component the flame-retardant (self cleaning) based on catalytic technology, the gas cooler and the spark-shut-off.
How to prevent the engine from sucking gas-filled air? We introduce a shut-down valve between the engine and the suction line that interrupts the air flow up to the extreme ratio of the engine shutdown. The alarm is triggered early and the throttle is activated long before the breaking point. The control system also closes the supply valve.
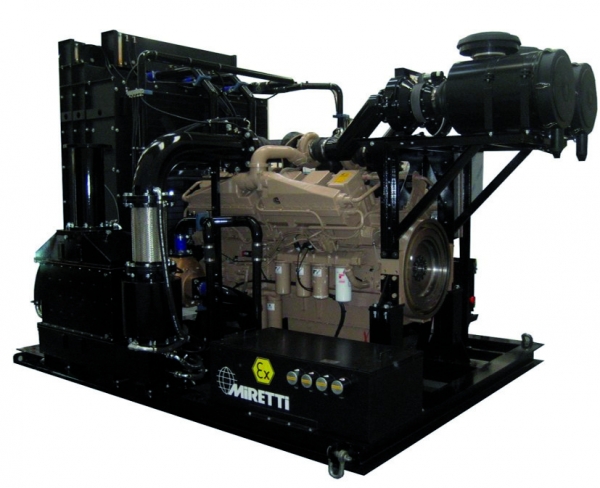
A difference between you and your competitors?
Among others, the allocation of the flame stop: others place it at the exit of the heat exchanger, in contact with cold gases; Miretti, on the other hand, positions it before the exchanger, in contact with the gases coming from the turbine that are very hot (even above 400 °C). In the first case, the unburned particles of the already cooled exhaust gases adhere more to the surfaces of the flame arrestor. This does not happen with us, thanks to the different positioning of this component. Furthermore, another difference concerns the superior maintenance interval, which Miretti sets at 1,000 hours.
In conclusion?
Miretti has been working in the mining sector for decades. Contexts such as oil platforms represent an emergency that, despite having always existed, has gained popularity in the last period (for example in the case of Deep water horizon). Miretti actively participates in various working groups that deal with the drafting of the new European and North American standards.
Specifically: technical committee of the CEI CT31-Explosion-proof Materials; “Project Team PT80079-41” which is working on the drafting of the new international standard for internal combustion engines; American committee NFPA Industrial Trucks. A final note on the service: the technicians are trained to intervene on any vehicle, engine or platform. We are an Italian company but with an international vision and a global anti-explosion approach. This allows us to follow customers all over the world.