MTU and its full coverage assistance
Digitization and loyalty are key features, according to MTU MTU. The new Customer Care Center in Friedrichshafen is another milestone for Rolls-Royce Power Systems customers. This is the declaration that the CEO Andreas Schell made during the inauguration ceremony of the new plant. In general, the new Customer Support Centers are part of Rolls-Royce Power Systems‘ […]
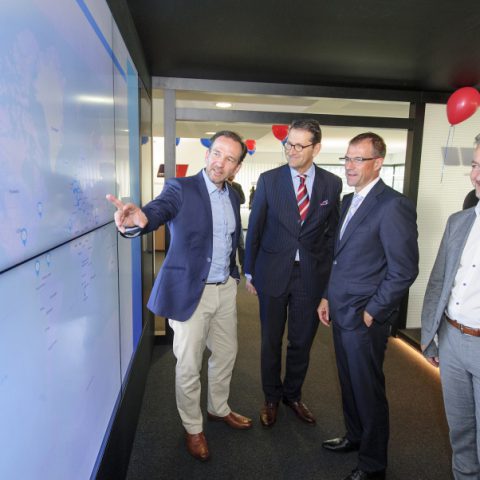
Digitization and loyalty are key features, according to MTU
MTU. The new Customer Care Center in Friedrichshafen is another milestone for Rolls-Royce Power Systems customers. This is the declaration that the CEO Andreas Schell made during the inauguration ceremony of the new plant.
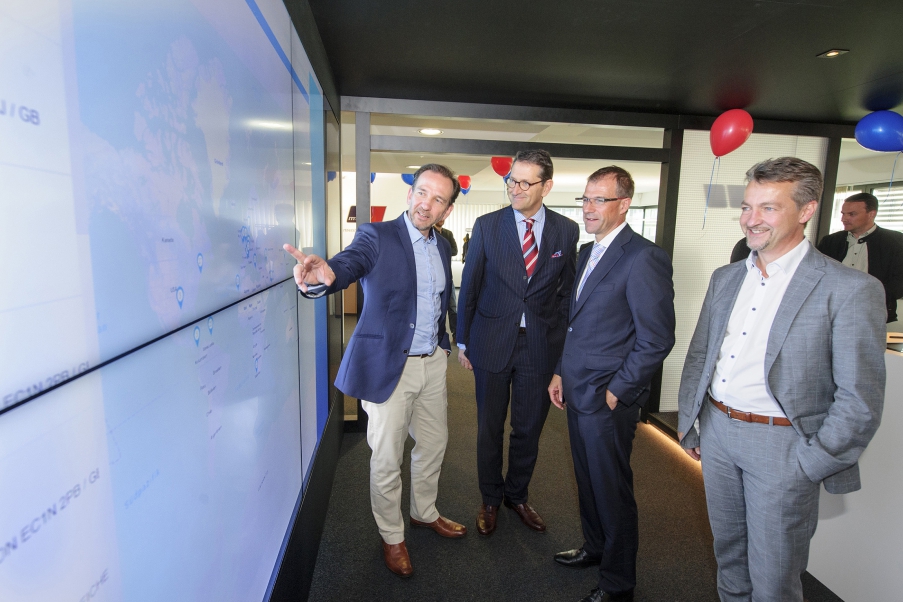
In general, the new Customer Support Centers are part of Rolls-Royce Power Systems‘ plan to transform and digitize their customer service. Since January, there are three locations where the MTU technicians provide 24-hour assistance. Singapore, Novi, and Friedrichshafen.
«With our service and digital strategy, we intend to deliver an exceptionally high customer-focused improvement in both our services and products», Andreas Schell explained. «The aim of our transformation is to support our customers as a complete solutions provider».
Digitalization is leading the transformation process
Rolls-Royce Power Systems has an in-house team of over 40 people involved in driving the transformation. In addition, external experts, start-up service providers, and app developers contribute with their expertize. «We are developing digital products and services that will generate substantial benefits for the customer», said Jürgen Winterholler, head of the digital solutions department. «We are doing it in the style of a start-up, fast, agile and with a close proximity to the customer. With the methods we use, such as design thinking, we make sure we know exactly what the customer needs».
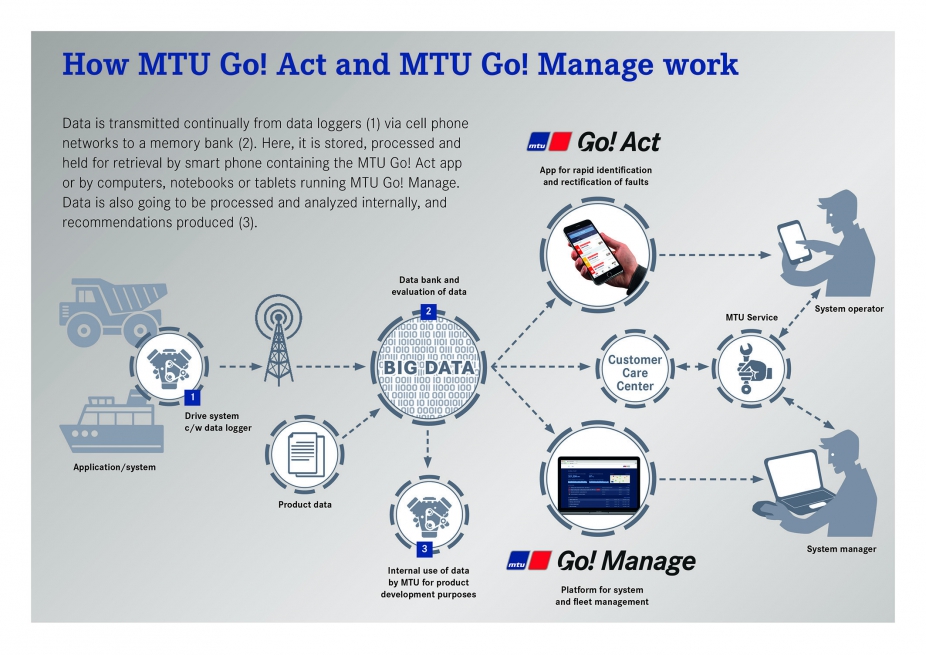
«They provide the communications between the operator, service personnel and experts. They collect the information at one location and help the customer and our organization to optimize the use and operation of our products. In all these considerations, cybersecurity and data protection have been assigned the highest priority. This is an area where we also benefit from the experience gained in the course of the last 20 years by Rolls-Royce in the aerospace industry».
Mtu Value Care, a complete package
Matthias Vogel, Executive Vice President Service, Network and Business Development at Rolls-Royce Power Systems shared his perspective. «As a result of the interplay between our new service agreements, new digital tools, and the Customer Care Centers, the customer is provided with a complete peace-of-mind package. The customers benefit in terms of reliability, operational efficiency and maximum service life for their propulsion or energy system. We assume the risks so that the customer can concentrate on their own core business».
The elaboration of the agreements is also an integral part of the new Customer Care Center in Friedrichshafen, where experts work side-by-side with the digital team. Preventive maintenance, with coordinated maintenance intervals, will be essential to ensure that everything runs smoothly.
MTU Go! Act and MTU Go! Manage, an extra tool for better support
These new digital tools represent the extra gear for the analysis of connected systems. MTU Go! Act notifies customers of any errors that may have occurred via smartphone. It also allows them to quickly identify and eliminate the error. Customers can share fault details with a specific supervisor or team. Instead, MTU Go! Manage is a platform that connects a customer’s system to Rolls-Royce Power Systems. This significantly improves communication with MTU partners, distributors, and the Customer Support Center. The operation and status of the connected equipment are continuously monitored and displayed. In this way, the operator and maintenance and assistance experts can react quickly in case of irregularities.
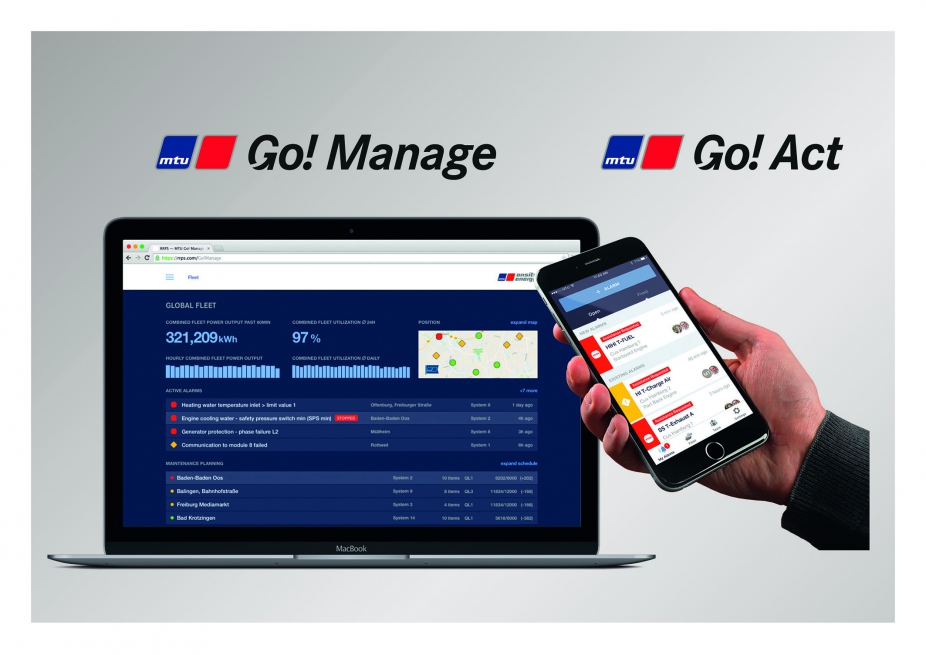