Tenneco Low Emissions brake
Tenneco Introduces Low Emission Brake Technology for Light and Commercial Vehicles
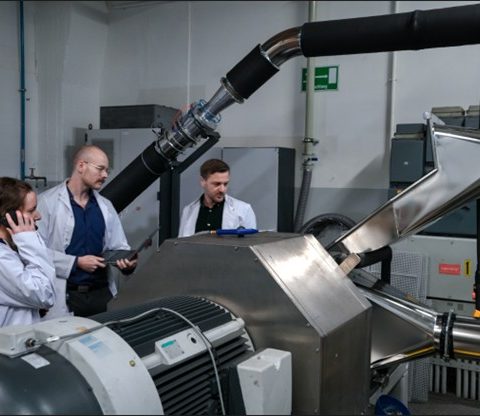
Tenneco is well aware that brake (together with the tyres) are responsible for a significant share of automotive pollution, regardless of whether a combustion or zero-emission propulsion system is used. The company has introduced a Low Emission Brake technology that is helping vehicle manufacturers and Tier One suppliers prepare for and meet the upcoming Euro 7 and China 7 brake emissions standards. The new technology enables Tenneco to utilize a variety of renewable and recycled materials and reduce C02 emissions associated with the manufacture of brake pads.
Brake for China 7 and Euro 7 according to Tenneco vision
From 2026, Euro 7 regulations will set strict limits on brake particulate emissions: 3 mg/km for pure electric vehicles (PEVs) and 7 mg/km for hybrids and ICE-powered vehicles. Heavy vans (N1 Class III) face limits of 5 mg/km for PEVs and 11 mg/km for other powertrains. Similarly, China’s upcoming China 7 standard, expected by the end of 2025, will introduce comparable limits focused on PM2.5 emissions. Tenneco’s Low Emission Brake technology uses natural materials, minerals, and recycled raw materials to significantly reduce PM emissions while meeting vehicle-specific braking requirements. In some cases, the pads could last nearly the lifetime of the vehicle. Since 2017, Tenneco has been actively involved in the Particulate Measurement Program of the European Commission’s Joint Research Centre, helping define measurement standards and participating in interlaboratory studies.
With an established customer base among leading Chinese OEMs, Tenneco is preparing for China 7 by investing in advanced emissions testing facilities and integrating AI and virtual simulation tools to accelerate product development and validation. Tenneco supplies brake pads and other products to a majority of Chinese light and commercial vehicle OEMs, including Chery-Huawei, GAC Motor, Geely, FAW, Great Wall Motor, JAC-Huawei, SAIC Motor, and XPeng Motors.
The Low Emission Brake program also contributes to production sustainability, cutting manufacturing-related CO₂ emissions by 15–35% through the use of renewable and recycled materials, with further reductions targeted through new manufacturing processes.
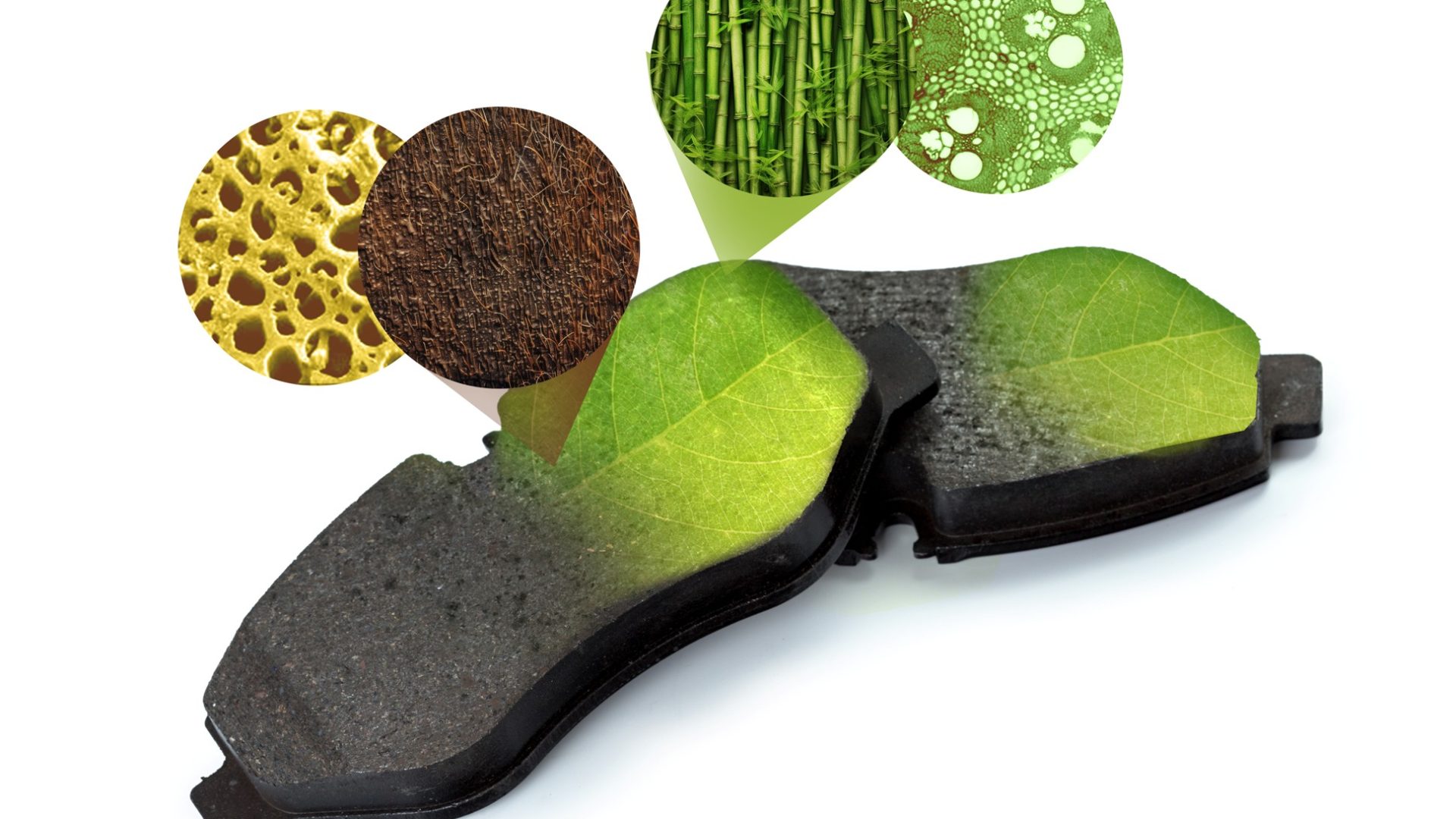
Schlauss and Frecchio
“Preparation for Euro 7 and China 7 has required a paradigm shift in virtually every area of brake pad and disc development and manufacture as well as significant investments in next-generation research, development and testing resources,” said Holger Schlauss, VP of Global Engineering, Tenneco OE Braking. “Our global team has been able to leverage our unique expertise in materials science, chemical and physical analysis, and advanced analytics to meet these new requirements on behalf of vehicle OEMs and Tier One suppliers.”
“As China’s OEMs finalize plans for their 2026 and later models, we are well prepared to meet the corresponding demand for Low Emission Brake pads that are precisely matched to each model,” said Marco Frecchio, Business Development and Supply Chain Senior Director, Tenneco OE Braking.