Vanzetti Engineering. LNG, pumps and sea
Vanzetti Engineering has established itself as an LNG specialist. Also at sea. Below we publish an extensive excerpt of the interview that you can find HERE. Being essential to have cryogenic fluids at very low temperatures and transfer the fluids from one tank to another, cryogenic pumps are also widespread in the marine field. We […]
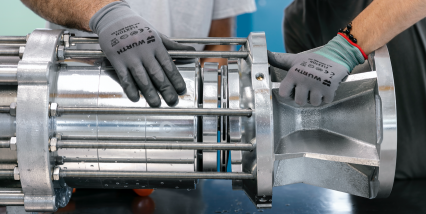
Vanzetti Engineering has established itself as an LNG specialist. Also at sea. Below we publish an extensive excerpt of the interview that you can find HERE.
Being essential to have cryogenic fluids at very low temperatures and transfer the fluids from one tank to another, cryogenic pumps are also widespread in the marine field. We talked about it with Giancarlo Geninatti, Lng Marine Sales Manager at Vanzetti Engineering.
What are the Vanzetti Engineering main types of cryogenic pumps in the marine field?
The cryogenic centrifugal pumps for marine applications are always submersibles: this means that the engine is submerged in the LNG. Compared to the industrial ones, then, there is an important difference also in pump types. Besides the centrifugal ones, there are also reciprocating cryogenic pumps.
What about applications instead?
There are basically two applications. One is the pump used to feed liquid methane to the ship engine. The second one is that of so-called cargo pumps, which are used to move the methane from the tank of a ship to the tank of another ship or rather to a liquid methane tank on ground. In the marine sector, as mentioned, the other family is that of reciprocating pumps, suitable for engines that need very high pressure, up to 350 bars.
Let’s talk in more detail about products. How does the Artika 120-3S differ from stationary application pumps?
The Artika 120-3S is the smallest pump in the Vanzetti Engineering Artika range and is mainly used in the marine field. The big difference, as far as marine industry is concerned, is the class certification; Vanzetti Engineering has got experience with virtually all marine certification bodies. To be certified all materials must come from certified production chains, from steel to aluminum alloy up to the individual parts of the pump. Once mounted, the pump have to be thoroughly tested in order to be compliant with some quite strict standards. The whole quality control is therefore much more expensive, also affecting the cost of products.