Hydac. Driving safely and agriculture 4.0
Hydac solution for comfort and safety of agricultural machine drivers Hydac smart hydropneumatic suspensions and steer by wire systems answer to the recent regulatory and market demands for safety and operator comfort, while keeping an eye on the most innovative autonomous driving systems. The company developed these systems in cooperation with different manufacturers, in order to […]
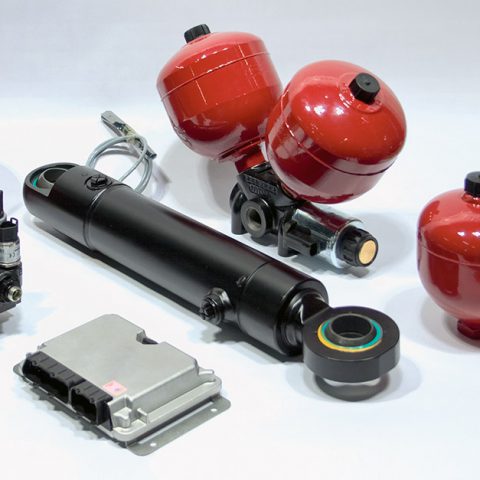
Hydac solution for comfort and safety of agricultural machine drivers
Hydac smart hydropneumatic suspensions and steer by wire systems answer to the recent regulatory and market demands for safety and operator comfort, while keeping an eye on the most innovative autonomous driving systems. The company developed these systems in cooperation with different manufacturers, in order to realize fully calibrated and optimized solutions based on the machine specifications.
Hydac suspension systems for the cab and axles, thanks to the integration of hydraulics, sensors and software, ensure the stability of the vehicle in different working conditions. They also contribute to the reduction of noise and vibrations, they guarantee a perfect set-up and reach higher speeds even on the road. The integration of hi-tech sensors and Gps technology to steer by wire electronic steering systems represents Hydac’s contribution to autonomous driving: it allows the operator to know exactly the location of the vehicle and to plan an automatic operational sequence.
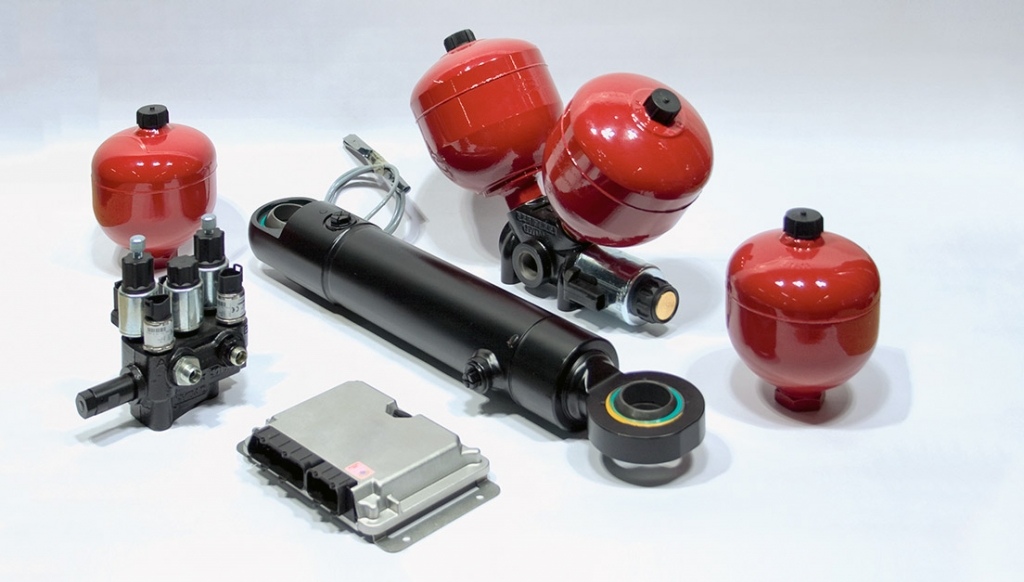
Agriculture 4.0 and smart farming
Smart farming requires the development of interconnected mechatronic systems. Hydac divides its smart farming offer into three types of solutions: measurement, control and interconnection and cloud. The contribution of TTControl, a company created by the joint venture with TT-Tech, was fundamental during the development process.
The first type of solution includes sensors that monitor system values and display interfaces such as the HY-eVision. The second type of solution includes control boards with decentralized architecture and full-duplex communication for the control and interconnection of the systems. The entire control of the vehicle is entrusted to electronic control units (Ecu, Hy-Ttc) constantly updated to be more and more performing.
The various units are connected to each other via the Can (Can-bus) protocol. For the collection of all signals and communication between the individual units, the solution is TTConnect 616.
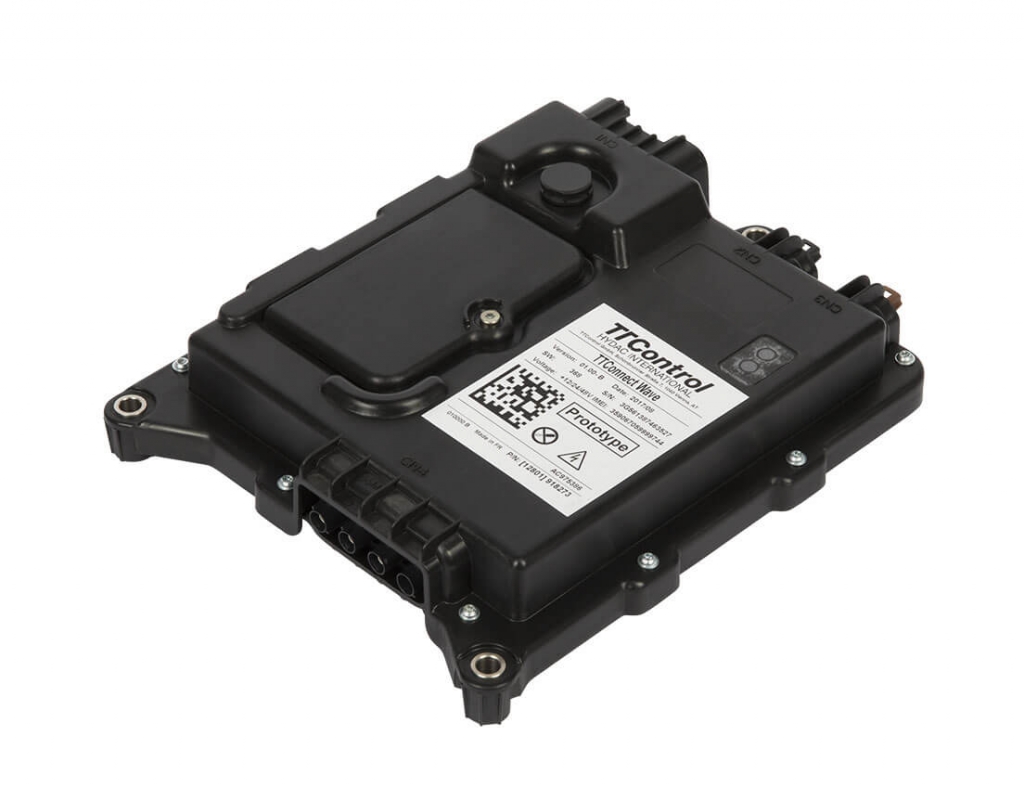
The TTConnect 616
It is a gateway with different interfaces, Can, Lin and FlexRay, and an Ethernet switch for different technologies such as cameras and, in general, for systems implementing Tsn (Time Sensitive Networking) protocols.
The BroadR-Reach physical layer provides full-duplex communication with bitrates of 100 Mbps. Thus, the TTConnect 616 becomes the “backbone” of the entire system, the component inside which all the electrical signals from the individual control units travel: from the operator panels (Hmi), to the cameras.
The data transmission speed simplifies and supports the management of large amounts of data essential for autonomous driving. Connecting the machine to the cloud and managing the data can be done easily thanks to the installation of a TTConnectWave interface that allows the user to connect the machine to the cloud via wireless or using a 3G or 4G mobile network.
TTConnectWave continuously transfers the measured values, the status of the machine and of its components to the TTConnect Cloud Service. In this way it is possible to access data from any authorized device, also in order to implement a predictive and prognostic maintenance of the system. The unit is integrated with a Gps module, to provide information on the position of the vehicle in real time and anywhere. This clears the path for rental of agricultural machinery and precision farming.