ABB Mobile E-Power for the electrification of the mining sector
The electrification of heavy-duty vehicles plays a crucial role in the fight against climate change and is one of the cornerstones of ABB's offering, as demonstrated by the recent creation of the dedicated Mobile E-Power business.
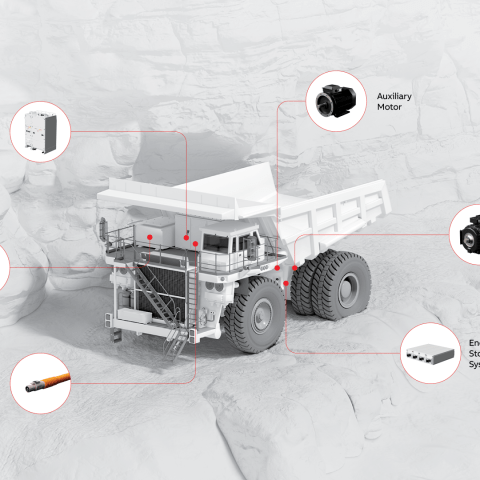
For some time now at the forefront of the fight against climate change with the Energy Efficiency Movement initiative, ABB offers solutions for energy efficiency in the most varied industrial sectors and, in particular, for the electrification of all types of vehicles, with a package that covers a wide range of powers. With the recent creation of the Mobile E-Power business, ABB has intensified its focus on the electrification of heavy-duty vehicles, including those used in the mining sector. The product portfolio includes motors, frequency converters, mobile controllers and energy storage systems, along with charging technologies designed by ABB specifically for mining, construction, material handling, public transport, maritime and rail.
The advantages of ABB’s proposal
The energy transition in the mining sector is driven, among others, by the International Council on Mining and Metals (ICMM), which has set the goal of net-zero greenhouse gas (GHG) emissions by 2050. ABB’s contribution takes the form of numerous partnerships with OEMs and System Integrators which, exploiting the experience of the Swiss-Scandinavian company in the innovation of sustainable transport solutions, aim to create complete electric powertrains for vehicles and machinery for heavy-duty work in underground and surface mines.
In addition to reducing emissions, fleet electrification promises very real benefits to companies in the mining sector, as well as their operators. It is estimated that by 2030 the total cost of ownership of a battery electric vehicle will be 20% lower than that of current heavy diesel trucks, thanks to 20-30% lower maintenance costs and a reduction in costs between 40 and 60%. The benefits from the point of view of the health and safety of operators are equally significant: vehicles without exhaust emissions reduce the need for underground ventilation and, consequently, reduce the risks associated with inhaling toxic fumes.
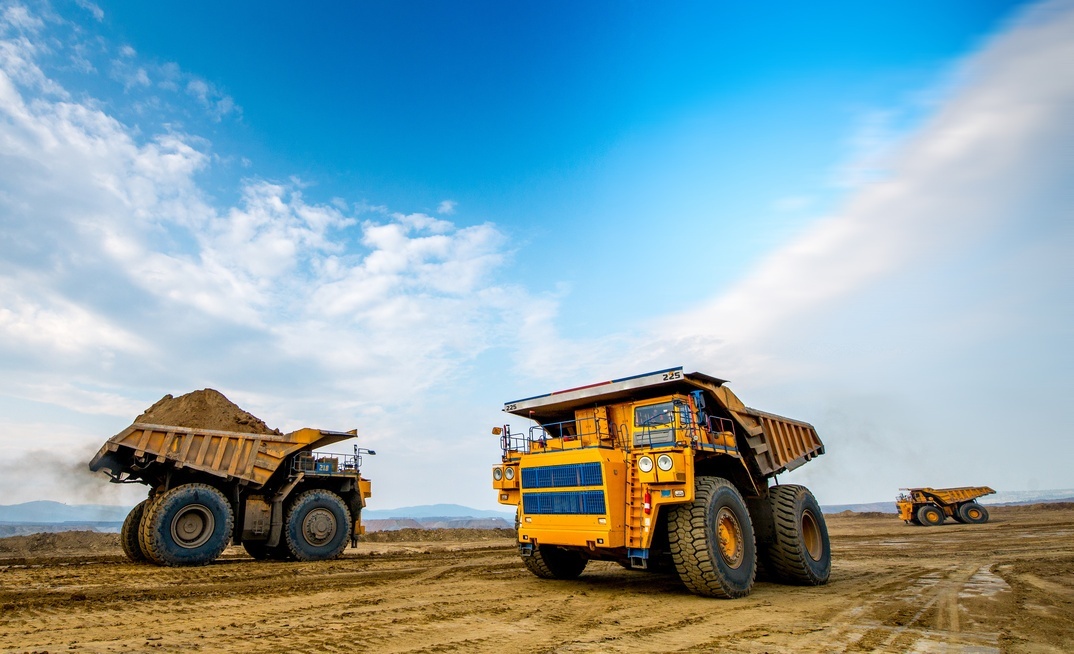
The transition comes from retrofitting
Over the next decade, to meet the growing demand for essential minerals such as graphite, lithium, nickel and cobalt, necessary for the production of batteries, over 300 new mines are expected to open. With these figures, a total transition to fully electric mining vehicles and equipment is impractical in the short term and companies will need effective solutions to continue using the huge fleet of existing vehicles. Hence the great importance that retrofit operations will assume.
ABB has developed a diverse range of electrification and hybridization solutions, suitable both for retrofitting existing systems and for implementation on new projects. These solutions include motors, batteries, inverters, system controllers and charging systems that can extend the life cycle of the machines.
By opting for retrofit, mining operators can not only safeguard investments already made, but also benefit from an extended operational life on the order of one or more decades before major mechanical maintenance is required. Furthermore, compared to traditional diesel options, electric traction offers superior performance and remote monitoring capabilities, combined with greater productivity and environmental sustainability.
ABB will talk about the advantages of retrofitting in a webinar to be held on 5 June, during which some of the financing channels to support companies intending to make the transition to electric will be presented.
The second life of machines: the Nuh Cement case
A significant retrofit intervention is that carried out by Nuh Cement, a Turkish company producing concrete and other construction materials, which, in collaboration with ABB, has started a broad-spectrum project for the electrification of its fleet of construction machinery, using numerous components supplied by ABB: X90 mobile controller, AXME auxiliary motor, Bordline traction platform solution, auxiliary inverter and DC/DC converter, Bordline energy storage system and traction motor. According to general director Halim Tekkeşin, with the first phase of the project (relating to the electrification of excavators working in quarries), the company has already reduced its carbon footprint and saved 2 million liters of diesel, also giving a second life of another 30 years to machines that would otherwise have had to be scrapped with a replacement cost estimated at 15 million dollars.

Read also: ABB and Perenti agree to decarbonize mining operations