Cummins acts big with QSK60
Customers can choose from one of two 2,300hp Stage IV engines; a 16-cylinder Cummins QSK60 or an MTU 16V4000 Detroit Diesel.
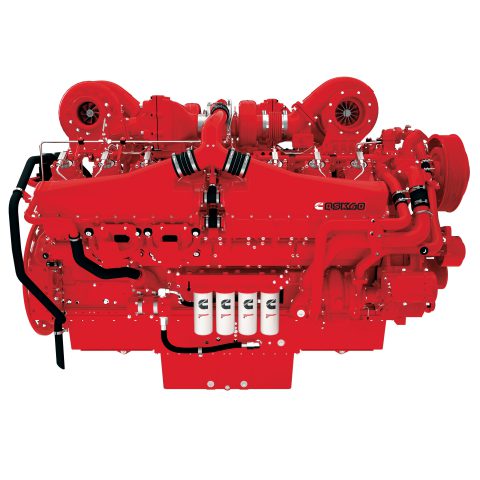
The largest wheel loader in the world, equipped with the Cummins QSK60 or, alternatively, with the Detroit Diesel, aka MTU, 16V4000, is ready to be noticed also in Europe. As we hear from aewsomeearthmovers.com “The P&H L-2350, a 2,300hp behemoth, has arrived in Europe.
Komatsu choose Cummins Qsk60
Premiered by LeTourneau Technologies at the 2000 MINExpo in Las Vegas, it has taken 20 years for the first L-2350 to come to Europe. One of two new P&H L-series wheeled loaders recently commissioned at the Swedish Aitik copper mine, the other is an equally impressive 240-tonne/2,000hp L-1850. The flagships in the four-model Texas-built range, which includes the 1,900hp L-1350 and 1,250hp L-1150, big as the L-1850, the L-2350 is in a league of its own. Available with three configurations of lift arms; standard, high lift and super high lift, even the standard 270-tonne version is listed in the Guinness World Records. Designed for loading coal trucks, the super high lift version hoists its bucket to a lofty height of nearly 16m and is a popular option for loading high-sided coal trucks. The high lift version is plenty sufficient for the Arctic Circle mine, which complete with bucket and tyre chains weighs a tad over 300 tonnes!”
CUMMINS AND THE FUTURE OF DIESEL TECHNOLOGY IN AGRICULTURE
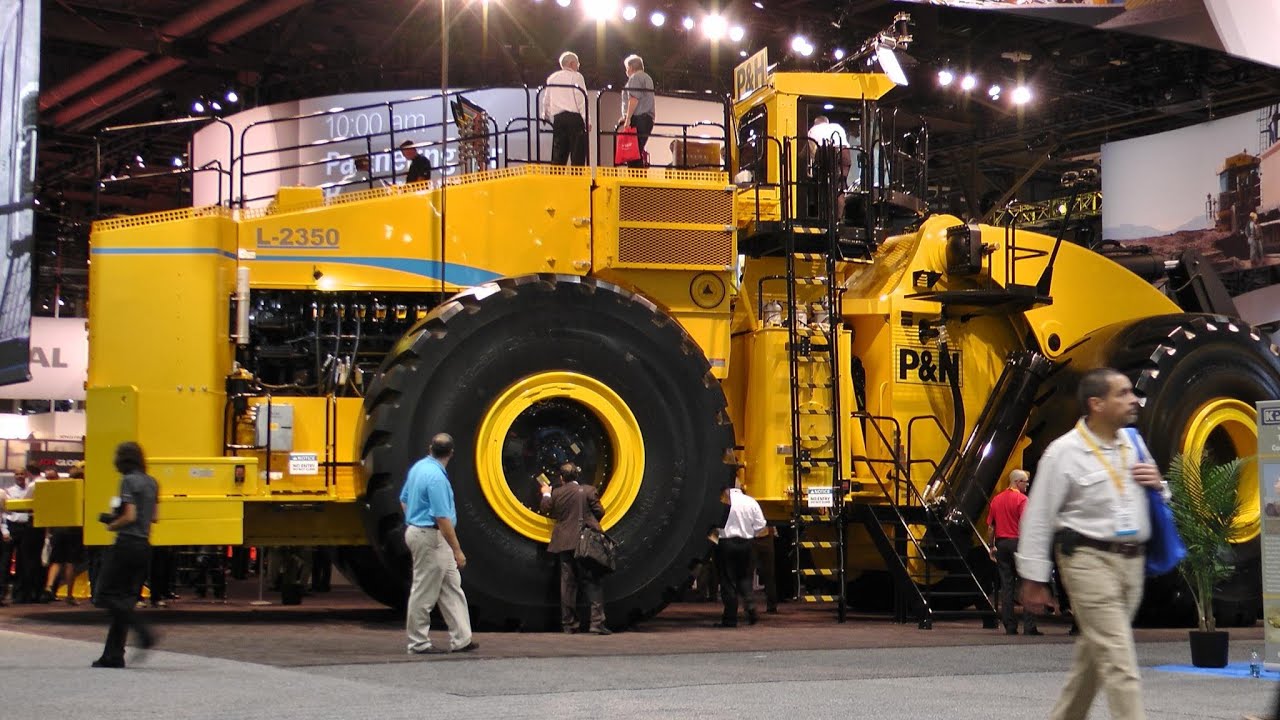
Cummins QSK60 for mining applications
- The 16-cylinder, 60.2 liters-displacement (BxS 159×190 mm), is able to provide UP TO 2125 kW and 11,218 Nm. According to Cummins, a redesigned power cylinder, optimized wastegate turbocharger and improved crankcase breather system work to keep particulate matter (PM) levels low while maintaining durability and reliability. The QSK60 achieves nearly 1.1 million gallons-to-overhaul. Fuel system – The Cummins Modular Common Rail Fuel System (MCRS) uses increased injection pressure and larger injector accumulator volume, for reduced PM and improved fuel economy. The leakless injector has increased fueling precision and timing control, for reduced parasitic losses, reduced fuel heating and improved fuel economy. An improved pilot valve resists wear, for enhanced reliability and durability. The fuel pump has an improved tappet design and fuel cooling of pumping elements, which contribute to longer component life. Air handling – The simplified configuration of the wastegate turbochargers and intercoolers allows access to the top end of the QSK60 without removal of the air-handling system, even on our two-stage engines. Its altitude capacity exceeds the 10,500-ft requirement for Tier 4 Final engines in North America. Lubrication and filtration – NanoNet® filtration captures and retains more harmful particles than traditional media, for longer fuel pump and injector life with better reliability. Oil and fuel filter change intervals have been increased to 500 hours. Selective Catalytic Reduction (SCR) – Cummins modular SCR system features an integrated decomposition chamber and a Cummins airless Diesel Exhaust Fluid (DEF) dosing system designed to last the life of the engine. The use of SCR minimizes engine backpressure, for increased fuel economy. Optimized temperature management minimizes DEF consumption.