Volvo CE works in the mines with Cummins QSK19
Volvo CE turned to Cummins to power the R60 and R70 dump trucks. The engine is the Cummins QSK19, 567 kW at 2,100 rpm
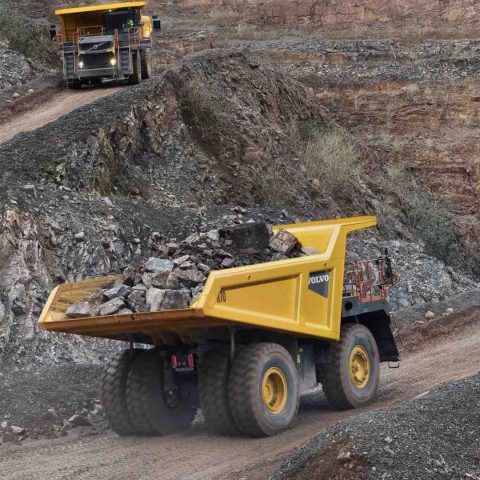
Volvo CE and Cummins QSK19 arm in arm in the sign of dump trucks. The Swedish manufacturer’s range of rigid dump trucks has been expanded with the R60 and R70 models, equipped with Cummins’ 19-liter Diesel engine. An engine that can also extend its life with the help of the European Master Rebuild Centre in Krakow, Poland.
A 19-litre Cummins Diesel engine for the Volvo CE dumpers
A versatile engine, the square Cummins QSK19 (AxC 159 x 159 mm) chosen by Volvo CE. Well-known in the world of power generation and oil and gas, commercial marine applications, as well as traction locomotives and railway maintenance, it is distinguished by several specific features. The modular common rail fuel injection system (MCRS) helps reduce noise and vibration impact on operators. Nanonet technology is at the service of the engine’s life cycle, filtering out impurities that could compromise its functionality, considering the extreme dustiness of the operating environments.
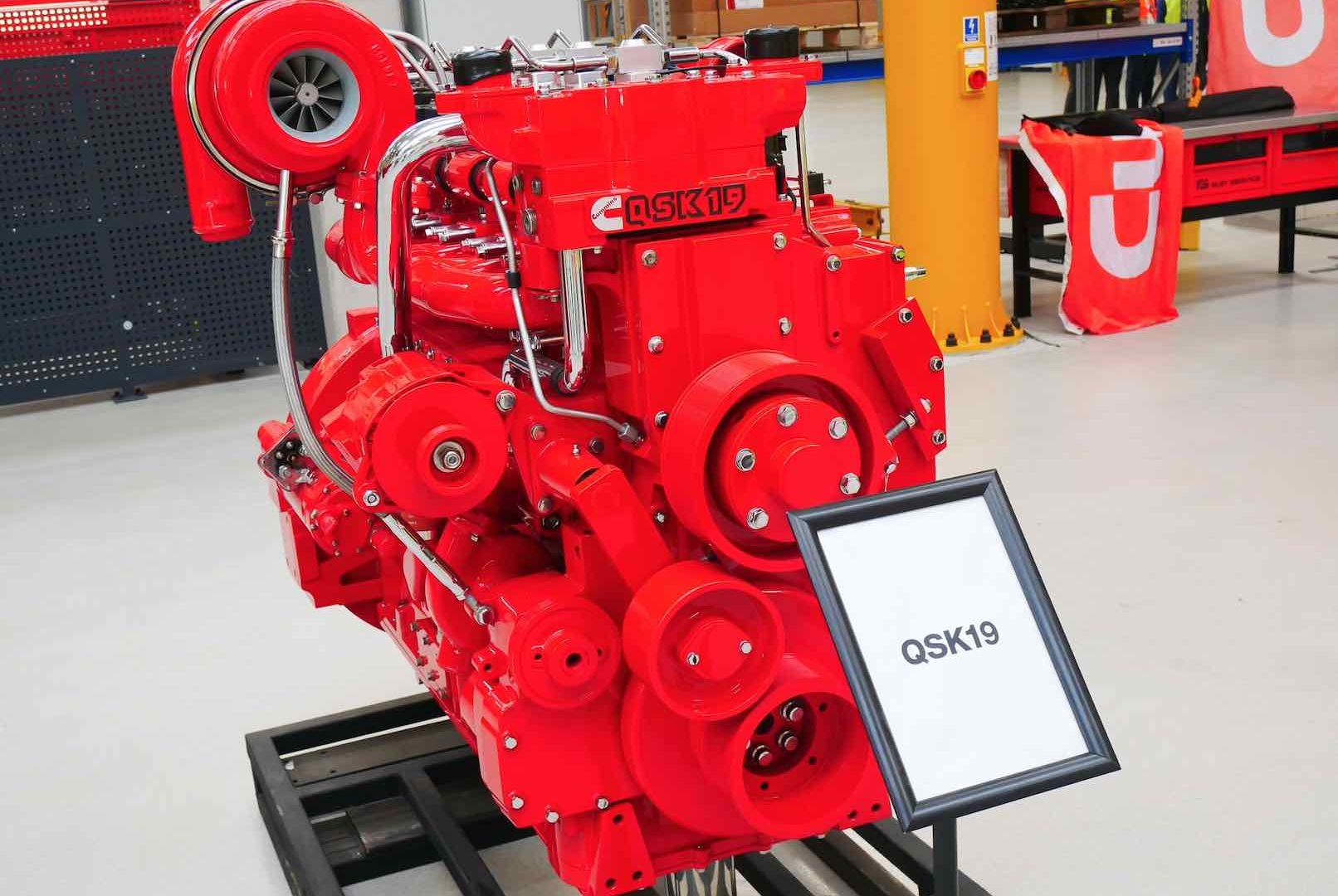
Ladies and gentlemen, the R60 and R70
The container capacities are 36 cubic metres for the smaller R60 and 42 cubic metres for its big brother R70. These are therefore two new machines designed to offer further optimal combination possibilities for those working in quarries and light mining. With an overlap, on the part of the R60, with the articulated A60H with which it shares the exact operating capacity. But obviously with a different application target and a lower TCO. In fact, the choice between a rigid and an articulated dumper, in mining and quarrying sites, depends on several factors. Assessing the specific needs and operating conditions is the first and most important step. Rigid dump trucks are suited to environments with wide, solid, well-maintained haulage roads, where they can travel quickly over long distances. Articulated dump trucks, on the other hand, are better suited to uneven, narrow, slippery and steep haulage roads with short operating cycles.
For maximising production
Like all rigid dump trucks, the R60 and R70 models are built to maximise production. The body has a classic ‘V’ section to ensure load retention and minimal material return after unloading. The unloading process takes place quickly thanks to a rapid tipping system. As an option, it is possible to have an on-board weighing system that facilitates the industry-standard 10/10/20 payload policy. That is, where the machine can withstand an overload of 10% of the time but not exceed 20%. Traction is ensured through adaptive automatic gear selection provided by Volvo Dynamic Shift Control. The engine also has an Eco mode that is set to the most efficient gear. In addition, the automatic engine shutdown at idle reduces wear and consumption. To keep costs down, service intervals have been extended to 500 hours. There are also ground-based tagout systems and service points that are easy to reach with walkways around the machine. There is an on-board diagnostic system while the CareTrack telematics system allows remote monitoring. This allows predictive maintenance by quickly identifying potential faults to intervene with controls before they occur.
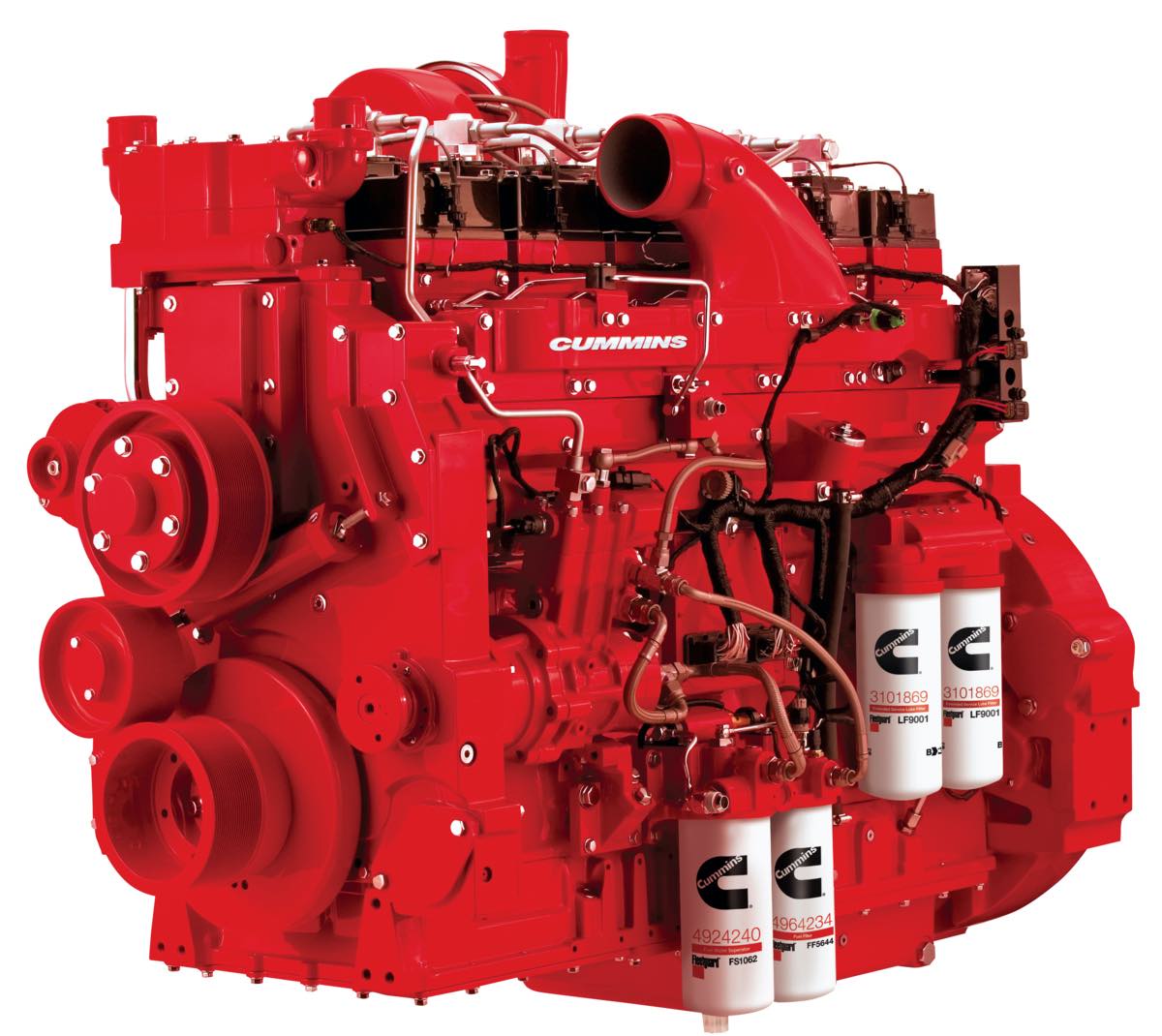