JCB Power Systems: do the right thing
JCB has made a choice: above 5 tonnes there is the H2 ICE. Read the full article in the March issue of Powertrain International
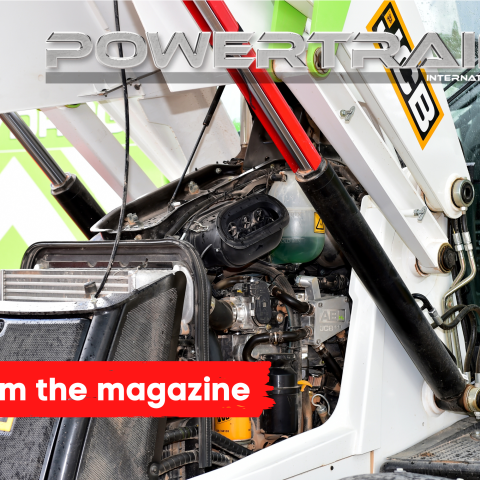
At JCB they have a clear idea: under the 4/5-tonnes threshold there will be room for electrification of compact machines; if you want move up the scale, green light to hydrogen. It is a matter of energy demand and the profile of the machine, whether service or production. Recharge time must be included in the TCO. CO2 production comes mainly from medium-power applications; compact machines only account 5% to CO2.
The electric option is attractive when it does not create too much mass in the vehicle. JCB’s analysis puts cars and mini-excavators, 1.9 tonnes, on an equal footing, for which batteries account for just 15% of the mass. But no Pindaric flights on fuel cells! That technology is not suitable for a dirt-saturated environment like the construction sites. Just imagine servicing such a delicate component in the middle of nowhere.
Moreover, to give you an order of magnitude, the cooling pack is 2.7 times larger than the diesel machine one. And if JCB engineers found traces of soot in the membranes of fuel cells of buses in service in London, what would happen on a building site? A scenario that also applies to the JCB excavator we have seen in the quarry. A similar approach to that of Liebherr, which will probably remain, like the others, on stand-by.
JCB’s strategy advocates the mistreated ICE, in this case the 4.8-litre Ecomax, Diesel of the Year 2011, as the champion of the transition, precisely in the hydrogen version. In the ring of H2 we could say that fuel cell vs ICE represents a clash between a fragile and a robust ecosystem. In the Wardlow quarry near the HQ, a backhoe loader and a telescopic handler showed themselves to us in “hydrogenated” translation.
It was to all intents and purposes a 1:1 replacement, i.e. without changing the design, a formula that can also be applied on other models, with the only caveat being the hydrogen tank housing. Same engine block, maximum scalability of the sub-components (one of the objectives of British engineering is the interchangeability of both the machinery, with a simultaneous manufacturing for diesel and hydrogen) and a revision of the processes related to air compression, spark ignition, steam management, pressures and thermal delta.
Hydrogen is known to have a “ill-tempered character”, but research into the management of this fuel has made great strides. Hydrogen needs maximum expansion to harmonise combustion process. For this reason, the injection angle has been investigated in detail. The production of steam, which must be monitored and processed, clearly cannot be ignored. It is no coincidence that the spark plugs are made of stainless steel.
JCB’s chairman, Lord Bamford, said: “The unique combustion properties of hydrogen enable the hydrogen engine to deliver the same power, the same torque and the same efficiency that power JCB machines today, but in a zero-carbon way. Hydrogen combustion engines also offer other significant benefits”.
We mentioned the parallelism between passenger cars and mini-excavators, for which the battery pack makes sense. Changing the scenario, imagining a tractor working 16 hours a day, it would require around 200 battery packs, so up to 10 tonnes more and a price range 4.3 times higher. For agricultural machinery, the figure becomes competitive with a work cycle of just 4 hours per day, which is not credible during sowing, harvesting and seasonal peaks. The work cycle of a skid steer loader allows long stand-by times to recharge.
Think instead of a backhoe loader, on any Indian construction site, without resorting a 36 tonnes excavator: with 3,000 to 4,000 hours of operation, when and how to recharge? After all, there is an obvious job-site limit, the connection to the grid. Speaking of job-site limit, JCB has come up with a mobile refuelling bowser to take the fuel to the machines. The bowser has enough hydrogen to fill 16 hydrogen backhoe loaders and can be transported on any vehicle. With a capacity of 1 kg/min, refuelling times become compatible with the requirements of users: mobile fuel and maximum uptime. In Wardlow the refueller was in tow of a Fastrac tractor, another application that could convert to hydrogen. The challenge was met by the 4.8 litre. There is a JCB 7.2-litre 6-cylinder stopped at Stage 2. Could this be the opportunity for the final breakthrough?
READ THE FULL ARTICLE HERE OR DOWNLOAD THE PDF