Mammoet’s electric-powered SPMTs make successful debut at ITER
Mammoet’s new electric battery-powered Self-Propelled Modular Transporters (SPMTs) have begun operation at the international nuclear fusion research facility ITER in southern France. The equipment is being used to transport heavy components for the construction of the world’s largest tokamak, a device used to prove the feasibility of fusion as a large-scale source of carbon-free energy.
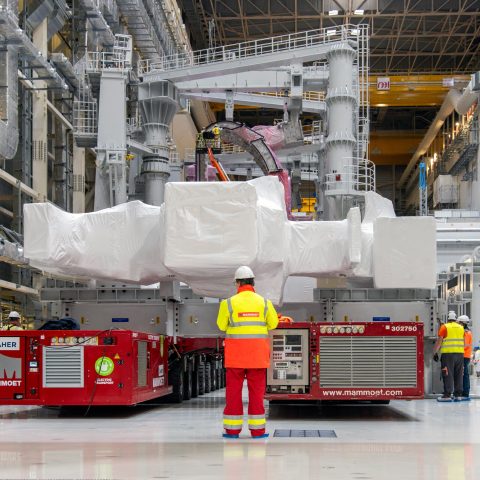
Mammoet ’s new electric battery-powered Self-Propelled Modular Transporters (SPMTs) have begun operation at the international nuclear fusion research facility ITER in southern France.
The equipment is being used to transport heavy components for the construction of the world’s largest tokamak: a device used to prove the feasibility of fusion as a large-scale source of carbon-free energy.
Mammoet is supporting its client DAHER, a global logistics specialist, to transport key components, including 367t toroidal field coils and 440t vacuum vessel sectors. Two combinations of twelve axle lines of SPMT are being used inside the facility to move the components from storage to the assembly area. Pascal Taconne, Project Manager at Mammoet, said: “In July last year, ITER asked if we had an electric power pack available, and at that period it was a time when Mammoet had started to develop a new prototype internally. We explained that we could carry out the necessary steps to have it ready for the beginning of 2024.”
The next six months saw Mammoet perform extensive testing with third parties, such as soundproofing and electrical interference testing. It also carried out over 100 hours of testing using different types of cargo, to prove the technology could carry out day-to-day jobs with a full battery. Previously, component transfers were performed using conventional diesel power pack units, which are louder, and generate carbon emissions and fine dust particles that need to be filtered and evacuated from indoor locations.
As the tokamak needs to be built in a clean environment, where moisture, temperature and particulates are all controlled, the new transport solution brings major benefits. In addition to being cleaner and quieter, the ePPU can power both lines of SPMTs at once. This means even heavier movements, which require them to work in tandem, can be carried out fully electrically.
With the first successful electric component transfer conducted at the site, the project is demonstrating what the future could hold for the movement of heavy components. Michel Bos, Technical Specialist at Mammoet, said: “All the things that we have learned, building and testing the unit, and adjusting and making it better, have taught us so much about electrifying our equipment. The feeling that heavy movements cannot be done electrically has totally changed in the last year. We are now confident we can work day-to-day jobs easily, creating a more comfortable working environment for operators and supporting zero-emission construction areas. With jobs like ITER, we have proven it works.”