Soilmec with Cat, Cummins, Deutz and Volvo
Soilmec expanded its engine offer. Volvo Penta joined Caterpillar, Cummins and Deutz in Tier 4 Final. Monoblock transitivity from Tier 3 to 4 and service are the key features of its engine partners. Talking with Soilmec Development Vice-President… Since 1969, Soilmec means drilling. Now it controls eight factories in Italy, United States, Brazil, China, Dubai and India. In […]
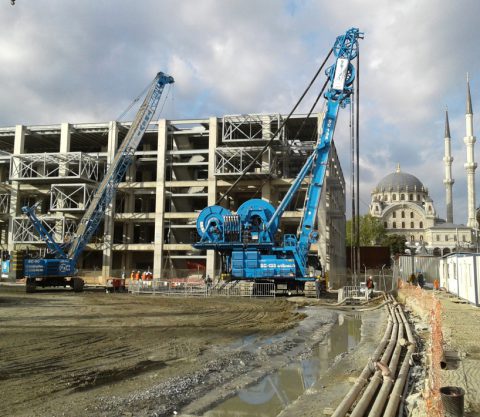
Soilmec expanded its engine offer. Volvo Penta joined Caterpillar, Cummins and Deutz in Tier 4 Final. Monoblock transitivity from Tier 3 to 4 and service are the key features of its engine partners.
Talking with Soilmec Development Vice-President…
Since 1969, Soilmec means drilling. Now it controls eight factories in Italy, United States, Brazil, China, Dubai and India. In Europe UK is its main market, Mexico is growing in the Nafta area featuring over 50 units delivered in two years. The Trevi Group relies on a technological and productive division, Soilmec, and an operative division, Trevi itself, linked by a continuous exchange of synergies and strategic information. We spoke with Federico Pagliacci, Soilmec Development Vice-President, to get “inside and behind the engine compartments”.
What are the criteria followed by Soilmec in choosing engine suppliers?
«Our product range includes 45 models ranging from micropiles drilling machines from 3 to 40 tons to the core business, the piling rigs from 35 to 160 tons. From heavy duty cranes equipped for diaphragms and foundations to hydromills water machines. The average annual production is around 250-300 units with a peak of 700 machines in 2007, after the Middle East market raise. The range of installed power goes from 70 to 700 kilowatts provided by Cummins, Deutz and Cat units. Volvo has recently joined the lot, after we had our first contacts at Bauma China».
Working to meet emissions regulations
Which are the critical issues of the transition from Tier 3 – Tier 4 Interim to Tier 4 Final?
«Soilmec achieves considerable figures in our market that are however small for our suppliers, forcing us to be subjected to the regulatory steps. Based on our information, Stage V should not have a critical impact in terms of size, contrary to what happened during the migration from stage 3 to stage 4».
What are the issues related to the migration to Tier 4 Final and the harshest work conditions?
«We use Scr, while installing Dpf only on request. In the transition to present regulations we had to redesign our machines in some cases. With regard to the environmental impact, our machines may also work in the desert, enduring temperatures up to 50 °C, and Tier 3 makes engine’s work easier».
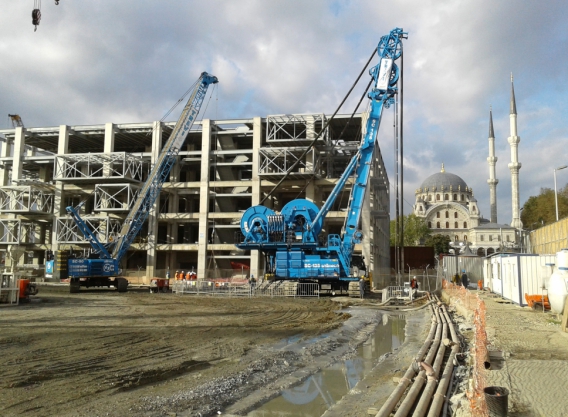
How important is fuel economy?
«More and more, considering that some machines may use up to 800-900 liters per day. The operator is used to an average speed of 1.800 rpm and could be not confortable with automatic shutdown functions. We are working instead on decreasing the engine rotation speed in order to reduce fuel consumption at low loads».
How about the alternatives?
1.800 rpm means working as a stationary engine…
«Yes, and in intermittent work cycles. Just think that the average translation from one drilling point to another is about 10-20 meters and operations are repetitive, requiring different power rates and discretionary use. We evaluated hybrid solutions but our work cycles do not allow energy recovery as it happens on many earthmoving machines. We are thinking about recovering energy during the release of the winch. But also in this case the energy amount is limited. The first Soilmec electric machines date back to the 90s. I’m talking about the positioners used in the Aosta – Monte Bianco motorway tunnels and high speed railway from Florence to Bologna. The current trend is of course heading towards electric applications».
Electric, then?
«In Mosul, Iraq, we use small electric driven drilling machines. These are entry level machines, delivering about 70 kilowatts. We are developing a research project that involves power rates up to 200 kilowatts. On urban sites we have to deal with noise limitations. New generation diesel engines involve larger cooling systems and consequently noisier fans».
What about gas fuels?
«Some prototypes of excavators are currently under development, but the implementation of these experiments on our machines is quite complex, just think about the refueling on construction sites. Even the simple management of oxyacetylene tanks for cutting is critical on site».