Vervaet: a spreader powered by Volvo Penta D13
Volvo Penta has found that by working closely with an OEM, with each company pooling its specialist knowledge, a solution can invariably be found to overcome any problem. The Quad 550 spreader is the result of the cooperation with Dutch OEM Vervaet.
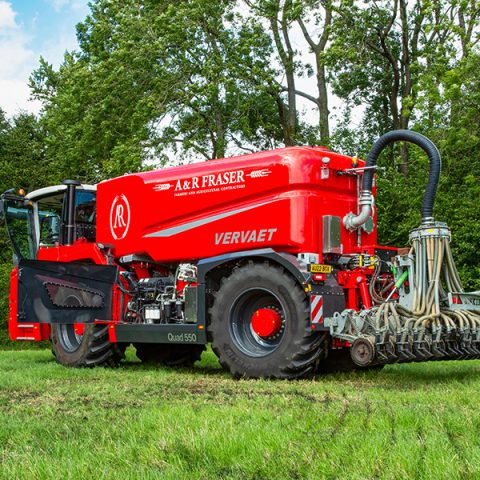
Injecting liquid manure directly into the soil, Vervaet’s distinctive three-wheeled self-propelled slurry spreaders have become a head-turning sight on fields across Europe and beyond, with its five-wheel variants having much the same effect on observers on more undulating terrain. Ever since 1990, when the first Trike was built at Vervaet’s facility in Biervliet, southern Holland, this unusual design to reduce ground compaction has been a big hit with farmers worldwide. But now a very different version has been developed in response to evolving customer needs.
“Historically, we’ve sold many three- and five-wheelers, but demand abroad is for four wheels, which is why we’ve built the Quad 550, our most powerful and technologically advanced slurry injector yet,” explains Robin Vervaet, co-owner and CEO of Frans Vervaet BV. “Before producing a new machine, we always investigate the customer’s needs, look at what the competition is offering, and then see what we can do to improve on that. But our philosophy has always been to keep the machine as simple as possible, as that helps to keep the cost of maintenance low.”
Vervaet and a partner like Volvo Penta
With those parameters in mind, a call to sound out Volvo Penta as an engine partner for the new design was an obvious early step. Producing 550 hp (405 kW), the company’s powerful yet compact inline six-cylinder, 12.78-liter TAD1385VE Stage V diesel engine clearly provided many of the key attributes required by a vehicle of this stature. By delivering up to 2650 Nm from engine speeds as low as 1200 rpm all the way up to rated power, for instance, the Quad 550 offers maximum torque in the crucial 5-15 km/h speed range in which these machines typically operate.
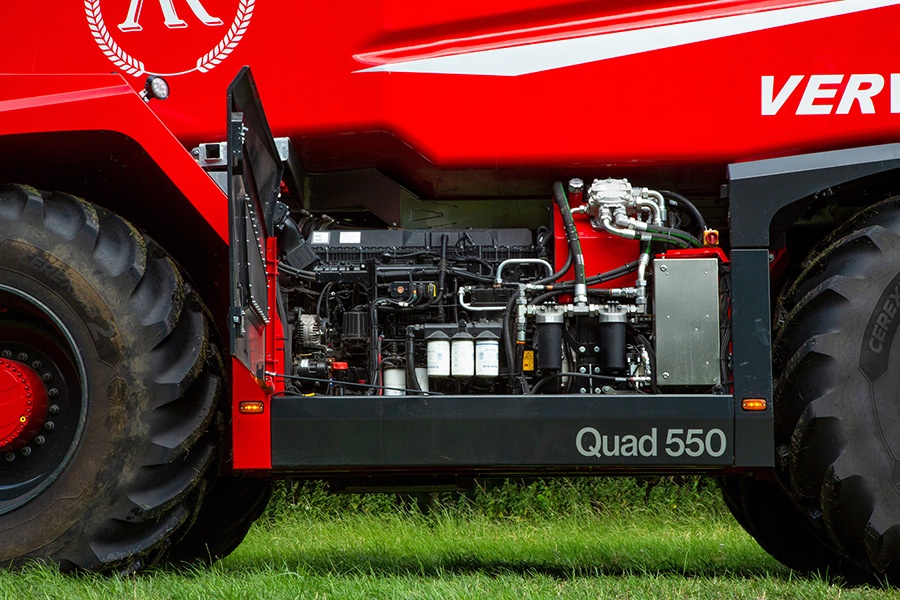
In addition to enabling first-class fuel efficiency, this allows the onboard pump to apply fertilizer at an incredible rate of up to 13,500 liters per minute (more than half of the huge slurry tank’s capacity), while offering 9000 kg of lifting capacity at the rear of the machine. None of these impressive statistics conflicted with Vervaet’s demands for simplicity, however. All of that impressive power and torque had to be supplied from a system that would add as little bulk and weight as possible to allow for optimal installation on the new machine. And at just 1251 mm long, 923 mm wide and 1200 mm high, and with a dry weight of 1215 kg, the D13 certainly met these requirements.
Easy access to vital components was a key design element from the outset, and is reflected in the unhindered accessibility of the engine compartment, air-filter, and fuel and AdBlue tanks, with ground-level access to service points aiding safe, simple daily maintenance.
The OEM was also keen to position the radiator at the very front, where it is at reduced risk of blockages from dust and other residues – a location that could have potentially resulted in some of the D13’s vast horsepower being lost through parasitics due to its mid-mounted position on the left-hand side of the machine. However, due to Volvo Penta’s preferred approach of working in partnership with its customers, rather than just acting as an engine supplier, this potential problem was quickly resolved. With the D13’s highly efficient belt-driven cooling pump and compact, simple and reliable Exhaust Aftertreatment System (EATS) already creating the ideal conditions for reduced cooling capacity requirements, enabling a smaller radiator to be fitted, the two manufacturers co-operated to develop a concept that ensures optimal operation in all conditions. In fact, even with its engine and driveline under full load, the Quad 550 suffers no loss of performance when working in ambient temperatures as high as 45°C.
“Working together with Volvo Penta we have developed a clever system in which all of the important components such as the engine, cooling and transmission are well coordinated,” adds Robin. “Thanks to the matching of the engine and transmission in perfect harmony, the Quad delivers unbeatable torque.”
Working closely with an OEM
Volvo Penta has found that by working closely with an OEM, with each company pooling its specialist knowledge, a solution can invariably be found to overcome any problem. Whether providing full installation support – covering everything from performance predictions and application integration to verification and test – or even creating modified engine designs to realize the desired performance, this approach is an extremely effective method of developing the best products possible.
Additionally, by supplying the engine in one complete package, along with its required accessories such as cables, filters, exhaust flanges, cooling package and aftertreatment system, Volvo Penta greatly simplifies the manufacturing process, explains Anna Maria Ullnert, Director Global Business Development, Industrial Sales at Volvo Penta: “Instead of our customers dealing with several suppliers and adjusting all parts separately, we offer a single point of contact and an engine ready to be lifted into the machine for simple installation. But our involvement doesn’t end there. Knowing the importance of uptime, we provide support on-call 24/7 for the rest of the engine’s lifecycle to ensure it runs effectively and reliably.”
Reliability and a strong global service network that could support Vervaet’s worldwide customers were also key considerations when choosing its engine partner, but these were easily satisfied with the D13’s worldwide engine homologation and ability to be serviced by any Volvo dealership, whether Volvo Penta, Volvo Trucks or Volvo CE. Should a technician be required onsite, the advanced Engine Management System (EMS) 2.4 greatly simplifies diagnostics and fault tracing, while speeding up the identification of any spare parts that may be required.