CHP without waste of water
POLITO and UNAERP are monitoring the emissions from CHP industrial biomass boilers without wasting water
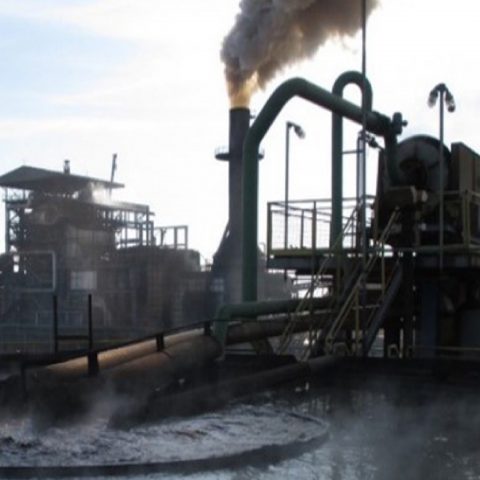
Energy efficiency definitely means avoiding waste, so also reducing water consumption during CHP. A study has been published by the Politecnico di Torino together with the Universidade de Ribeirão Preto on dry techniques for reducing particulate matter, which takes off from the case study of Brazil’s sugarcane industry (HERE, BorgWarner and ORC) .
How to reduce PM and water consumption during CHP
According to Politecnico di Torino (Italy), in Brazil and other countries, a lot of water is used, on average, to operate removal systems for particulate matter (usually referred to as PM) called “wet scrubbers”. In these devices, water is nebulised in a column in order to englobe the particles in the little drops of water.
SUSTAINABILITY AND CHP: A WEBINAR FOCUSED ON SMART GRIDS
This system is used, above all, to reduce emissions coming from bagasse-fed steam generators, “bagasse” being the residue from the industrial processing of sugarcane. The steam and energy obtained using bagasse combustion are needed to operate the sugar and alcohol production plants. However, the wet scrubbers produce sludge that contains harmful substances and, for this reason, must undergo a special treatment, without being disposed as they are. There are also dry technologies that, thus, do not require the use of water, which is much more precious than it used to be, and that still ensure emissions control. The problems with these innovative techniques include the initial cost of investment and, very often, the consolidated habits that aren’t questioned, especially because the majority of sugar and alcohol producers are reluctant to innovate.
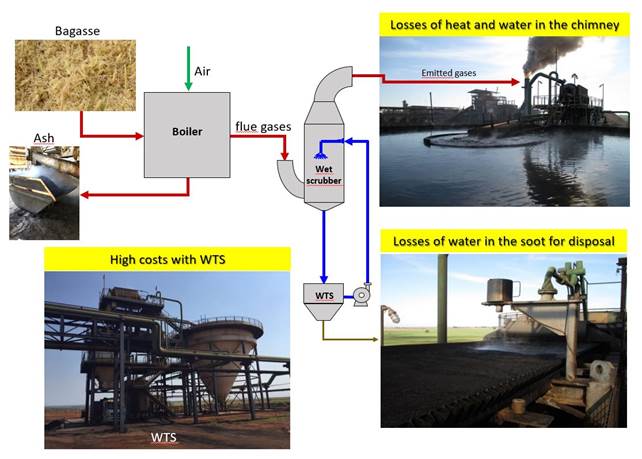
Brazil and sugarcane
Brazil, as the largest global producer of sugarcane, was chosen as a case study, using the data of a typical ethanol and sugar production plant in the South American country. The key performance indicators of a steam generator and wet scrubbers were assessed experimentally over a sugarcane harvest season and were compared with the legal requirements for particulate matter emissions and water quality in Brazil. The results highlight the inefficiency of the water-based system, which used only 30% of the water to operate the water scrubbers and 70% to transport the dry particle material collected in the discharge duct of the steam generator, in the heat exchangers, and in the multi-cyclone separation system.
Evaporation caused atmospheric loss of 10.5% of the cleaning water. Finally, transporting the damp particle material thus collected (7.9t/h with 78% water inside of it) for disposal in the fields entails significant petrol costs, as well as significant water loss. The inefficiency is also economic: the operation of the wastewater treatment plant accounted for 62% of the total capital expenses of the cleaning system, while the wet scrubbers represented just 38%.
Professor Innocentini said
“The partnership between POLITO and UNAERP was essential for demonstrating that managing water used for cleaning the fumes produced by bagasse-fed steam generators is still neglected and uneconomical in the majority of plants producing sugar and ethanol. Thus, thermal energy and water, both precious resources today, are wasted”, Prof. Murilo Innocentini emphasises. “The same problems may occur in all biomass-fed steam generators where water is used to control particulate matter emissions and limit the environmental impact. Our partnership proposes alternatives for implementing and optimising dry fume-cleaning technologies to help industry comply with the PM emissions limits, while saving in the process. Our intention is to establish a partnership with the industries concerned in this optimisation, for example, by constructing a pilot plant for testing the dry collectors, or even re-sizing of their wet scrubbers so that they are more economical and ecological. POLITO and UNAERP engineers and students are welcome to come on board to face this challenge”.