Fraunhofer IPT H2GO
In the "H2GO" research project, researchers at the Fraunhofer IPT are developing two different processes for forming bipolar half-shells
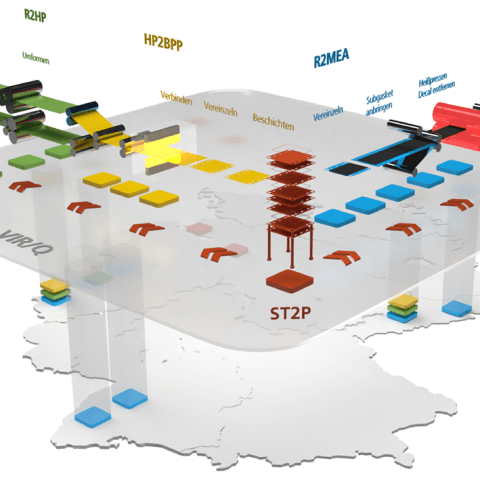
H2GO is yet another challenge from the Fraunhofer Institute for Production Technology IPT on the research front of alternatives to fossil-based energy production. We have told you about the photovoltaic system for trucks, methanol and the production of battery cells.
Large-scale fuel cell project. The Fraunhofer H2GO project
The core of Fraunhofer’s H2GO project is research on bipolar plate halves. To develop the production technology for the individual components of the fuel cell, H2GO is organized into five sub-groups. Work is being carried out on the bipolar plate made of metal and compound materials, the membrane electrode assembly, de-assembly and virtual production. Also in Germany, we focused on Schaeffler’s bipolar plates, which give stacks a power density about 20% greater than the previous generation plates. Researchers at Fraunhofer IPT have identified two key processes for manufacturing fuel cells: discrete forming and roll-to-roll (R2R) forming. In discrete forming, a fuel cell design is embossed onto a metallic sheet using a tool insert, or active part, within a progressive die. In R2R forming, the design is applied to a metallic foil using an embossing roller. As part of the H2GO research project, Fraunhofer IPT scientists are working to bring bipolar plates into series production through progressive composite manufacturing. To enhance formability, they are integrating a heating module into the existing punching and forming units, making the thin sheet material easier to shape.
To meet the tight tolerance requirements for bipolar plates at high production volumes, the team is also developing an inline quality inspection system for the progressive die. Additionally, they are using a roll-to-roll machine to optimize the continuous forming process, testing and evaluating the geometric accuracy and structural precision of the bipolar plate halves under different process parameters.
Sensors and DMC
To further refine the process, the team is integrating additional sensors into the embossing rollers to monitor deformations. By comparing and validating the measured values through simulations, the scientists aim to improve and simplify the machine’s design. Moreover, the roll gap between the embossing rollers is precisely controlled using enhanced measuring technology, ensuring greater accuracy in the final bipolar plates.
In both discrete and roll-to-roll manufacturing, a bipolar plate half undergoes multiple steps, including cleaning, sealing, and laser processing. Researchers use data matrix codes (DMC) to track each workpiece through the process chain. This enables real-time monitoring of quality and machine data, helping to optimize production, improve product quality, and reduce waste and costs.