Improving the fuel efficiency of an internal combustion engine (Part I)
The matter of fuel efficiency is crucial indeed for internal combustion engine to be competitive in the future scenarios of mobility. Here we publish the first part of an authoritative technical contribution about such a key issue. The next parts will be published in the next weeks on our website. The author of the article […]
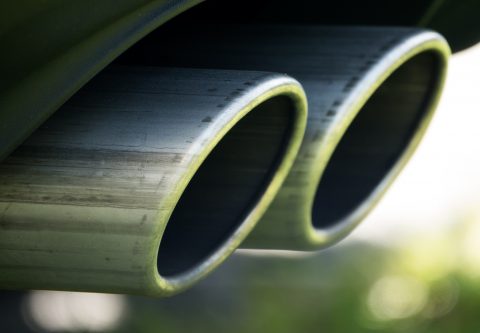
The matter of fuel efficiency is crucial indeed for internal combustion engine to be competitive in the future scenarios of mobility. Here we publish the first part of an authoritative technical contribution about such a key issue. The next parts will be published in the next weeks on our website. The author of the article is Serguei Tikhonenkov, MSc.
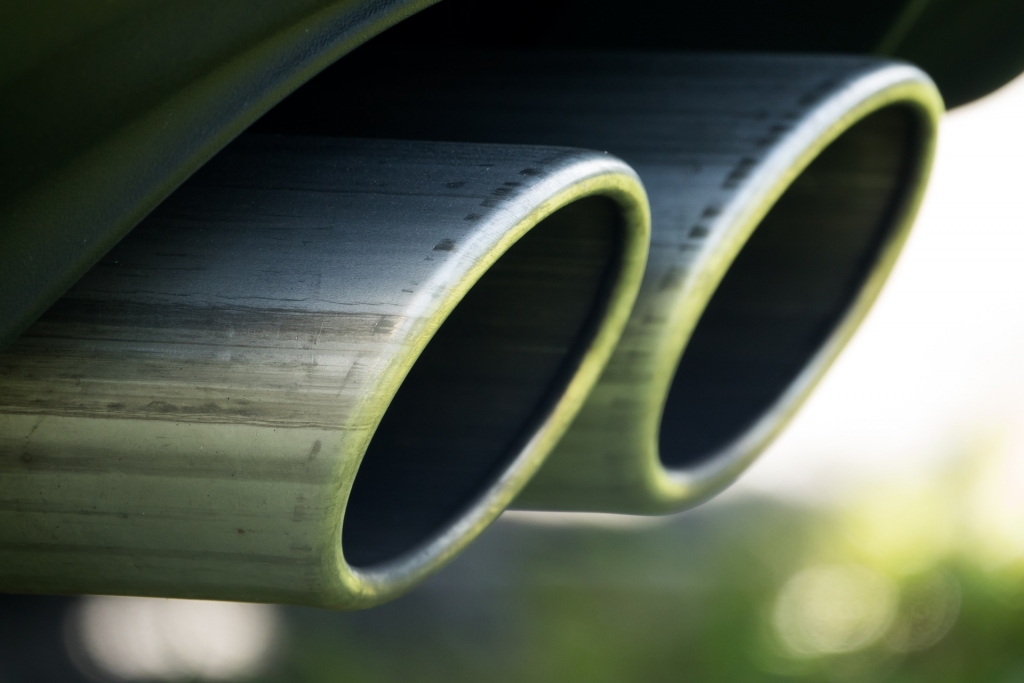
Increase the efficiency of fuel utilization
The current scale of production of reciprocating internal combustion engines has led to significant environmental impacts. Harmful emissions have caused a critical concentration of chemicals in the air, water and land, and have become dangerous for humanity. Currently, the problem has no solution and is characterized by a steady upward trend.
One of the main ways to reduce harmful emissions is to increase the efficiency of fuel utilization. The amount of harmful emissions depends on the perfection of the engine design. It should be noted that significant work has been done recently to perfect the engine with noticeable results in reducing harmful emissions.
At the same time, the tendency of harmful emissions to increase their impact on the environment persists, which creates an incentive to search for new solutions.
FIVE HOT MANUFACTURING TRENDS IN 2020
Modern internal combustion engine
Modern internal combustion engines are built using the classical design: cylinder, piston, connecting rod and crankshaft, and we should note a number of known flaws in traditional engines:
- Inefficient combination of pressure within the cylinder and tangential force on the crankshaft. Two points need to be looked at closely here:
- the ignition of the fuel-air mixture begins before the piston moves to the “top dead center” (TDC). This means that the total pressure of the fuel-air mixture compressed in the cylinder and the pressure of the ignited fuel-air mixture impede the movement of the piston to the TDC. This factor leads to a loss of power.
- With the pressure increasing to a maximum and combustion of a significant part of the mixture, the crankshaft rotates 180 degrees, and the ratio of the tangential force on the crankshaft to the force acting on the piston varies from 0 to 1 and from 1 to 0.
48V CARS. THEY’LL DOUBLE IN FIVE YEARS
Thus, two phenomena are observed when the crankshaft rotates 180 degrees:
- The pressure changes from a maximum to a minimum value (Chart 1).
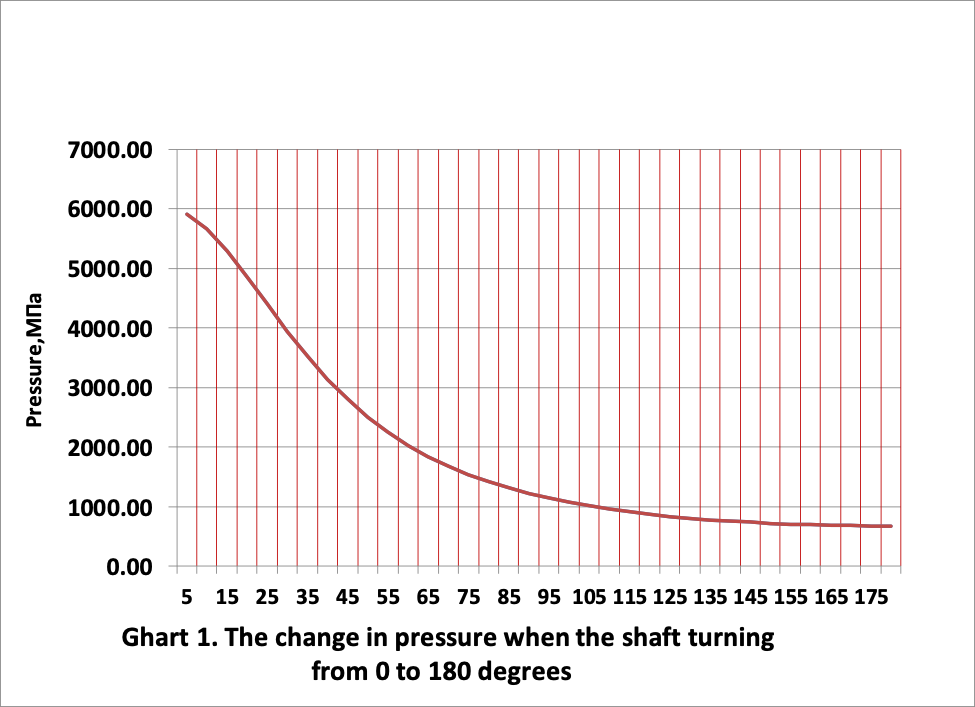
- The lever size on the crankshaft changes from 0 to 1 and from 1 to 0 (Chart 2).
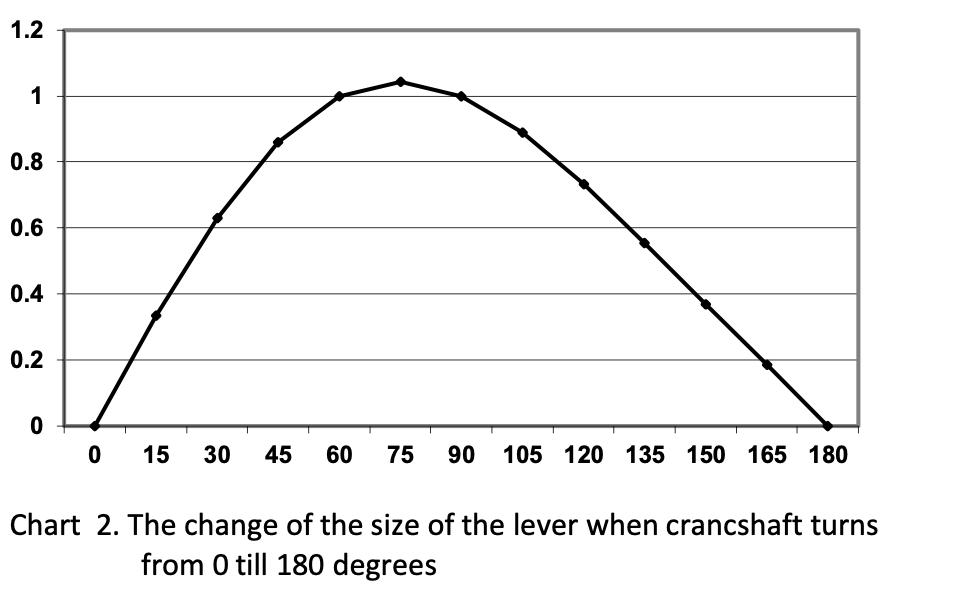
srgtikhonenkov@gmail.com