Lithium-ion electrode slurries for batteries
A new technology for the production of lithium-ion electrode slurries inducts powders dust-free under vacuum into a liquid stream, thereby enabling dispersion of the powder particles within milliseconds
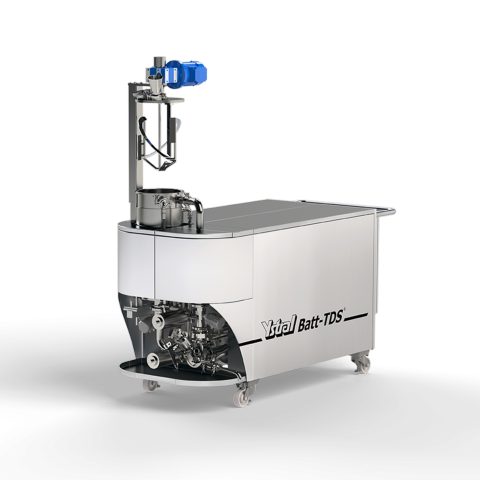
Many ingredients are needed for the recipe for battery applications including the production of lithium-ion electrode slurries. David Manke tells us about it, Chief Technology Officer and Managing Director of German machine and plant manufacturer ystral.
A drastic reduction of process times in the production of lithium-ion electrode slurries for batteries
A planetary mixer (s. Fig. 1) requires a high viscosity (several million centipoise) to generate the shear stress required for dispersion. As the shear rate is determined by the rotational speed of the mixing blades, the possible shear stress increases in line with the viscosity (Newton’s law on the viscosity of liquids: shear stress = viscosity * shear rate). However, with very high viscosities, the motors required for the movement need a high torque and capacity. As only a fraction of the capacity is available for dispersion at a time, a large part of the capacity is wasted in an inefficient process. To maintain this shear stress, the solvent must be retained fully or in part, leading to wear and metal contamination caused by hard cathode powders. The binding agent is normally pre-dissolved at higher temperatures, cooled down, filtered, and slowly added to the already dry mixed active and conductive materials using a High Speed Dissolver (HSD, image below), an inefficient powder wetting technology. This step is performed in the planetary mixer in which HSDs are also installed, whereby viscosity decreases with an increasing quantity of binding agent. The planetary mixer and HSDs must perform mixing and dispersion together in such a process.
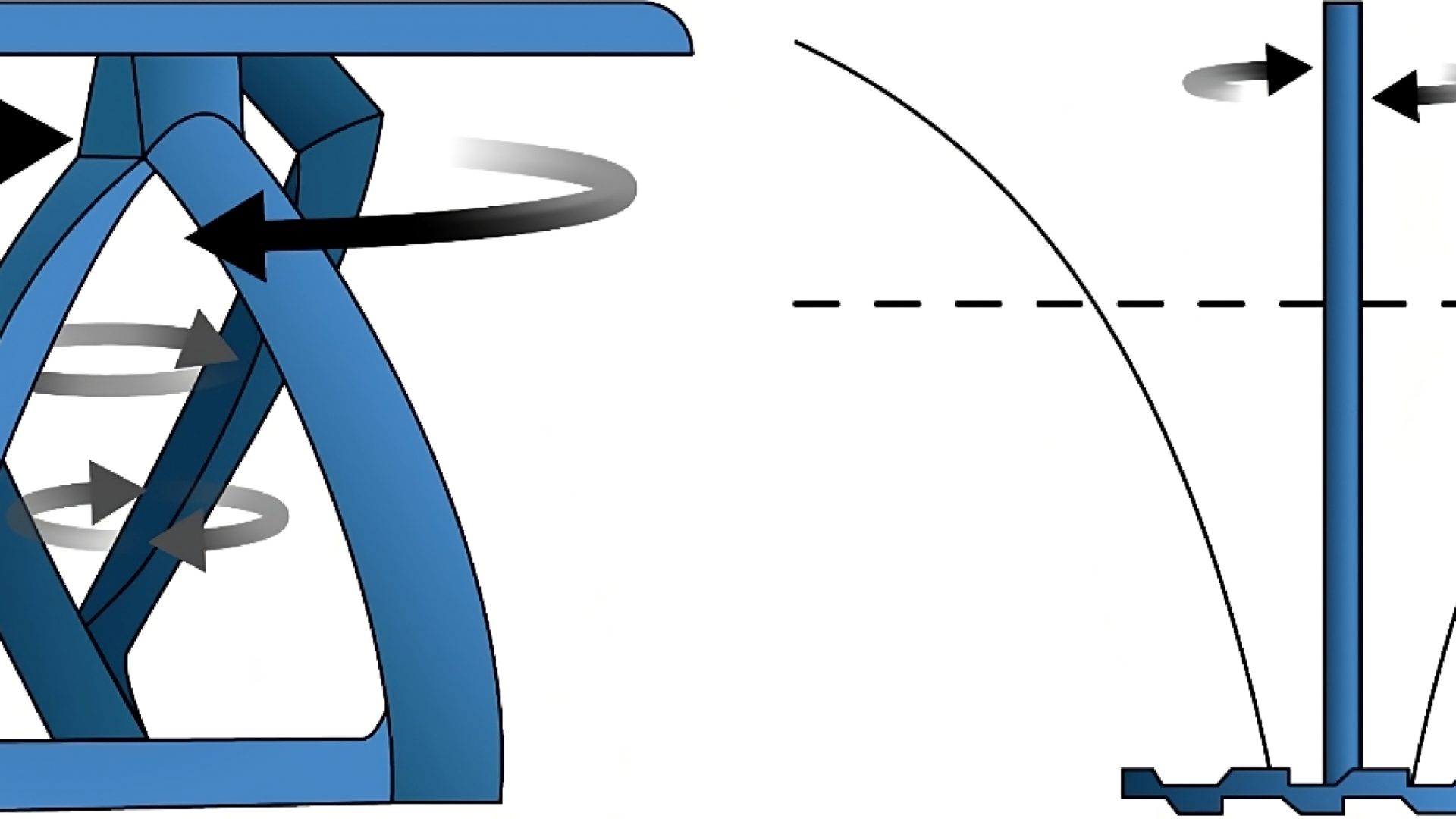
Production of battery slurries with these conventional technologies is energy-intensive, slow and associated with an enormous space requirement. Industrial planetary mixers might achieve batch sizes of approx. 3,000 litres by now for the production of electrode slurries. However, the mixing time is now more than 3 hours, and adding to this still one to three hours for cleaning between individual batches. Meeting the extremely strong increase in demand for storage batteries will be barely possible through linear scaling of traditional batch mixing technology. Against this background, the mixing and dispersion technology specialist ystral has developed the mixing platform Ystral Batt-TDS, which overcomes the limits of traditional processes, enabling the production of battery slurries with a significantly lower time, energy and space requirement. The Batt-TDS mixing concept for electrode slurry consists of a circulation process with an inline mixer, which inducts powders dust-free into a liquid stream and disperses them, as well as a 3D mixer, which achieves fast batch homogenisation in the vessel with low energy consumption and low shear rate. Dispersion in the inline mixer takes place under vacuum in this process. Instead of high viscosity, the inline mixer operates with a significantly higher shear rate, thereby achieving high shear stress, which is inversely proportional to the sub-mm gap between a rotating rotor and the stator. Strong speed gradients are generated in this dispersion area, which correspond to the shear rate. The specific capacity can be increased 10,000-fold, and the shear stress can be concentrated to a few milliseconds of dispersion time in the active mixing area – instead of hours as for conventional mixers.
Ystral Batt-TDS
The inline mixer of the YSTRAL Batt-TDS mixing platform is specifically tailored to the requirements of battery slurry production, as rotor-stator systems are usually limited to viscosities that are lower than those relevant to electrode slurries. With a large stator diameter, the inline mixer is designed in such a way that it can receive the high viscosities and control the exposure time with high shearing, by decoupling the shear rate from the controlled powder and liquid throughputs.
With the ability to generate shear stress independent of viscosity if required, the gentle, but efficient separation of agglomerates enables the dispersion of powders almost in real-time in a broad viscosity range, whereby the viscosities can also be lower than those required for effective dispersion in a planetary mixer. A crucial advantage of this concept is that the shear rate can be tailored to the process requirements of an individual powder, so that a shear stress- and energy-optimised process is possible in a certain sequence, without the need to use different devices for each type of powder.
Production scale
The mixing platform YSTRAL Batt-TDS is available in four sizes – from a 12-litre unit for fast formulation and process screening (Batt-TDS navi, s. Fig. 2), up to a production system for large-scale production processes for cathode or anode slurries with a batch size of 10,000 litres (Batt-TDS Pro supra, s. Fig. 3). Results from the trial scale can be easily scaled up to the production scale here. At the production scale, the new technology achieves a more than 10 times higher productivity compared to conventional technologies, and a productivity that is twice as high compared to available extruders. Fig. 4 shows a comparison of conventional planetary mixers and the Batt-TDS Pro systems mid and supra for the production of electrode slurries at the scale of currently planned factories (40 GWh / year), illustrated for NMC 622/graphite batteries. As large factories for cathode processes must be air-conditioned, the option to produce large quantity of slurry in a small space results not least in significant savings potential with regard to energy consumption and the costs for buildings in which the machines are housed.
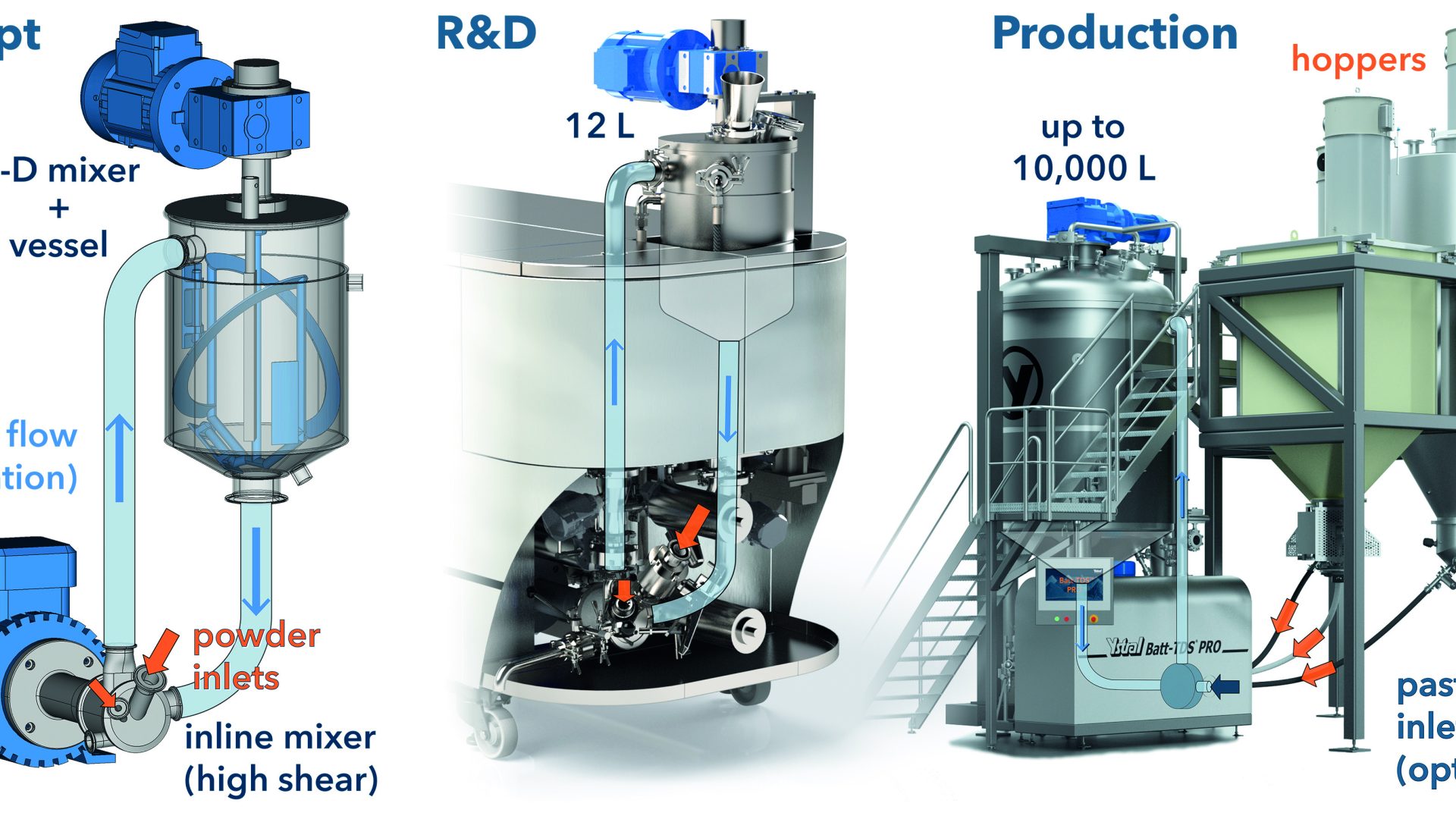
Tests conducted by the Karlsruhe Institute of Technology in Germany have shown that Batt-TDS cells have a better conductive morphology and thus lower internal resistance with increasing throughput than conventionally produced cells. For this purpose, NMC-622 cathodes were coated from slurries, which were produced separately in 12- to 15-litre batches with a Batt-TDS navi, as well as with a planetary mixer for comparison. Cells, which were produced by the KIT with Batt-TDS cathode slurry and an identical anode, showed a 27-percent increase of the long-term cycle capacity compared to the materials mixed in the planetary mixer. No metal contamination by iron (ICP-OES, detection limit: 8-ppm Fe) was detected in the NMC slurry of the liquid-lubricated Batt-TDS process.Probably from the end of the year, battery manufacturers will be able to perform tests on an R&D system with the YSTRAL Batt-TDS navi dispersing system within the scope of the project “Battery Cell Research Manufacturing (Fraunhofer FFB)” in Münster / Germany.
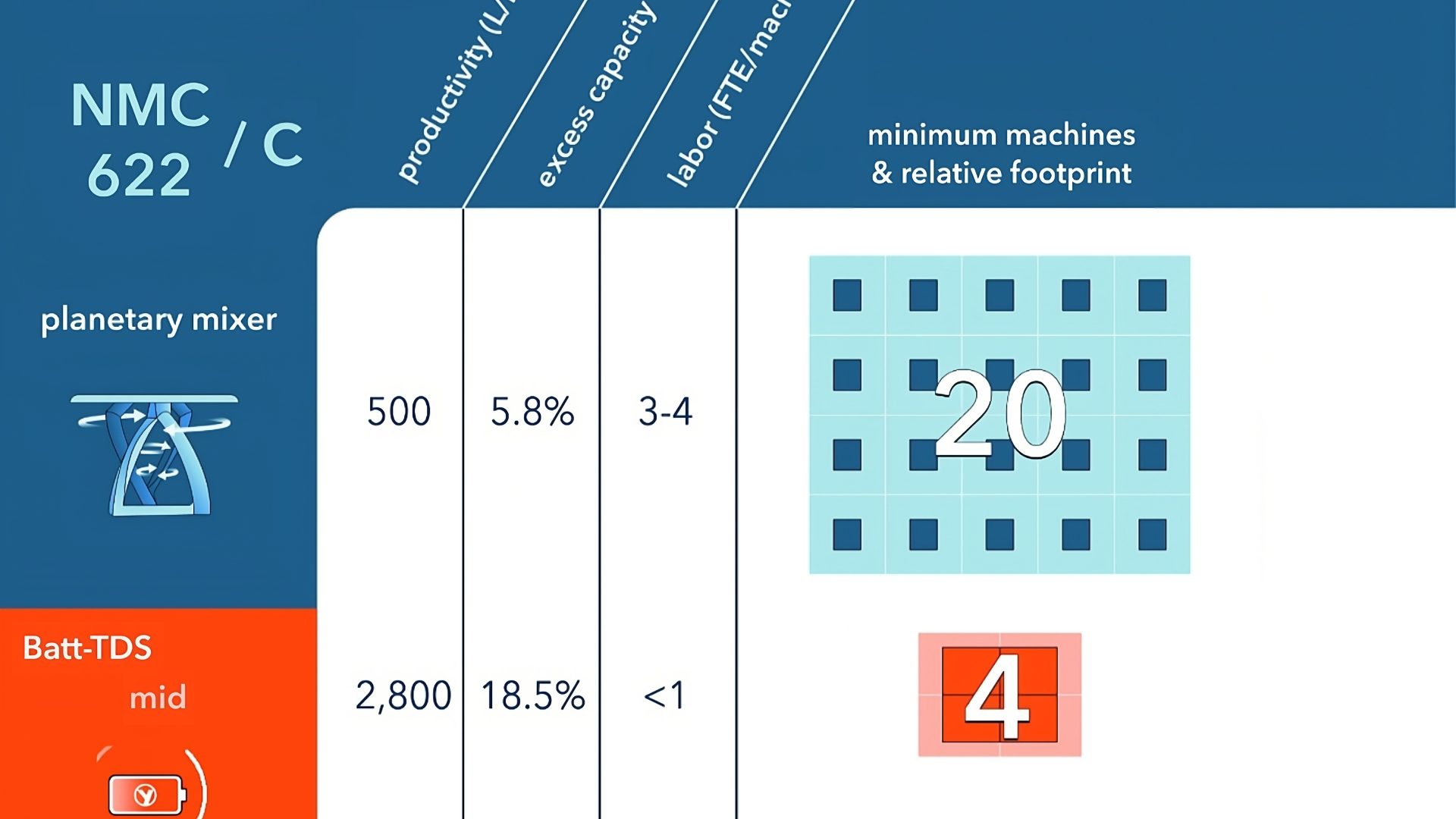