Steyr Konzept: hybrid for working ‘hard and green’
Steyr Konzept. The CNH Industrial Group proposal delegated to Steyr (tractors) and FPT Industrial (powertrain and driveline) opens up new horizons in the world of hybrid engines. Surprisingly, the traditional transmission (often a structural and certainly characteristic element in the world of agricultural traction) disappears and is replaced by a solution with 4 independent hub wheels with […]
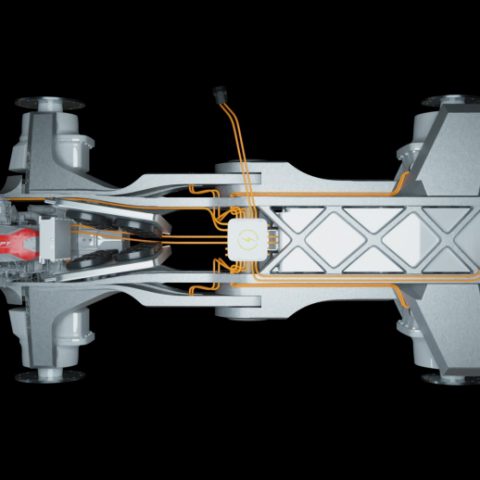
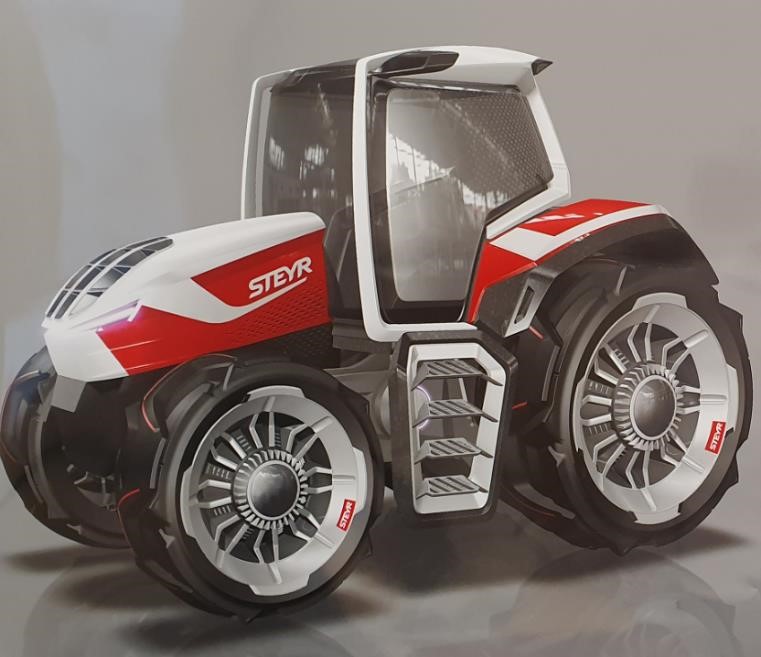
Steyr Konzept. The CNH Industrial Group proposal delegated to Steyr (tractors) and FPT Industrial (powertrain and driveline) opens up new horizons in the world of hybrid engines. Surprisingly, the traditional transmission (often a structural and certainly characteristic element in the world of agricultural traction) disappears and is replaced by a solution with 4 independent hub wheels with integrated system composed by electric motor and its dedicated gearbox needed to ensure the proper transmission ratio to the wheel. The endothermic engine is paired with a generator that, provides the electric power for e-traction, e-implements, electrified tractor functions (PTO, Hydraulics and Auxiliaries) and for battery recharging. A recharging plug-in socket allows the battery charging during overnight.
We talked about Steyr Konzept with Selin Tur, Head of FPT Industrial E-Powertrain.
Let’s talk about fuel consumption: you assume a 10% reduction. What about emissions? What was the primary objective that made you choose this solution?
On some specific tractor missions, the combined effect of the friction reduction thanks to the downsizing from 6 to 4 cylinders and the optimized engine working points – thanks to the flexibility of serial hybrid architecture – allows to achieve the fuel consumption saving. Emission level are kept according legislation requirement. A ‘pure electric’ drive mode is possible for zero-emission and low-noise operations with autonomy range depending on the vehicle mission.
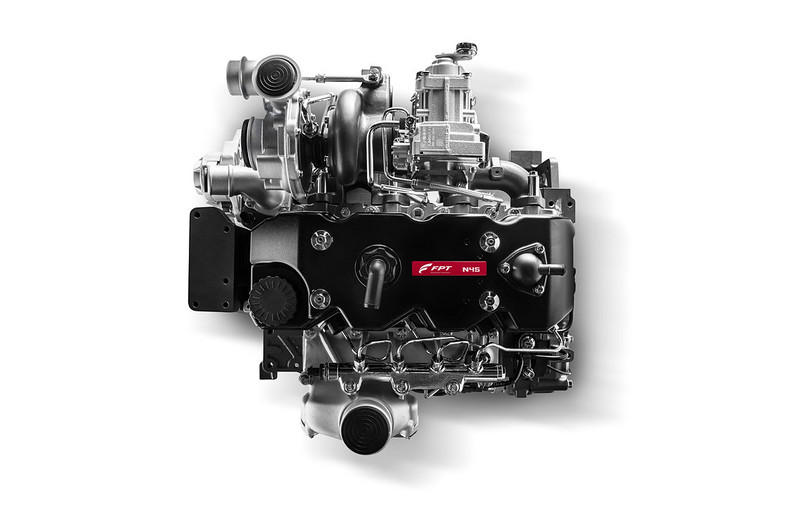
The battery pack of Steyr Konzept seems to be integrated into a reticular structure that replaces the classic rear axle drivetrain of traditional tractors. Considering the stress this structure endures during working cycles, which problems you had to solve (also in terms of passive safety of the battery pack) because of such a choice?
The first challenge we faced has been to design the frame for modularity purposes in order to keep the door open for future developments, allowing at the same time proper accessibility for the maintenance operations. Moreover, the frame has been sized to grant the proper robustness for the typical duty cycles.
The abolition of the traditional transmission means that the 4 electric motors are supposed to work at very low speeds (even a few meters per hour) for longer periods: how do you deal with the issue of their cooling?
The concept includes high speed and high efficiency electric drives with integrated gearbox. A dedicated liquid cooling system provides the proper amount of coolant for all the e-components (e-motors, inverters, batteries). The main radiators with dedicated e-fans have been installed under the vehicle hood.
The presentation mentions ‘modular’ batteries: which capacities are you thinking about?
Two packs of 30kWh each are foreseen to ensure 30min autonomy in zero-emission driving mode or inner-city zone on standard heavy-duty mission.
The maximum power at the wheels is 250 kW. Not being isodiametric, how is it divided between front and rear axles?
40% front and 60% rear, up to 250kW for hybrid electric boosting mode for improved dynamic behavior on high load demand in the field.
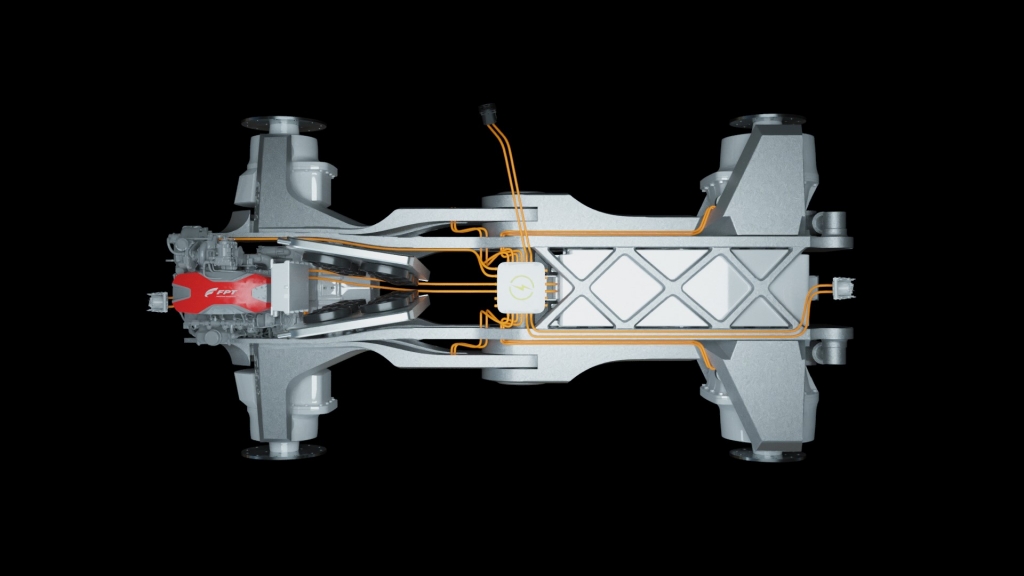