The thousand skills of Cummins full-electric and PTO
Cummins full-electric and PTO. Why comparing apples to oranges? Because we’re talking about Cummins, who expresses himself 360 degrees in the drive train. Let’s go to explore the full-electric excavator. According to Cummins press release: Cummins full-electric and PTO. Now, a XCMG electric xcavator Cummins Inc. with XCMG, the 4th largest construction machinery company in the […]
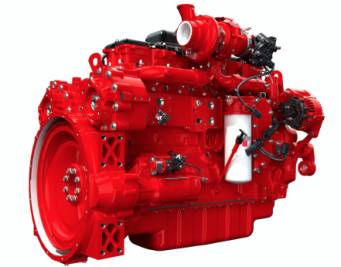
Cummins full-electric and PTO. Why comparing apples to oranges? Because we’re talking about Cummins, who expresses himself 360 degrees in the drive train. Let’s go to explore the full-electric excavator. According to Cummins press release:
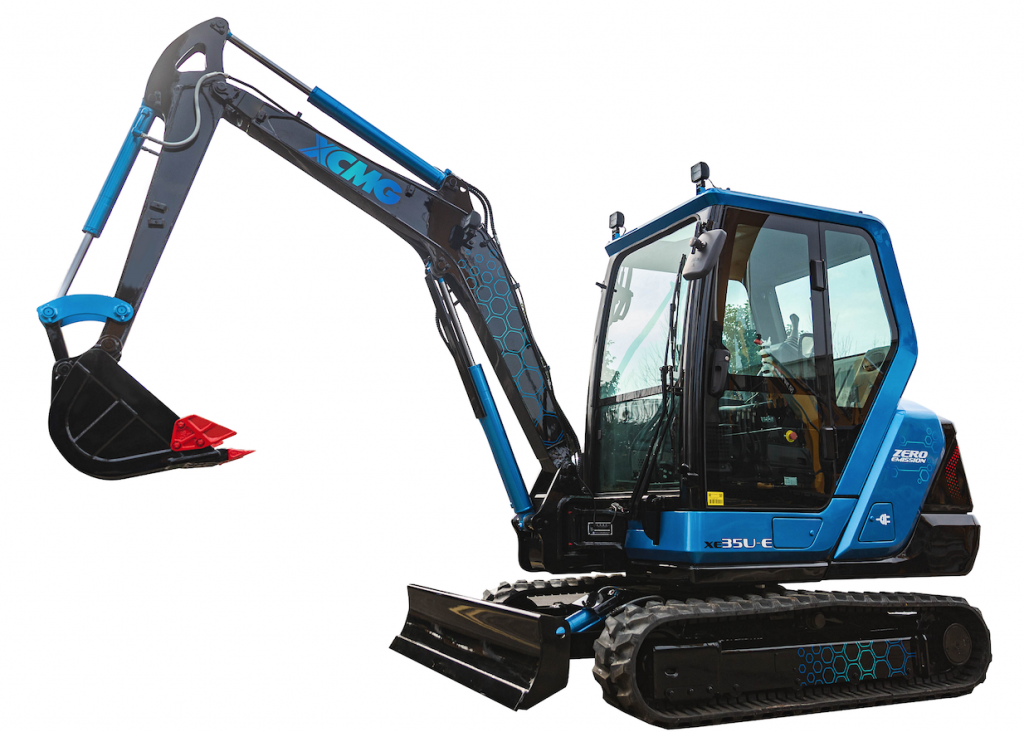
Cummins full-electric and PTO. Now, a XCMG electric xcavator
Cummins Inc. with XCMG, the 4th largest construction machinery company in the world, have designed and built a 3.5-ton electric excavator to serve as a technology demonstrator. The XCMG electric excavator powered by Cummins made its debut at this year’s ConExpo, in Las Vegas, Nevada, USA. The excavator earned its descriptor as ‘beautiful’ from winning the most beautiful machine award at the show, beating some tough contenders to the top spot. The new electric excavator is suitable for operating on work sites in densely populated towns and cities around the globe, surpassing stringent emissions requirements and keeping noise to a minimum while getting the job done. Powered by Cummins BM5.7E battery modules, the excavator has 45 kWh of battery power. Each battery module is designed for very high shock and vibration capability to endure the harsh conditions of the construction environment. Precise matching between motor and hydraulic system creates an efficient, reliable and quiet drive system, making it ideal for use in urban and suburban construction. On a single charge of less than six hours, the excavator meets operational needs for a full 8-hour shift. Short charge time means that equipment can be charged overnight, eliminating downtime and taking advantage of off-peak energy savings. After its win in Vegas, the excavator is now back in China where it will be used in a series of performance and customer tests conducted by Cummins and XCMG, to prove capability of the demonstrator and refine a robust solution for the market. This project is part of Cummins’ and XCMG’s agreement to collaborate on research, development and integration of technologies across a wide range of product lines.
And now we move on to the new engine power take-off (PTO) capabilities to support key applications such as cranes, crushers and screeners, developed by Cummins for the B6.7 and L9 Performance Series Power Units. What are we talking about?
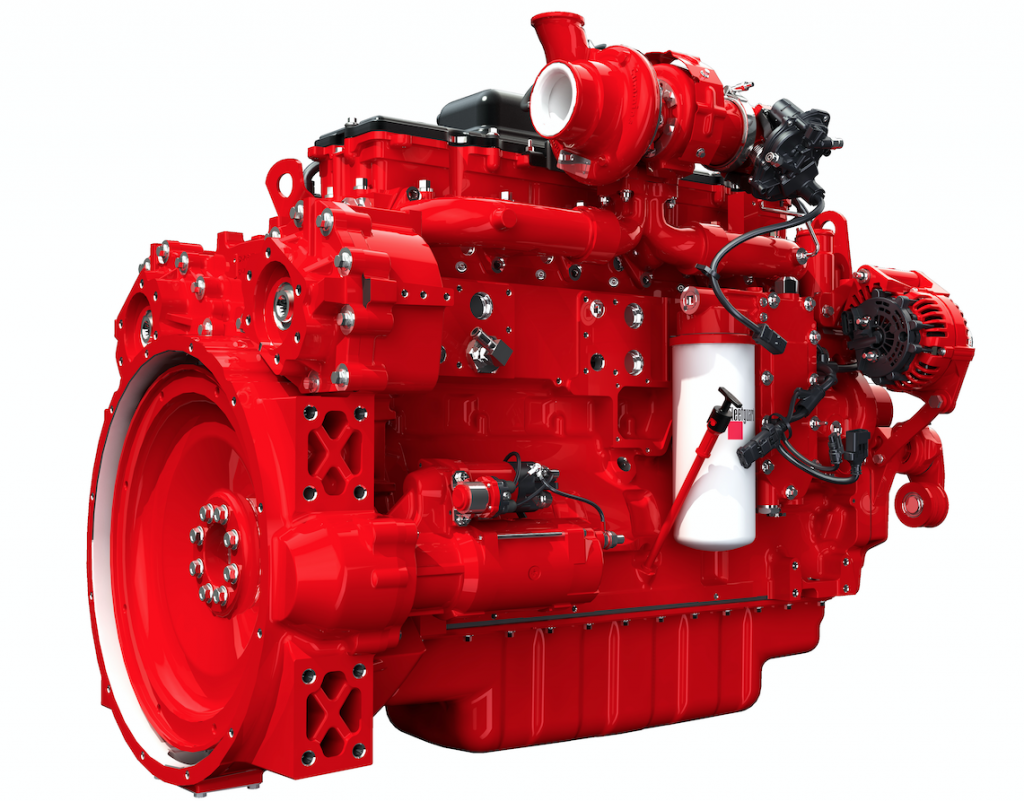
B6.7 and L9 Performance Series Power Units new engine power take-off
Cummins’ power units are available from 75 – 503kW (100 – 675hp) delivered as a complete and ready-made package. This comprises an engine, exhaust aftertreatment system, radiator and cooling system, plus auxiliaries such as mounting feet, hoses and an air cleaner. More than 60% of the content is pre-approved, making the machine integration process simpler and quicker. Jeremy Harsin – Cummins Off-Highway Marketing Director said: «Our Performance Series power units offer a flexible drop-in solution for manufacturers. The high-power density of our engines enables them to deliver high machine capability for hard working applications such as crushing, screening and pumping.» Examples of installations to date include the L9 Power Units powering Anaconda’s new J12 and I12 crushing machines. The B6.7 version is available with Bandit in their Intimidator 20XP tree chipper plus NLB Corp’s water jetting systems. «To increase the flexibility and capability of the power units, we are integrating new single and dual rear-engine power take-offs (REPTO). These complement their standard PTO capability used for items such as hydraulic pumps. We are also making these available on the base engines without the pack,» added Harsin. As an example, fitted with the dual REPTO, the L9 will have a total drive capability of 560 Nm. This will make the engine capable of driving additional pumping capability through SAE B 2 and 4 bolt mounts. Integrated into the flywheel housing the dual REPTO is compact and has a minimal impact on engine packaging. Added weight is approximately 100kg. «For equipment manufacturers, they have the ability to efficiently drive more from the engine without the need for additional aftermarket systems. This would support driving of hydraulic pumps for all sorts of machine functions from steering systems to fans, etc. It will reduce installation costs and complexity, for a more integrated solution,» concluded Harsin.