Volvo Penta and efficiency. The five Swedish declensions
Volvo Penta and efficiency. We all usually call it efficiency. But Volvo Penta has found a way to pursue the same goal, but with a different semantics: to maximize uptime. In Guthenburg they show five ways to go. Listen straight from their words (for first, refresh on Stage V). Volvo Penta and efficiency. Downsizing, rightsizing, […]
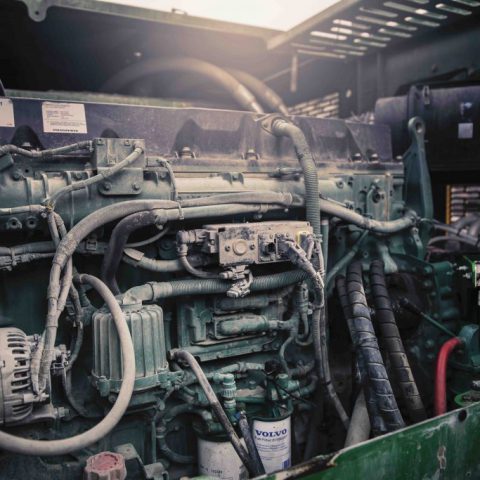
Volvo Penta and efficiency. We all usually call it efficiency. But Volvo Penta has found a way to pursue the same goal, but with a different semantics: to maximize uptime. In Guthenburg they show five ways to go. Listen straight from their words (for first, refresh on Stage V).
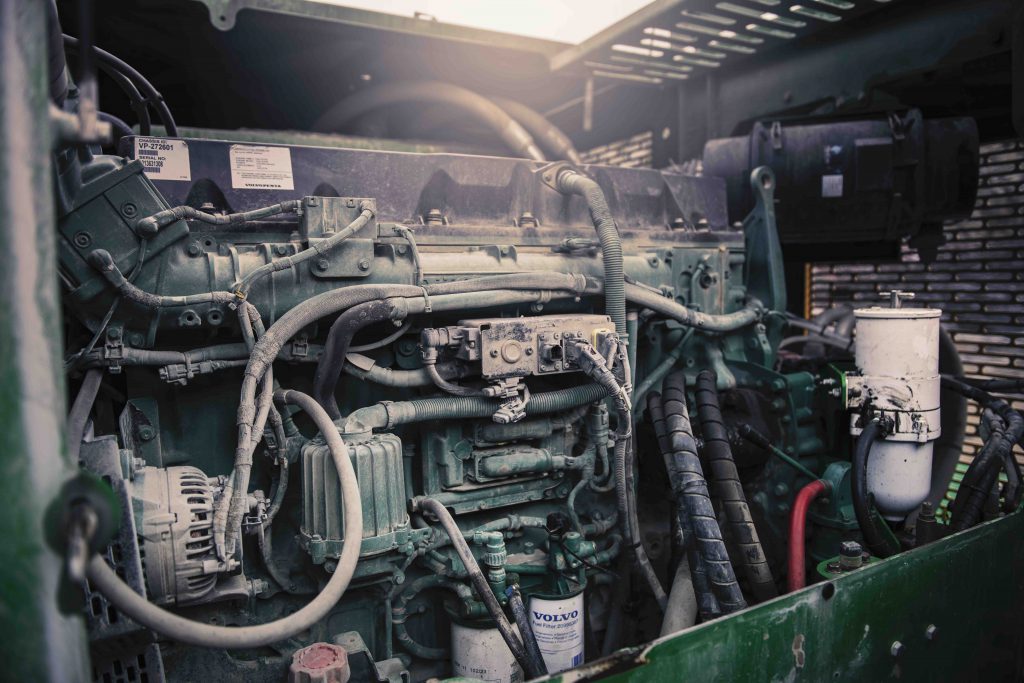
Volvo Penta and efficiency. Downsizing, rightsizing, etc etc
“When it comes to industrial engines, the right size very much depends on the application you’re working in. An engine that’s too small will result in average loads that are too high, and you’ll struggle to perform the equipment’s intended tasks. This will lead to increased wear on the engine and its components. However, if it’s too big, the equipment won’t run efficiently. That’s why it’s crucial to work with your engine manufacturer to find the right size for your application and usage to maximize uptime. At Volvo Penta, we work with our customers to perform simulations on factors such as speed and torque trace, and calculate an accurate description of how the engine should be sized for its workload.”
Talking about ATS
“Stage V emission legislation requires off-road engines up to 560 kW to have a diesel particulate filter (DPF) which captures and stores soot. Active regeneration – the process of burning off this soot – can cause significant downtime as it requires the engine to stop. This can be minimized by choosing the right diesel engine and aftertreatment system (EATS) concept to suit your specific needs.The intervals between regenerations can vary greatly between engine manufacturers and their EATS concepts. At Volvo Penta, we have a “Regeneration Zero” vision, which means that we’ve minimized the need for active regeneration as much as possible by maximizing the use of passive regeneration. Here, the soot accumulated in the DPF is burned off during normal machine operation, without the need for frequent active standstill regeneration. Through an optimized engine and EATS that work seamlessly together, we’ve increased uptime to keep customers’ machines operational and profitable.”
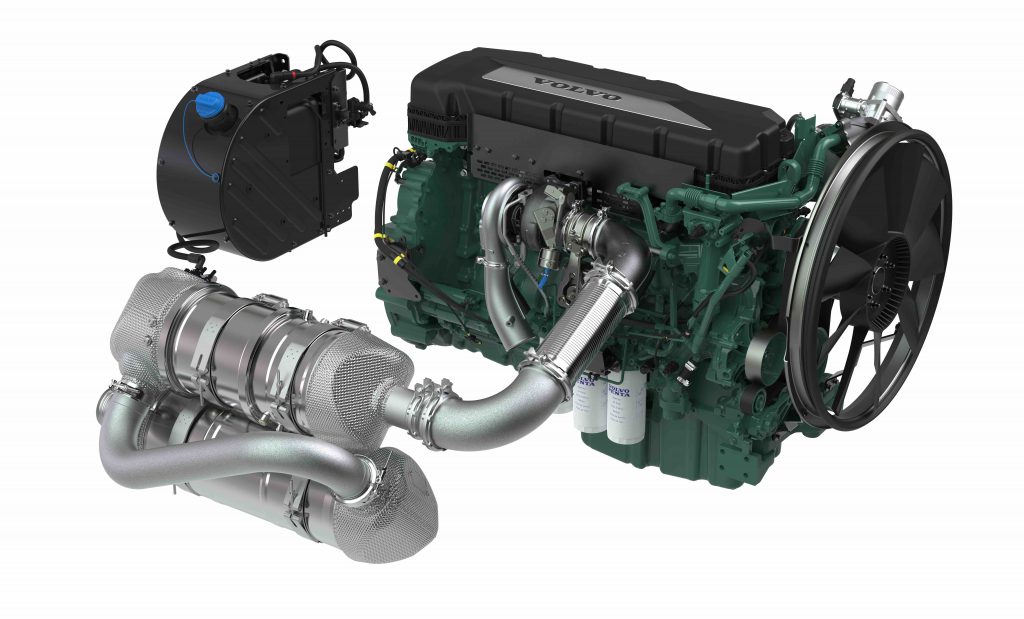
The importance of the aftermarket
“If something goes wrong, getting aftermarket support quickly is crucial to reducing downtime. Choosing an engine supplier that works with competent service providers who have the right spare parts at hand and can reach you quickly is vital. Things to discuss with your engine manufacturer include dealership coverage areas, call out service, product registration, service agreements and oil analysis.”
Human resources
“Operating your engine with maximum efficiency is key for longevity and uptime. Pushing the engine too hard and operating at too high RPM (revolutions per minute) can result in increased wear on components and higher fuel consumption. That’s why it’s important to train operators so they know the ideal RPM and engine loads for their application. This prevents downtime, and the cost savings will quickly repay the investment.”
Cool and connected
“Connectivity can increase uptime. Engines and components can generate vast amounts of data that can be used to analyze performance and report active or predicted faults. The data transmitted will also help to identify inefficiencies and will allow technicians to assess and diagnose an engine fault before going out to service it. Connectivity is already showing huge potential for improving uptime and will continue to grow in the coming years as suppliers, OEMs, technicians and operators are exploring how data can be used to establish new ways of working.”