Metal rubber anti-vibration systems: how to create a new product
T200160 metal rubber anti-vibration mounts. Have you ever wondered how a customized component is created? Patrini, who has been designing and manufacturing anti-vibration systems from high quality Italian raw materials since 1965, tells us the birth of a new product. PATRINI, SINCE 1965 AGAINST VIBRATIONS Reducing the vibrations of a diesel engine «Sometimes, the most […]
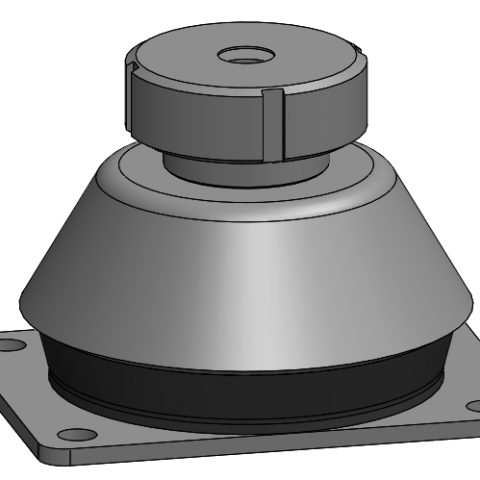
T200160 metal rubber anti-vibration mounts. Have you ever wondered how a customized component is created? Patrini, who has been designing and manufacturing anti-vibration systems from high quality Italian raw materials since 1965, tells us the birth of a new product.
PATRINI, SINCE 1965 AGAINST VIBRATIONS
Reducing the vibrations of a diesel engine
«Sometimes, the most challenging projects are born almost by chance and on the sly. This is the case with the T200160, a new metal rubber anti-vibration mount designed to reduce the vibrations of a large diesel engine under binding operating conditions.
The collaboration with the customer, in fact, was born almost by chance, from a simple contact through our website www.patrinigiacomo.it following a Google search. After a series of emails and phone calls, our Product Manager, together with the owner and Head of the Engineering Department, decided to visit the Spanish headquarters of the company. It was clear, in fact, that there was an interesting project to develop. At Patrini, we believe that meeting in person is fundamental to deepen the requirements, discuss them and build a relationship of mutual trust.
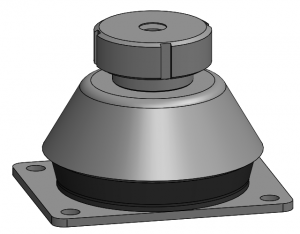
In-house production of metal rubber anti-vibration systems
The situation was challenging indeed: a totally new design for a very large diesel engine in an application subject to safety standards for human life, with a very small installation area, the need for preload on the anti-vibration mount and critical operating conditions. Furthermore, we knew that Patrini was not the only potential supplier.
Using our FEA (finite element analysis) and calculation system, we were able to identify the right metal rubber anti-vibration mount for this application and to produce the samples in a few days. Patrini, in fact, has in-house all the main production stages of metal rubber anti-vibration systems: metal parts forming, milling of the internal components, painting of the metal parts to allow the rubber/metal adhesion, rubber vulcanization. This allows us to be very fast and more competitive on the market.
ANOTHER PRODUCT BY PATRINI: T63W
Our compound supplier has also supported us in the project: he has made a special fireproof compound to meet the standards required by the application. Upon approval of the samples, the recipe will be ‘frozen’ and will remain unchanged throughout the production of this customer’s T200160 anti-vibration mounts. The collaboration with our suppliers is another winning card of Patrini’s philosophy. Our Quality System certified according to ISO 9001:2015 provides, in fact, the relationship with selected suppliers that are periodically audited.
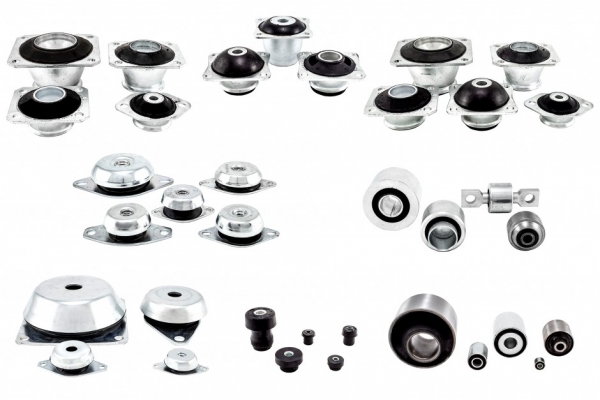
One million test cycles
So, after several evaluations and studies shared between the engineering departments, the time has finally come to produce and test the samples in our laboratory. Our dynamic testing machine was mainly used. The characterization of the metal rubber T200160 anti-vibration mount took place at the frequency from 0 to 50 Hertz, while the test cycles (around one million) took place between 3 and 5 Hertz. The results are very promising and we expect positive feedback. Now the prototypes are ready to be mounted on the customer’s engines and we are waiting for confirmation of our data in the field application.
Patrini has been producing metal rubber anti-vibration systems since 1965. Our mission is to create a collaborative relationship with customers to support them in their work by simplifying it».
Are you facing some annoying vibrations? Would you like to better evaluate your application?
FOR A TAILOR-MADE EVALUATION IN ONLY 48 HOURS, JUST CLICK THE BUTTON: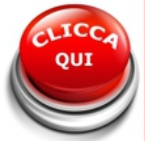