Patrini, since 1965 against vibrations
Vibrations? Patrini has the answer Patrini, antivibration since 1965 in the sign of customization, digitization and Made in Italy. Wherever there are moving parts and vibrations and distortions can occur. Wherever and however it happens, Patrini has the resources and the know how to tame the onset of these phenomena. Patrini in numbers? In 2017, […]
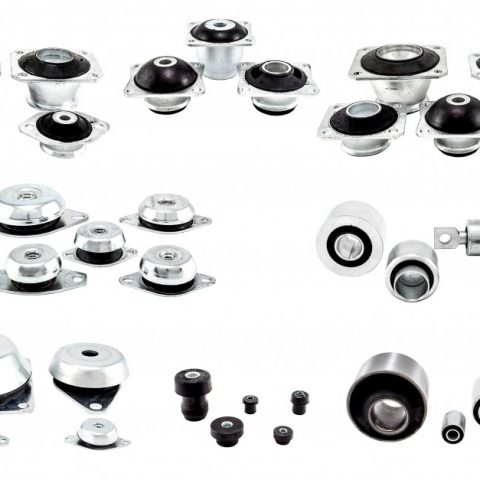
Vibrations? Patrini has the answer
Patrini, antivibration since 1965 in the sign of customization, digitization and Made in Italy. Wherever there are moving parts and vibrations and distortions can occur. Wherever and however it happens, Patrini has the resources and the know how to tame the onset of these phenomena.
Patrini in numbers? In 2017, the headquarter in Opera, in the neighborhood of Milan, produced 7 million and 700 thousand mounts. A figure of 9% progression compared to 2016. Focusing on the first quarter of this year, the amount already counts 3 million and 600 thousand. Figures that witness an exponential growth.
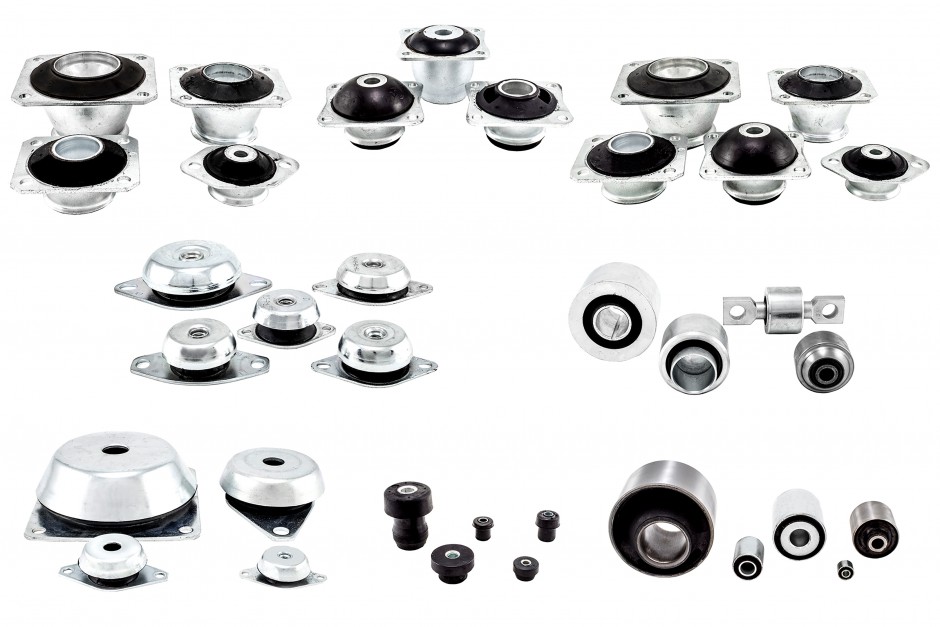
Intermediate life
Patrini has traditionally played an intermediary role. In Opera, however, the time has come to change, at least partially, the register. Why? We asked this directly to Walter Patrini, the CEO. «Our need to make ourselves more visible on the market is to create further synergies with the various users. We no longer need to be confined to the role of supplier of products in the catalog. The catalog should be used as a starting point to define the correct dimensions and fixings».
There is a metaphor that expresses the company’s application mission: tailoring. «We have the skills to make custom-made vibration dampers and we also know how to explain to OEMs the advantages of the tailoring of each product. This is the heart of the service we offer, not the indexing of catalog items! And we are structuring ourselves to expand and consolidate ourselves in this direction».
Which direction?
Patrini has strengthened its analytical and predictive capacity in three directions. The first leads to the newly designed testing room. The second to the new fatigue test machine. These two tools allow simulating a work cycle, practically in the whole length of life. The most recent example concerns a bush, which has endured up to 1,5 million cycles, stress tests that until January could not happen. The third is the portable 24-channel vibrational sensing device.
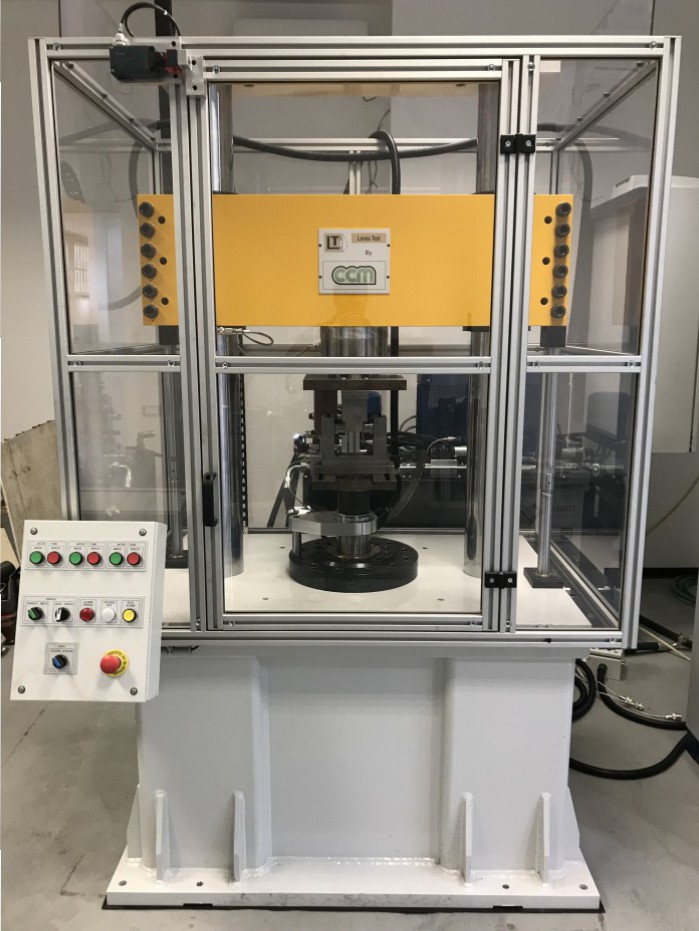
Which applications?
«If I answered all those on the market?» In fact, the answer could be enough, but to understand more: «From the engine (Kohler, Kubota), the body (for example the CNH and Same cabins), or the marine engines and generators (Mase, Genset). We also have a very strong connection with the suspension of the electric motors of the extractor hoods, which productively commits the company with more than 1,5 million pieces per year. In addition, we range from applications for wind farms, railways, sun beds, dentists’ chairs, coffee machines and coffee grinders. We are taking the first steps in the defense sector, using our philosophy for a very important customer».
Customization, 4.0 and Made in Italy
Everything is clear on customization. From Patrini’s perspective, the digitization or industry 4.0 is linked to the concept of personalization. «It is the management of data within the company to guarantee the benefit to the final customer». And the Made in Italy? Perhaps it would be more correct to call it ‘zero kilometers’.
The CEO proudly concludes: «We are a vertical company. We buy raw materials, steel, and rubber. For the rest, everything is built and generated in house. We only buy the screws and delegate the surface protection treatment of the metal to the outside. From 70 hours to 1,000 hours of salt spray. All this to provide the customer with an increasingly personalized service».